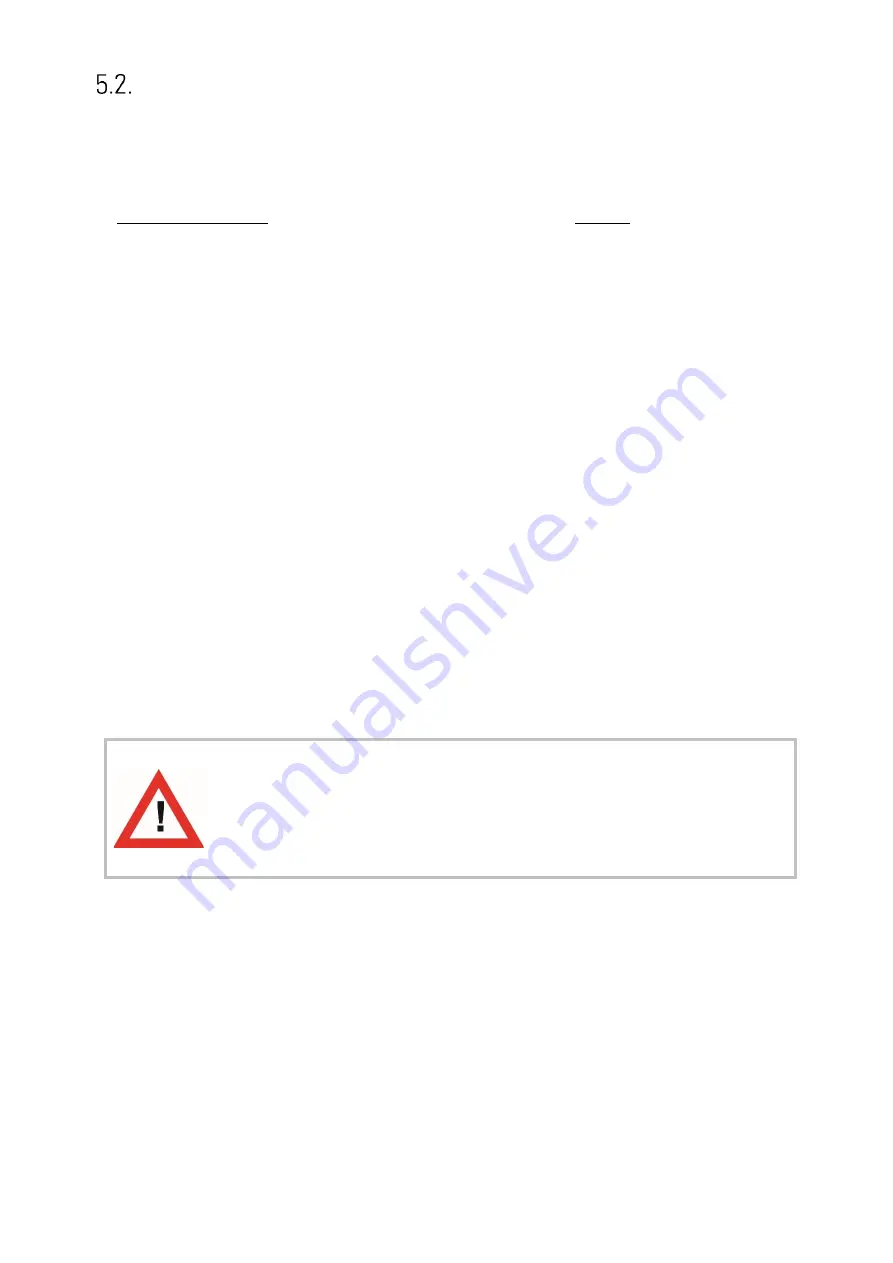
Fs340_02b_oi_e.docx / Nov-21
Page 15 / 49
System Configuration
As a master drive, either the motor of a feed roll or a measuring wheel equipped with an
incremental encoder is used.
The encoder resolutions should be at least 5 times higher than the maximum acceptable
cutting error.
At maximum line speed, the master encoder frequency should be at least about 1 kHz, for best
resolution of the analogue output. Moreover, the input frequency must not exceed the
maximum level of 300 kHz (RS422 and TTL differential encoder) or 200 KHz (HTL and TTL single-
ended encoders).
It is best to choose the ppr numbers of line and carriage encoders in a way to produce
frequencies in the same range. Acceptable ratios are in the range of
5:1 ... 1:1 ...1:5
Mismatching beyond 1:16 and 16:1 are not allowed. Where applicable, the (x1), (x2) or (x4)
hardware multiplication of the Master channel or the Slave channel may be used to adapt the
frequencies
The line encoder must be connected to input “Master” and the carriage encoder to input
“Slave”.
For speed reference of the carriage drive, the analogue output is used.
At any ti
me the controller needs a remote signal upon completion of the cut (“cut completed”)
to commence the return motion of the carriage.
It is necessary to adjust the carriage drive to its maximum dynamic response (no internal ramps,
no integral control loop, high proportional gain), because the FS340 and FS641 will generate
the ramps which the drive has to follow with no additional delay
For safety reasons it is mandatory to limit the traveling range of the
carriage by independent limit switches at both ends, in order to avoid
damage with carriage overshoot upon failure of the electronic control
system!