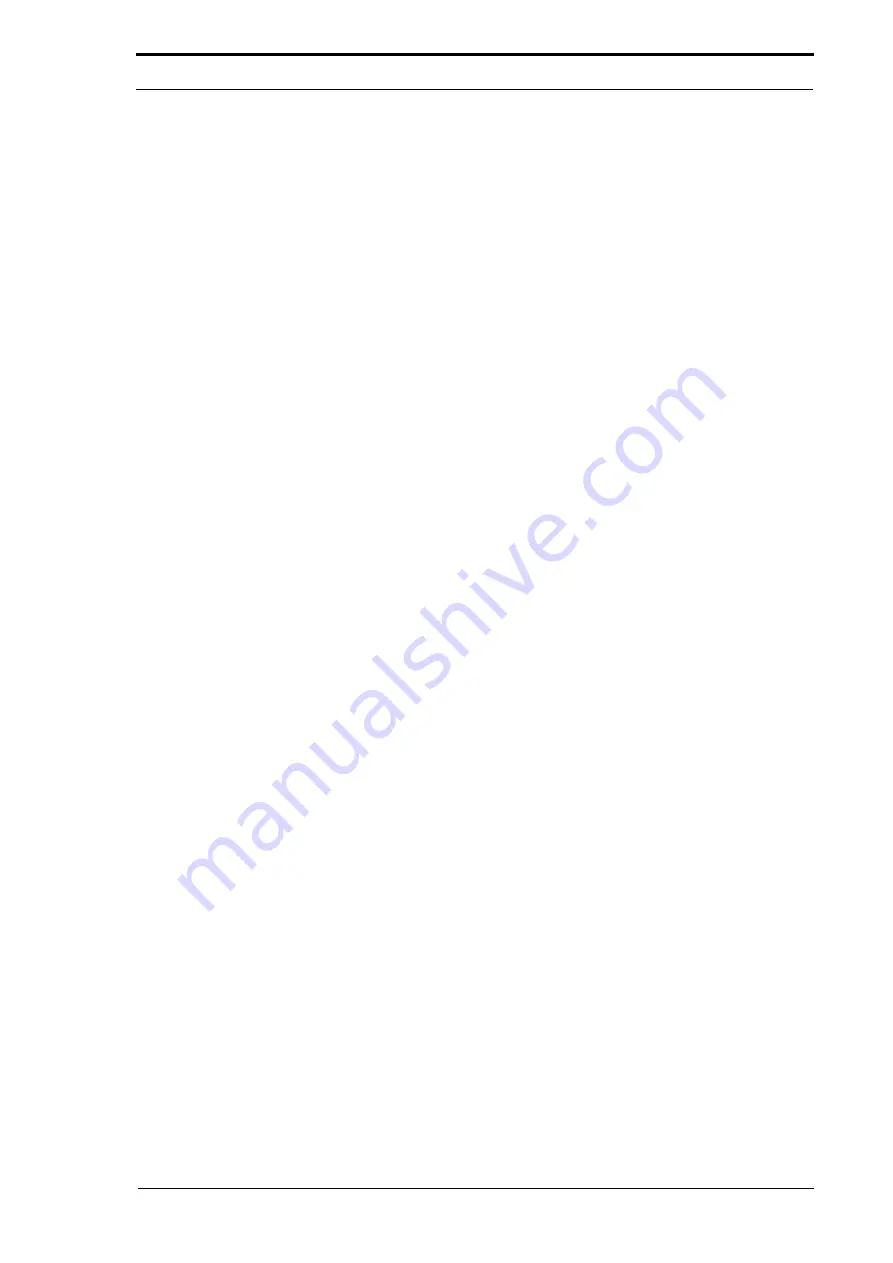
6. General Procedures - The Diagnostic Tools Pages
204
Morgana DocuMaster MFC - Service Manual
1:
Always use the inner sensor pair.
2:
Always use the middle sensor pair.
3.
Always use the outer sensor pair.
<Last Error>: The number code of the last error on the system.
‘A’ Set AUTO/MANUAL Mode (PWM control)
Sets the PWM control from the GUI CPU ON (AUTO mode) or OFF (MANUAL mode).
When in AUTO mode some commands, such as R, S and H, are not permitted.
An
Set the motor control mode to AUTO or MANUAL.
n = 0 MANUAL mode. Motor control is via H, R, S, etc, commands.
n = 1 AUTO mode. Motor control is via the PWM input from the GUI CPU.
‘Bx’ Blade Test Operations
A series of commands to control and test the crease blade.
Bn
Move the blade motor in steps. The value n may be positive (motor moves in normal
direction) or negative (motor moves in reverse direction).
BC
Do a complete cycle (movement is not at full speed).
BH
Move the blade to the home position.
BT
Move the blade to the t.d.c. (Top Dead Centre) position.
‘C’ Set Test Creases
Specifies up to three arbitrary crease positions for the next sheet through the creaser.
This will override any crease instructions set by the GUI CPU in AUTO mode.
Cn1, n2, n3
n1, n2 and n3 are the crease distances to be set in multiples of tenths of a millimeter.
There may be a maximum of three creases and the crease distances must be specified
in ascending order. If less than three creases are required omit n3, or n2 and n3.
Example:
Crease the next sheet at 50mm and 250mm.
C500,2500
‘E’ Clear or Set Current Error
Clear the current error when in MANUAL mode or generate an error.
E
Clear the current error. (The errors are cleared when the motors are run anyway).
En
Generate the error code and send the error code to the GUI CPU.
‘G’ Enter/Read Configuration Data
Read or change the current configuration parameters and save to or read from the
EEROM. Note that all changes are made to a RAM copy and the changes will be lost if
the power is turned OFF (i.e if you operate the E-Stop switch) unless they are saved to
the EEROM with the ‘GW’ command.
G?
Displays current configuration parameters from the temporary memory in the format,
#<Stretch trim>, <Skew mode>; <Inner lead trim>, <Inner offset>, <Inner scale>;
<Middle lead trim>, <Middle offset>, <Middle scale>; <Outer lead trim>, <Outer offset>,
<Outer scale>
GKn o,s
Sets the offset (o) and scale value (s) for the sensor pair specified by n. n=1 is inner
pair, n=2 is middle pair and n=3 is for the outer pair. This command does not affect the
sensor pair currently in use. The configuration changes are only made to RAM and
must be saved to EEROM with the ‘GW’ command before the MFC is turned off or
reset.
GR
Read the EEROM contents into current configuration RAM.
Summary of Contents for DocuMaster MFC
Page 8: ...CONTENTS vi Morgana DocuMaster MFC Service Manual ...
Page 9: ...Morgana DocuMaster MFC Service Manual 1 1 SECTION 1 Introduction ...
Page 27: ...Morgana DocuMaster MFC Service Manual 19 2 SECTION 2 Error Conditions ...
Page 43: ...Morgana DocuMaster MFC Service Manual 35 3 SECTION 3 Output Quality Problems ...
Page 46: ...3 Output Quality Problems Crease Quality 38 Morgana DocuMaster MFC Service Manual ...
Page 47: ...Morgana DocuMaster MFC Service Manual 39 4 SECTION 4 Service Procedures ...
Page 196: ...4 Service Procedures The MFC Maintenance Schedule 188 Morgana DocuMaster MFC Service Manual ...
Page 197: ...Morgana DocuMaster MFC Service Manual 189 5 SECTION 5 Parts Lists ...
Page 199: ...Morgana DocuMaster MFC Service Manual 191 6 SECTION 6 General Procedures ...
Page 221: ...Morgana DocuMaster MFC Service Manual 213 7 SECTION 7 Electrical and Control System ...
Page 259: ...Morgana DocuMaster MFC Service Manual 251 8 SECTION 8 Installation Manual ...
Page 266: ...8 Installation Manual Install the MFC 258 Morgana DocuMaster MFC Service Manual ...
Page 267: ......