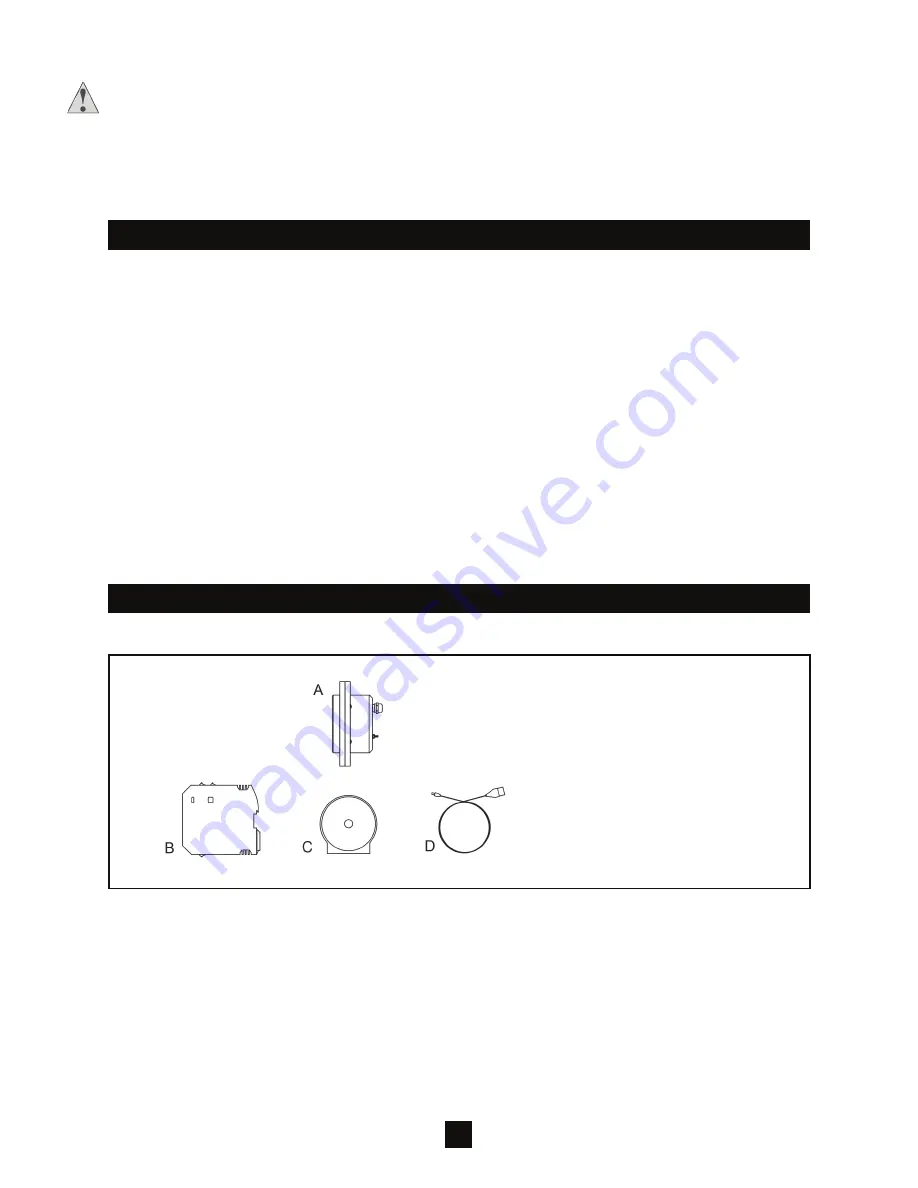
3
The
Humi
Core
™
Pro
in-line moisture measuring system for process monitoring guarantees trouble-free
measurement of the internal product moisture of solids and emulsions. The
Humi
Core
Pro
moisture sen-
sor circuitry principle is centered around an electrical high frequency field. With no material present, the
ambient air is the dielectric component of the electrical high frequency field. The dielectric constant of air
is one. When the process is active, bulk material passing in front of the sensor face displaces the ambient
air and becomes the dielectric for the electrical high frequency field. As the dielectric constant increases,
it also causes a change in the electrical high frequency field. That change is processed by the electronics,
is compensated for temperature, and is sent to the transmitter. Given the sensor output, a control system
can now quantify and display the moisture content of the material passing by the sensor face. The area of
material influence is typically up to 7.75 inches (200mm) from the sensor surface. Calibration is a simple
procedure which typically utilizes end user’s existing moisture measurement apparatus. The
Humi
Core
Pro
sensor can provide a high precision measurement (0.1% to 0.3% typical).
A complete
Humi
Core
Pro
system consists of the DIN-Rail transmitter and the moisture sensor. The DIN-
Rail transmitter allows for easy integration into an existing control system. Calibration software is provided.
In addition, up to 24 different product parameters can be recorded to accommodate product or process
changes.
The
Humi
Core
™
Pro
package consists of the components as depicted in Figure 1.
A) Sensor
B) Transmitter
C) Configuration Software
D) USB Cable
Figure 1
2.0 PRINCIPLE OF OPERATION
3.0 SYSTEM STRUCTURE
CAUTION: When handling this instrument, take care to exercise industry standard practices for electro-
static management. Sensitive electronic components may be damaged by electrical discharge that is far
below the limits of human perception. Such voltage occurs even when you touch a component or electrical
connections of a component and are not electrostatically discharged. The damage that occurs to a compo-
nent because of overvoltage usually cannot be detected immediately and may not become noticeable until
after a longer operating period.