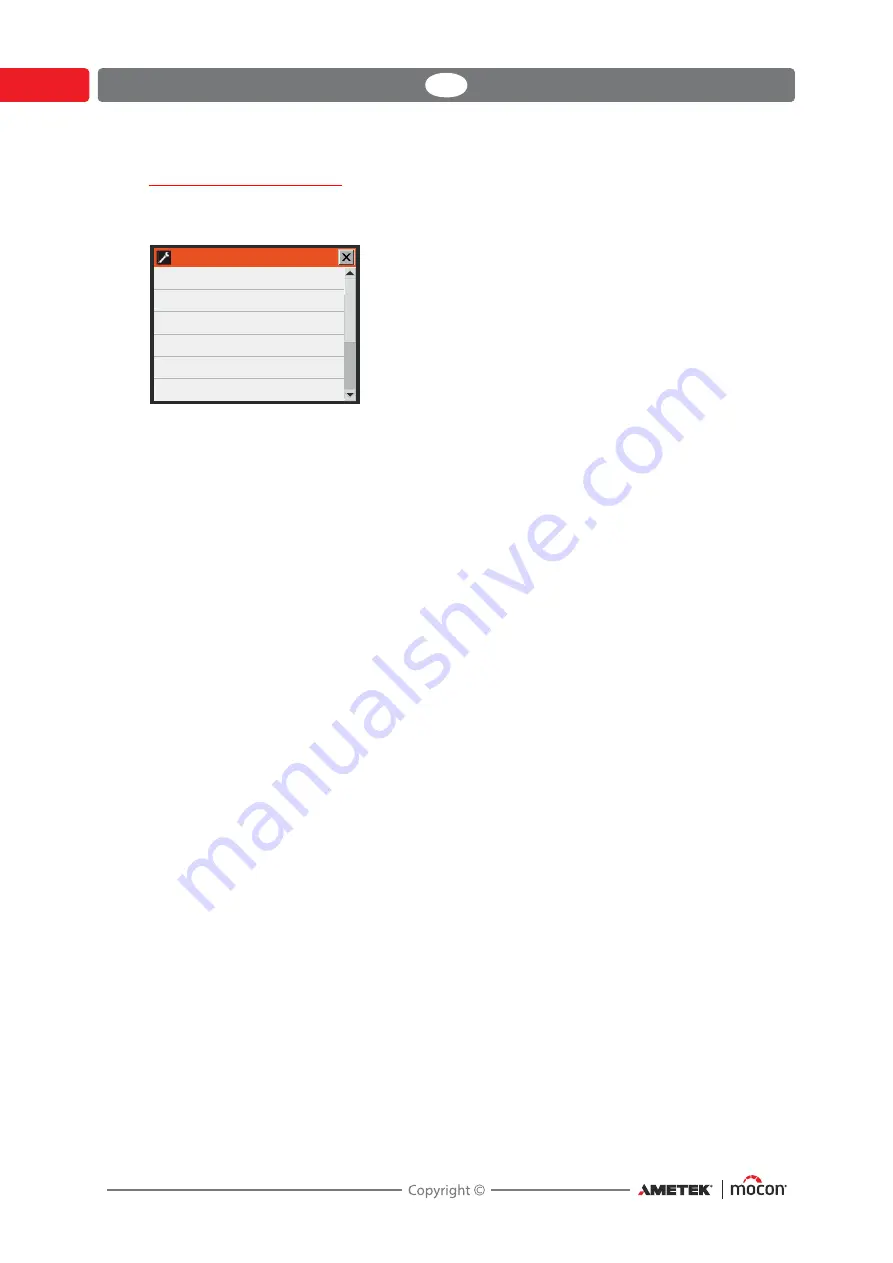
62
User Guide
EN
Dansensor
®
MAP Check 3
Vacuum
Buffer measure setup
Selecting
Buffer measuring setup
from the
General setup
menu will display a screen
showing the setup parameters for the buffer measuring.
Measure on buffer
No
No automatic buffer measurement is performed.
Start up
An automatic buffer measurement is performed
when device is switched into measuring mode.
Always
An automatic buffer measurement is performed
when device is switched into measuring mode and
also when a new product is selected while in
measuring mode.
Allow manual
No
No manual measurement is allowed
measuring
When ready
A manual buffer measurement can only be started
when the device is in Ready mode.
Always
A manual buffer measurement can always be started.
Online measuring will be disabled while buffer
measurement runs.
Buffer measure time
The time that the device measures on the buffer tank. Ensure that
the set time allows the gas to reach the sensor. A higher pressure and
longer hose requires for a longer measuring time.
Hold Alarms
Yes
If a buffer measurement is above or below the set
O
2
%/CO
2
% limits, the alarm relay is activated and
remains activated until a new measurement has
been performed where the result is within the limits.
No
The alarm relay is activated for 4 secs.
Hold Warnings
Yes
If a buffer measurement is above or below the set
O
2
%/CO
2
% limits, the warning relay is activated and
remains activated until a new measurement has
been performed where the result is within the limits.
No
The warning relay is activated for 4 secs.
Buffer measure delay
(Parameter only appears when “External mixer connected” is set to
“Yes” in the “external mixer settings” menu.)
Enter number of seconds to delay measuring after start of the buffer
pressure measurement.
The delay should ensure that the mixer has sufficient time to fill the
buffer tank before measurement starts.
#VGGFSNFBTVSFTFUVQ
.FBTVSFPOCVGGFS
"MMPXNBOVBMNFBTVSJOH
#VGGFSNFBTVSFUJNF
)PME"MBSNT
)PME8BSOJOHT
#VGGFSNFBTVSFEFMBZ
/P
"MXBZT
TFD
/P
/P
TFD
Summary of Contents for AMETEK Dansensor MAP Check 3 Vacuum
Page 1: ...P N 320598 G 11 2019 UserGuide 7BDVVN...
Page 2: ...This blank page has been inserted to enable double sided printing of the document...
Page 4: ...2 User Guide EN Dansensor MAP Check 3 Vacuum P N 320598 G 11 2019...
Page 8: ...6 User Guide EN Dansensor MAP Check 3 Vacuum P N 320598 G 11 2019...
Page 12: ...10 User Guide EN Dansensor MAP Check 3 Vacuum P N 320598 G 11 2019...
Page 20: ...18 User Guide EN Dansensor MAP Check 3 Vacuum P N 320598 G 11 2019...
Page 54: ...52 User Guide EN Dansensor MAP Check 3 Vacuum P N 320598 G 11 2019...
Page 76: ...74 User Guide EN Dansensor MAP Check 3 Vacuum P N 320598 G 11 2019...
Page 84: ...82 User Guide EN Dansensor MAP Check 3 Vacuum P N 320598 G 11 2019...
Page 91: ...This blank page has been inserted to enable double sided printing of the document...