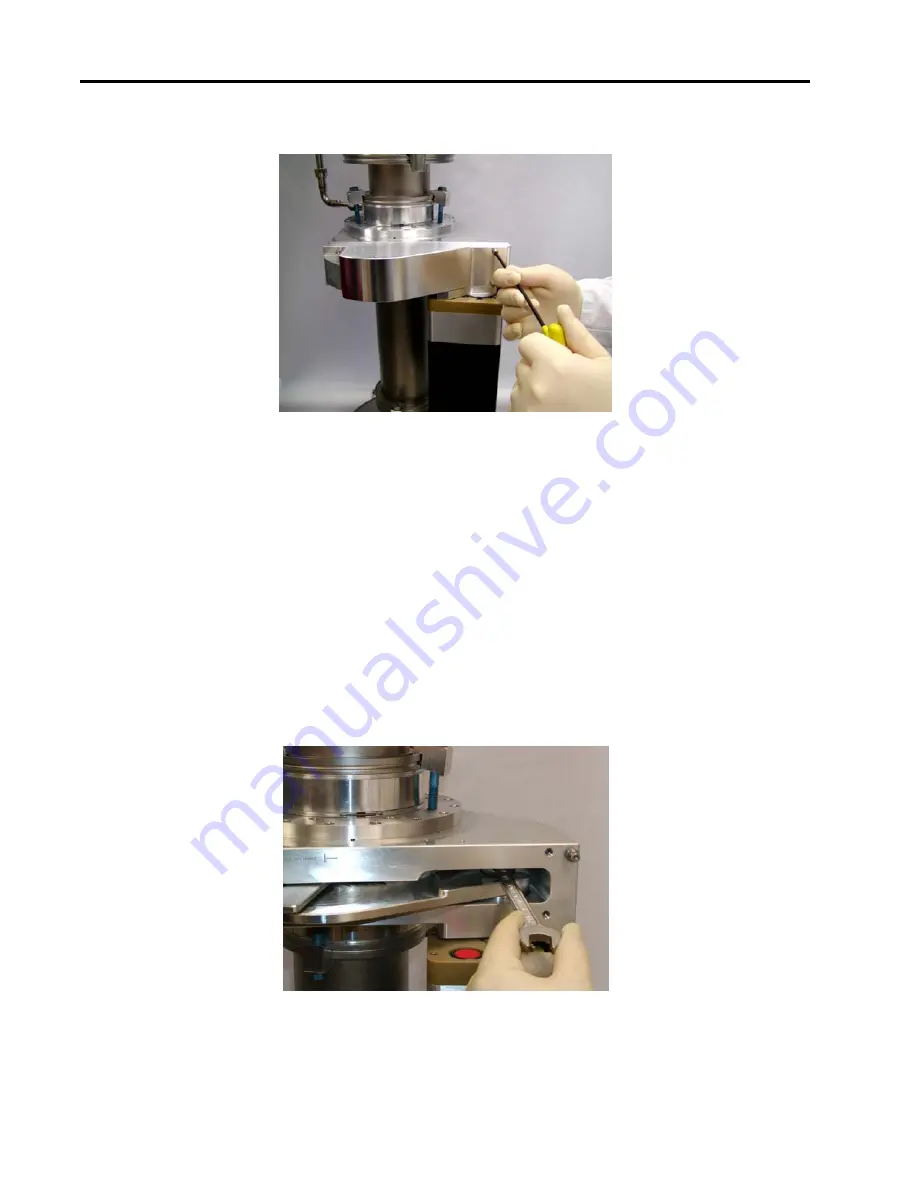
Chapter Five: Maintenance and Troubleshooting
Preventive Maintenance
38
3.
Loosen the valve cover screws (4) and remove the cover. Refer to Figure 16.
Figure 16: Four (4) Valve Cover Screws
4.
Select the
Pendulum Maintenance Mode Screen
on the tool computer.
5.
At the
Pendulum Maintenance Mode Screen,
select the “
Select Position Control Mode
” command.
6.
At the
Pendulum Maintenance Mode Screen,
select the “
Move Gate to 50 Percent Position
” command.
(This will move the gate to the 50% position and allow access to the bolt(s) holding in the gate.)
7.
Observe the bolt(s) attaching the gate to the main shaft. If there is only one bolt, skip to Step 8.
Otherwise, loosen the outer bolt with a ½” open end wrench. The outer bolt is the bolt located farthest
from the centerline of the valve bore.
8.
At the
Pendulum Maintenance Mode Screen
, select the “
Move Gate to 100 Percent Position
” command.
(This will move the gate to the 100%, full open, position and allow access to the bolt(s) holding in the
gate.)
9.
Loosen the remaining bolt attaching the gate to the main shaft (using a ½” open end wrench). Refer to
Figure 17.
Figure 17: Gate Bolt
10.
Remove the gate.
Summary of Contents for T3PIA
Page 3: ...MKS Type T3PIA Pendulum Valve With Analog TTL Interface...
Page 8: ...viii This page intentionally left blank...
Page 27: ...Electrical Information Chapter Two Installation 19 Figure 4 Top Panel of the T3P Unit...
Page 32: ...Chapter Two Installation Startup 24 This page intentionally left blank...
Page 60: ...Appendix C Dimensions 52...
Page 61: ...Appendix C Dimensions 53...
Page 62: ...Appendix C Dimensions 54...
Page 63: ...Appendix C Dimensions 55...
Page 64: ...Appendix C Dimensions 56...
Page 65: ...Appendix C Dimensions 57...
Page 66: ...Appendix C Dimensions 58...
Page 67: ...Appendix C Dimensions 59...
Page 68: ...Appendix C Dimensions 60...
Page 70: ...Index 62...