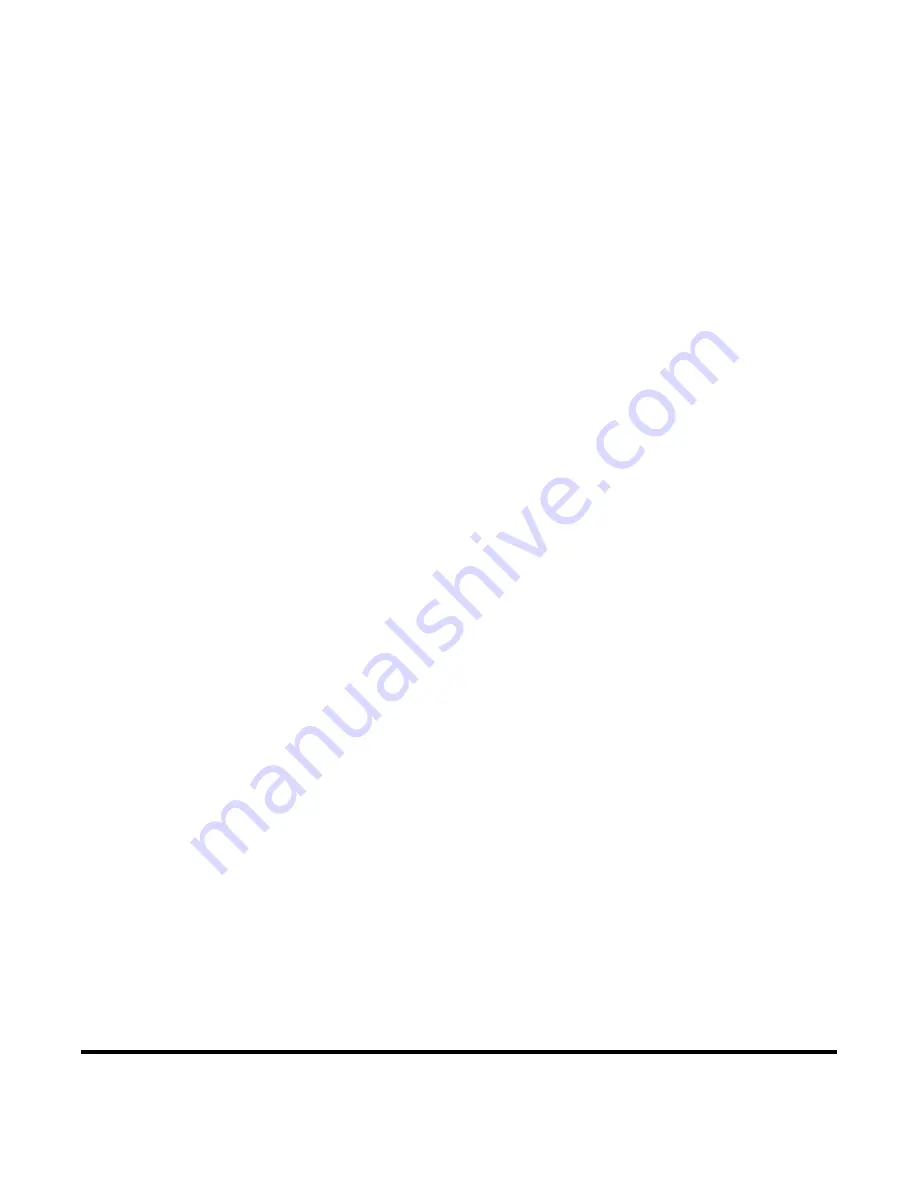
ISA-4001CR INVERTER POWER SUPPLY
990-364
ix
SAFETY PRECAUTIONS
General
This instruction manual describes the operation and maintenance of the Power Supply
and provides instructions relating to its SAFE use. Procedures described in this manual
must
be performed as detailed by QUALIFIED and TRAINED personnel.
For SAFETY, and to effectively take advantage of the full capabilities of the Power
Supply, please read this instruction thoroughly
before
attempting to use it.
After reading this manual, retain it for future reference when any questions arise
regarding the proper and SAFE operation of the Power Supply.
Operation
Procedures other than those described in this manual or not performed as prescribed in
this manual, may expose personnel to
electrical shock
or
DEATH
.
When operating any welder,
always
wear appropriate personal protective gear.
Maintenance/Service
Before performing any maintenance on the Inverter Power Supply, read
Chapter 5,
Maintenance
thoroughly. Use the appropriate tools for terminating the connecting
cables, being careful not to nick the wire conductors.
Do
not
modify the Power Supply without prior written approval from Miyachi Unitek.
HIGH VOLTAGE
is used in the operation of this equipment.
DEATH ON CONTACT
may result if personnel fail to observe the
safety precautions labeled on the equipment and noted in this manual.
WHEN WELDING
always
wear safety glasses.
Summary of Contents for ISA Series
Page 16: ...CHAPTER 1 SYSTEM DESCRIPTION ISA 4001CR INVERTER POWER SUPPLY 1 4 990 364 ...
Page 22: ......
Page 30: ......
Page 44: ......
Page 48: ......
Page 62: ......
Page 76: ......
Page 87: ...APPENDIX C SYSTEM TIMING ISA 4001CR INVERTER POWER SUPPLY 990 364 C 11 Pulsation Pulsation ...
Page 108: ......
Page 112: ......
Page 114: ......
Page 116: ......
Page 118: ......