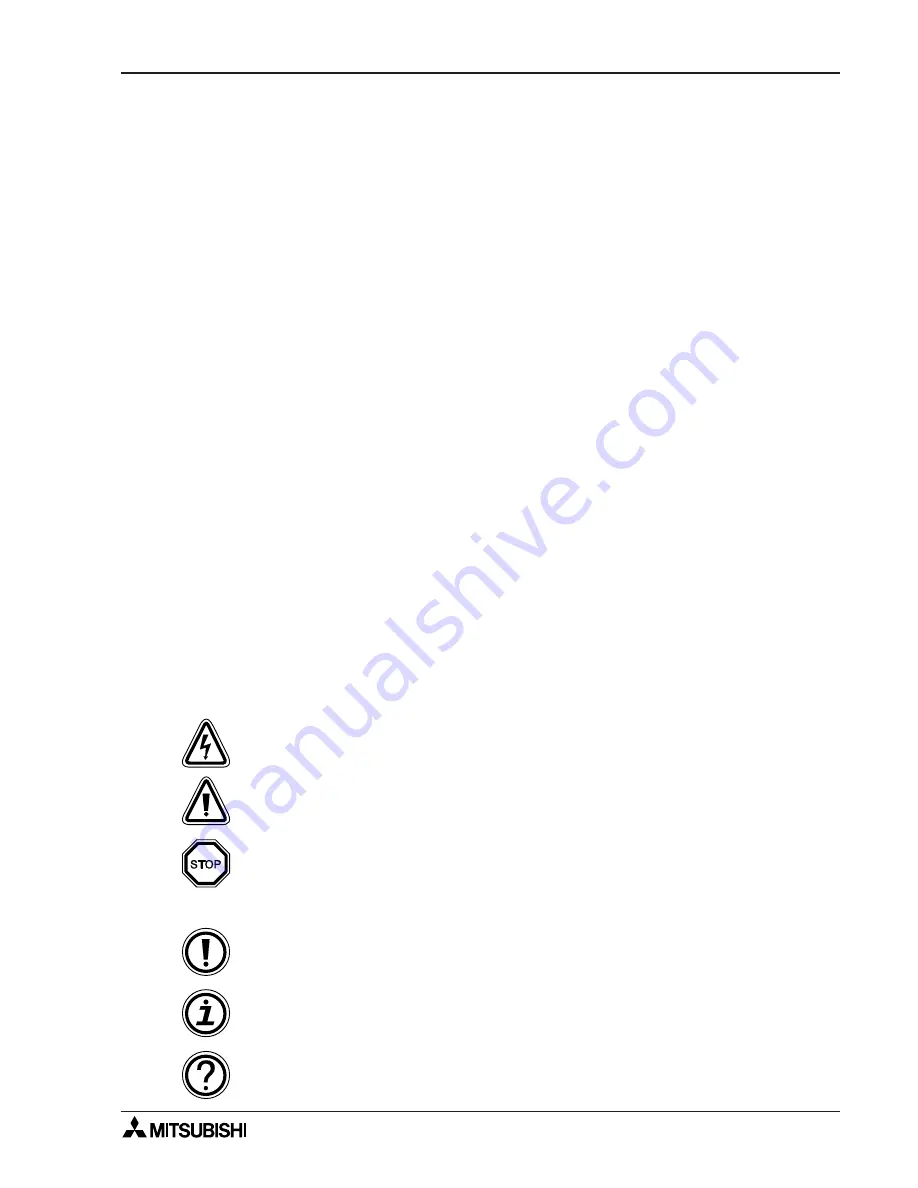
iii
FX-10GM POSITIONING CONTROLLER
Guidelines for the safety of the user and protection of the FX-10GM unit
This manual provides information for the use of the FX-10GM unit. The manual has
been written to be used by trained and competent personnel. The definition of such a
person or persons is as follows;
a)
Any engineer who is responsible for the planning, design and construction of
automatic equipment using the product associated with this manual should be of
a competent nature,trained and qualified to the local and national standards
required to fulfill that role. These engineers should be fully aware of all aspects
of safety with regards to automated equipment.
b)
Any commissioning or service engineer must be of a competent nature,trained
and qualified to the local and national standards required to fulfill that job. These
engineers should also be trained in the use and maintenance of the completed
product. This includes being completely familiar with all associated documentation
for the said product. All maintenance should be carried out in accordance with
established safety practices.
c)
All operators of the completed equipment should be trained to use that product in
a safe and co-ordinated manner in compliance to established safety practices.
The operators should also be familiar with documentation which is connected
with the actual operation of the completed equipment.
Note: the term 'completed equipment' refers to a third party constructed device which
contains or uses the product associated with this manual.
Notes on the symbology used in this manual
At various times through out this manual certain symbols will be used to highlight
points of information which are intended to ensure the users personal safety and protect
the integrity of equipment. Whenever any of the following symbols are encountered its
associated note must be read and understood. Each of the symbols used will now be
listed with a brief description of its meaning.
Software warning
Indicates a point of interest or further explanation
Indicates a special point which the user of the associate software element
should be aware of
Indicates special care must be taken when using this element of software
Hardware warnings
Indicates that the identified danger could POSSIBLY cause physical and
property damage.
Indicates that the identified danger WILL cause physical and property
damage.
Indicates a point of further interest or further explanation.