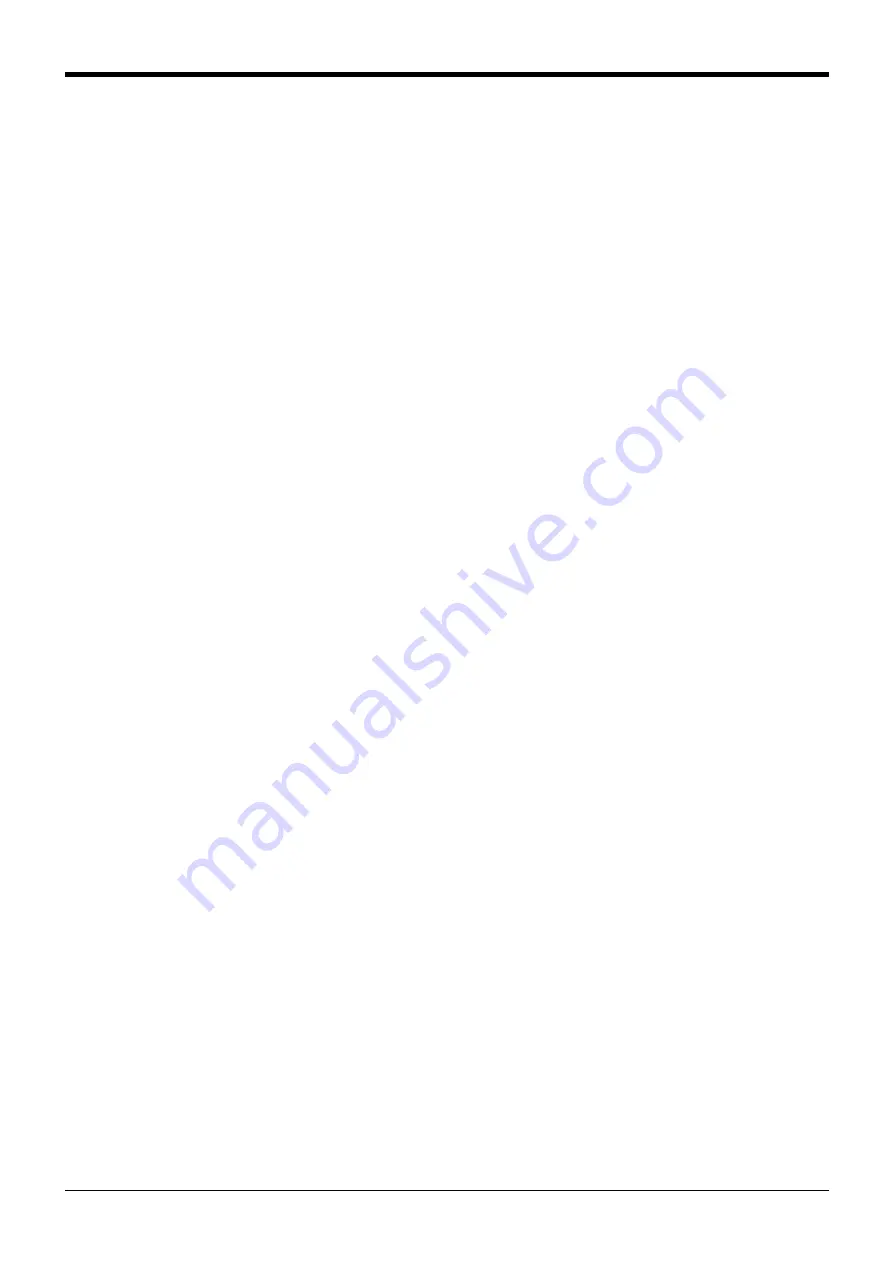
6Safety
Safety 6-130
(4) Training
・ Train the operators about the operations, maintenance and safety required for the robot work.
・ Only trained and registered operators must operate the robot.
Participation in the "Special training for industrial robots" sponsored by the Labor Safety and Sanitation Com
-
mittee, etc., is recommended for safety training.
(5) Daily inspection and periodic inspection
・ Always inspect the robot before starting daily operations and confirm that there are no abnormalities.
・ Set the periodic inspection standards in view of the robot's ambient environment and operation frequency, and
perform periodic inspections.
・ Make records when periodic inspections and repairs have been done, and store the records for three or more
years.
6.1.4 Safety measures for automatic operation
(1) Install safety fences so that operators will not enter the operation area during operation and indicate that
automatic operation is in progress with lamps, etc.
(2) Create signals to be given when starting operation, assign a person to give the signal, and make sure that the
operator follows the signals.
6.1.5 Safety measures for teaching
Observe the following measures when teaching, etc., in the robot's operation range.
(1) Specify and follow items such as procedures related to teaching work, etc.
(2) Take measures so that operation can be stopped immediately in case of trouble, and measures so that oper
-
ation can be restarted.
(3) Take measures with the robot start switch, etc., to indicate that teaching work is being done.
(4) Always inspect that stop functions such as the emergency stop device before starting the work.
(5) Immediately stop the work when trouble occurs, and correct the trouble.
(6) Take measures so that the work supervisor can immediately stop the robot operation when trouble occurs.
(7) The teaching operator must have completed special training regarding safety. (Training regarding industrial
robots and work methods, etc.)
(8) Create signals to be used when several operators are working together.
6.1.6 Safety measures for maintenance and inspections, etc.
Turn the power OFF and take measures to prevent operators other than the relevant operator from pressing the
start switch when performing inspections, repairs, adjustments, cleaning or oiling.
If operation is required, take measures to prevent hazards caused by unintentional or mistaken operations.
(1) Specify and follow items such as procedures related to maintenance work, etc.
(2) Take measures so that operation can be stopped immediately in case of trouble, and measures so that oper
-
ation can be restarted.
(3) Take measures with the robot start switch, etc., to indicate that work is being done.
(4) Take measures so that the work supervisor can immediately stop the robot operation when trouble occurs.
(5) The operator must have completed special training regarding safety. (Training regarding industrial robots and
work methods, etc.)
(6) Create signals to be used when several operators are working together.
Summary of Contents for CR800 Series
Page 2: ......
Page 154: ...Appendix 141 Specifications discussion material 7Appendix ...
Page 155: ......