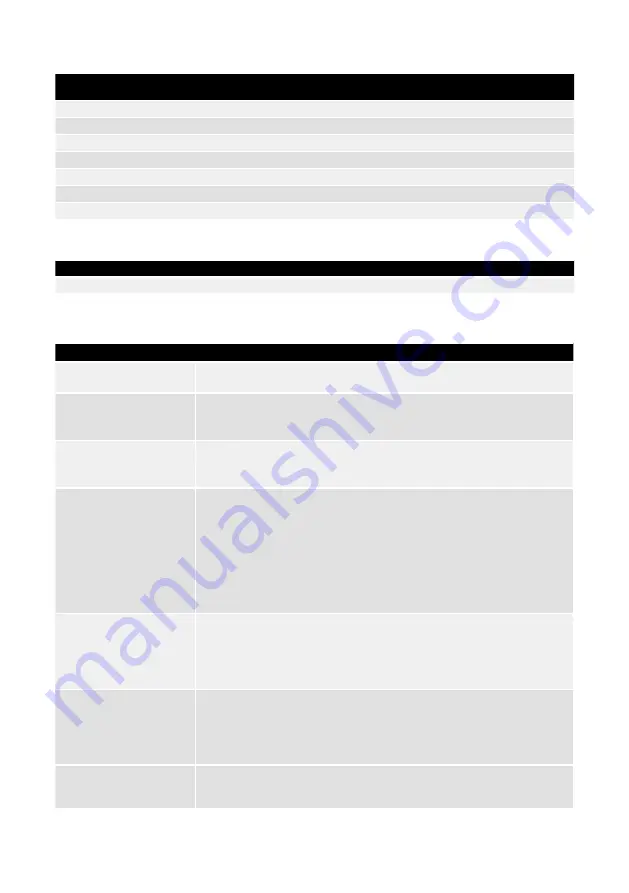
14
Mirka® AIROS • 77 mm (3"), 125 mm (5") & 150 mm (6") • Electrical manual
Troubleshooting guide
Symptom
Recommended procedures
Motor drive does not
power on.
• Check that 48 VDC is present on J2 and that the polarity is correct.
Tool does not start.
• Check that the motor drive is in ON-state (D14 is not blinking).
• Check that the motor drive is in RUN-state (D4 is lit green).
• Check the cable assembly for the tool: are the pins properly connected?
Tool suddenly stops.
• Check the alarm status flag.
• Check the motor drive and tool temperatures.
• Check if the tool is being overloaded.
Modbus RTU
communication is not
working.
• Check the baud rate, parity, stop bits and data bits.
• Check the transmit/receive indicators D29 and D30; these blink when there is
activity on the bus.
• Check that the A-pin and B-pin are connected properly.
• Check whether addition of a terminating resistor (JP2), A-pin pull-down resistor
(JP3), B-pin pull-up resistor (JP4) solves the issue.
• Check that JP1 is not set.
• Check the slave address (set the JP13 jumper and use indicators D2–D3, D17–D22
to read the current address).
Profinet I/O gateway
communication is not
working.
• Check the gateway network configuration.
• Check the gateway Modbus RTU to Profinet I/O mapping configuration.
• Check the 24 VDC power supply.
• Check the Modbus RTU adapter cable is connected properly.
• Check that JP1 is not set.
Digital speed controller
interface is not working.
• Check that JP1 is not set.
• Check that JP8, JP9, JP10, JP11 and JP12 are set.
• Check the voltage on a high input, it should be between 15–33 VDC.
• Check the voltage on a low input, it should be close to zero volts.
• Check the GND connection.
Indicator D36 is lit red,
or the tool speed is too
fast/slow.
• Check C+/C-/P+/P– wiring on J3.
Speed set-point display
RPM
BIT 8
D22
BIT 7
D21
BIT 6
D20
BIT 5
D19
BIT 4
D18
BIT 3
D17
BIT 2
D3
BIT 1
D2
≥ 4,000
–
OFF
OFF
OFF
OFF
OFF
OFF
ON
≥ 5,000
–
OFF
OFF
OFF
OFF
OFF
ON
ON
≥ 6,000
–
OFF
OFF
OFF
OFF
ON
ON
ON
≥ 7,000
–
OFF
OFF
OFF
ON
ON
ON
ON
≥ 8,000
–
OFF
OFF
ON
ON
ON
ON
ON
≥ 9,000
–
OFF
ON
ON
ON
ON
ON
ON
≥ 10,000
–
ON
ON
ON
ON
ON
ON
ON
Modbus RTU slave address display
BIT 8
BIT 7
BIT 6
BIT 5
BIT 4
BIT 3
BIT 2
BIT 1
D22
D21
D20
D19
D18
D17
D3
D2