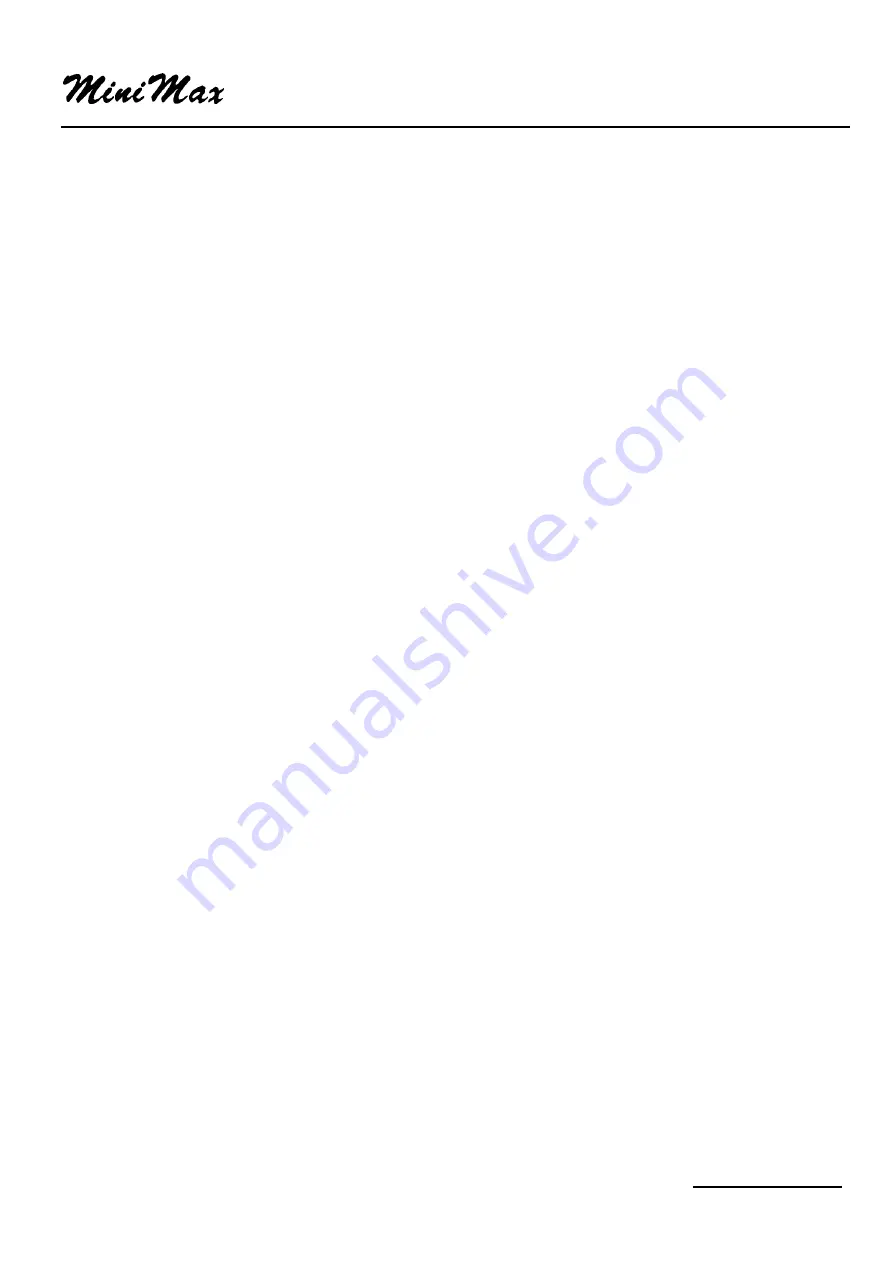
GENERAL
T1 1.11
1
1-7
1-7
1-7
1-7
1-7 SAFETY RULES
SAFETY RULES
SAFETY RULES
SAFETY RULES
SAFETY RULES
Carefully read this manual before starting the machine.
In the proper Section concerning the adjustments the relative guards and their use are described.
This machine has been built to ensure the highest safety degree
as well the best perfomance.
The manufacturer is not responsible for the damages due to modifications carried out on the
machine.
Final safety depends on you.
Any machine tool may be be potentionaly dangerous: do not forget it!
PERSONAL SAFETY
PERSONAL SAFETY
PERSONAL SAFETY
PERSONAL SAFETY
PERSONAL SAFETY
1- Experience teaches that there are various objects on a person that can cause injuries; take off
rings, watches, bracelets; button your sleeves tightly around your wrists, take off ties that could
be caught in tight places, keep hair gathered underneath aproper nets (cap, elastics, hair pins).
Use prescribed footwear usually recommended by all countries.
2- Always use glasses, protective shields for your eyes.
3- Use proper means for ear protection (plugs etc.)
MACHINE SAFETY
MACHINE SAFETY
MACHINE SAFETY
MACHINE SAFETY
MACHINE SAFETY
1- Be extremely careful when starting any working cycle
2- Never start the machine without having properly installed the covers for the spindle, the belts,
chains etc.
3- Before starting the machine make sure that the worktable is free from parts which do not relate
to the working
4- Work only when all guards are in place.
5- Do not machine workpieces too smal or too big for the machine.
6- Before fitting the spindle make sure that each support surface is clean, free from dents and
perfectly flat.
7- Make sure that the cutters are perfectly balanced, sharp and well clamped.
Not sharp tools reduce not only the quality of the finished piece but they increase the piece
kickback danger.
8- Never use deformed cutters and do not exceed the speed limit indicated on them and prescribed
by tool manufacturer or by MINI MAX.
9- Use only tools in accordance with prEN 847-1 and suitable for manual feed.
10- The use of circular saw blades is not permitted
11- The tool shall be adjusted with the machine off and with proper instruments (gauge, comparator).
12- It is necessary to connect all suction hoods to the suction system.
By taking proper measures make sure that when you start the motor the suction system is
switched on at the same time.
Summary of Contents for FORMULA T1
Page 22: ...T1 2 3 2 2 1 2 2 kg _____ 475 ...
Page 24: ...T1 2 5 2 2 6 2 5 B T13216 E D E K D C ...
Page 26: ...T1 2 7 2 MORSE1 L1 L2 L3 N PE P 2 7 ...
Page 29: ...INSTALLATION 2 10 T1 BF NGB2 ...
Page 32: ...T1 3 3 3 A1 A2 F L M A A1 A2 B A F B V V 3 1 P 3 2 ...
Page 34: ...T1 3 5 3 L H 3 4 A1 A2 F L M A A1 A2 B A F 3 4a ...
Page 35: ...MACHINE SETTING AND USE 3 6 T1 BF NGB3 ...
Page 38: ...T1 7 3 7 7 2 7 3 ALBE1 ALBE2 D B S A C B A Z T 7 1 A F P bf7 4 ...
Page 40: ...T1 7 5 7 B A 7 4 ...
Page 42: ...T1 7 7 7 7 6c 7 6a 7 6b ...
Page 44: ...T1 7 9 7 7 7 7 8 L S N C G P H ...
Page 46: ...T1 7 11 71 L H A M P C 7 9 ...
Page 48: ...T1 7 13 71 7 13 REGISTR M 7 12 H M P L I T F R ...
Page 50: ...T1 7 15 71 CUFFI4 F R 7 14 7 15 I T REGISTR M H M P L ...