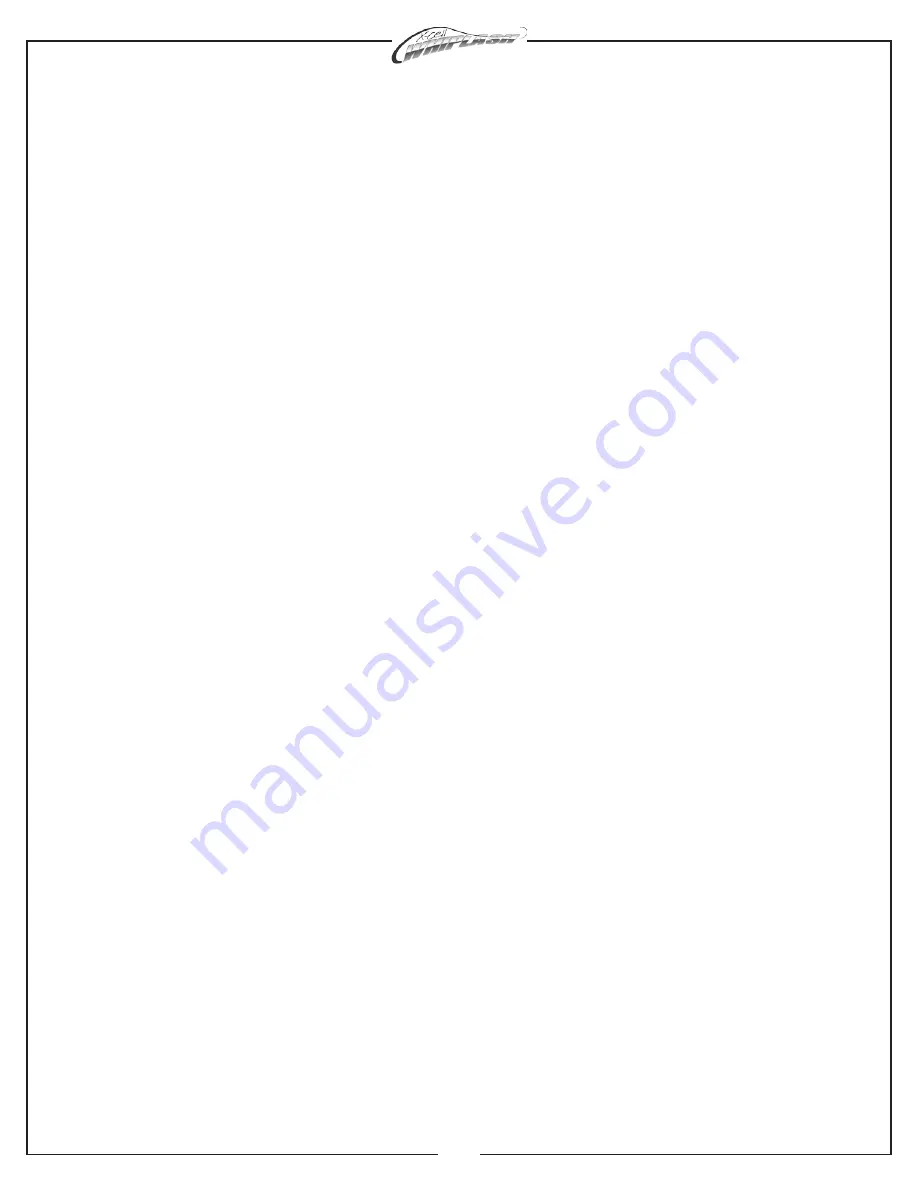
Academy of Model Aeronautics
Miniature Aircraft highly recommends joining the Academy of Model Aeronautics (AMA).
• AMA is the Academy of Model Aeronautics.
• AMA is the world’s largest model aviation association, representing a membership of more than 195,000
from every walk of life, income level and age group.
• AMA is a self-supporting, non-profit organization whose purpose is to promote development of model
aviation as a recognized sport and worthwhile recreation activity.
• AMA is an organization open to anyone interested in model aviation.
• AMA is the official national body for model aviation in the United States. AMA sanctions more than one
thousand model competitions throughout the country each year and certifies official model flying records on
a national and international level.
• AMA is the organizer of the annual National Aeromodeling Championships, the world’s largest model
airplane competition.
• AMA is the chartering organization for more than 2,500 model airplane clubs across the country. AMA offers
its chartered clubs official contest sanction, insurance, and assistance in getting and keeping flying sites.
• AMA is the voice of its membership, providing liaison with the Federal Aviation Administration, the Federal
Communications Commission, and other government agencies through our national headquarters in Muncie,
Indiana. AMA also works with local governments, zoning boards, and parks departments to promote the
interests of local chartered clubs.
• AMA is an associate member of the National Aeronautic Association. Through NAA, AMA is recognized by
the Fédération Aéronautique Internationale (FAI), the world governing body of all aviation activity, as the only
organization which may direct U.S. participation in international aeromodeling activities.
For more detailed information, contact the Academy of Model Aeronautics
5161 E. Memorial Drive, Muncie, Indiana, 47302
or telephone (800) 435-9262.
You may also visit the AMA website at www.modelaircraft.org
4