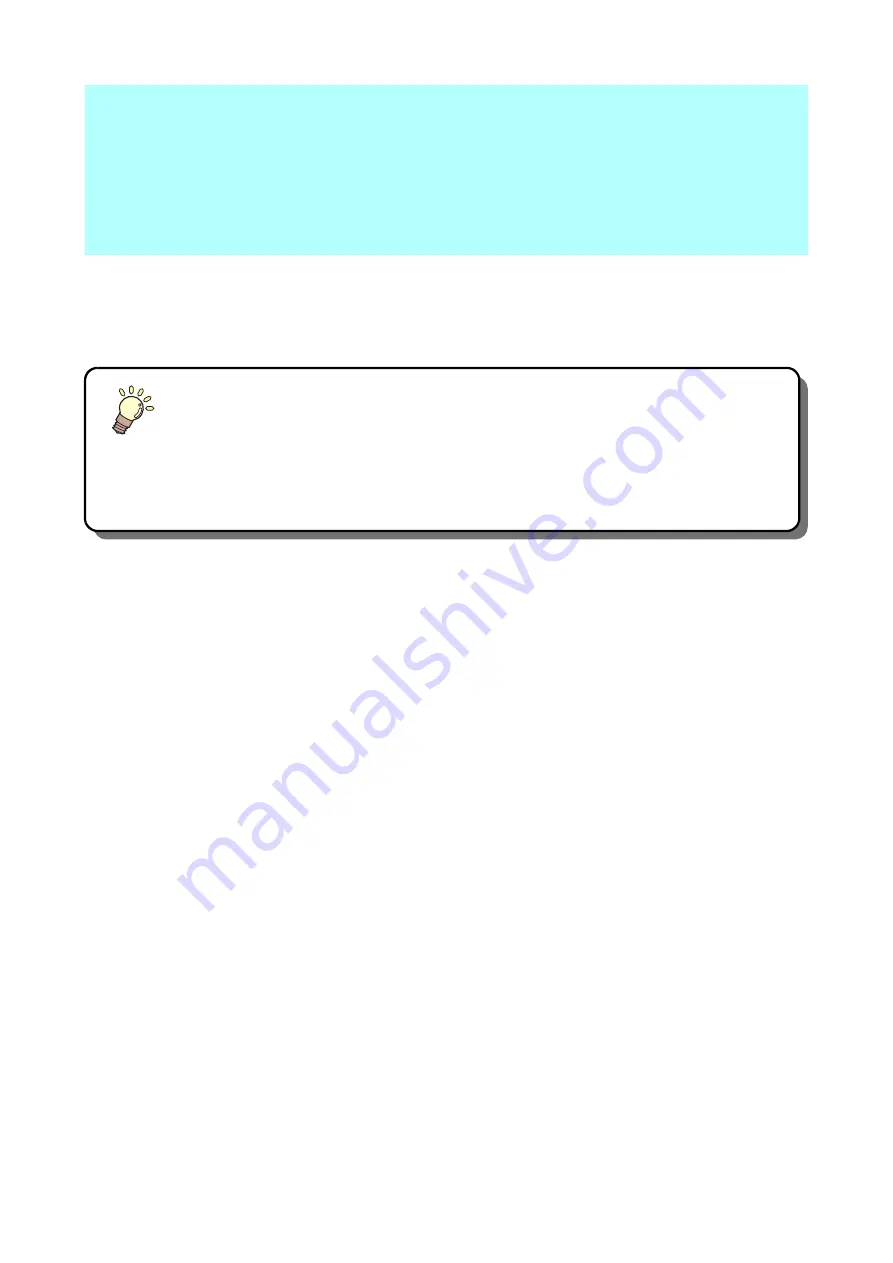
This Section....
... describes the basic operations, such as mounting tools and workpieces.
Basic Operation Workflow ...................... 2-2
Turning the Power ON............................ 2-3
Moving the Head .................................... 2-4
Moving the Head Using the Head Retraction
[VIEW] Function ....................................... 2-4
Moving the Head Using the Jog Keys ...... 2-5
Fixing the Workpiece .............................. 2-6
Fixing the Workpiece with Adhesive Tape 2-6
Fixing the Workpiece
by Vacuum Adhesion ...............................2-7
Method of fixing the sponge .....................2-9
Selecting Tools ..................................... 2-10
Select the tool condition .........................2-10
Set Items ................................................2-11
Adjusting the Blade to Match
the Workpiece....................................... 2-14
Adjusting the tial Cutter ..........................2-14
Adjusting the Swivel Blade .....................2-16
Making a Test Cut ................................ 2-17
Checking the Tool Status .......................2-18
Checking the Status Between Tools .......2-20
Setting the Drawing Origin.................... 2-23
Cutting (Drawing).................................. 2-24
Effective Cutting Area .............................2-24
Cutting (Drawing) ....................................2-24
Interrupting Processing ...........................2-25
Restarting Processing ............................2-25
Interrupting Processing (Data Clear) ......2-26
Turning the Power OFF ........................ 2-27
Chpater 2
Basic Operations
Summary of Contents for CFL-605RT
Page 7: ...vi ...
Page 14: ...xiii ...
Page 48: ...2 8 1 Put the workpiece on the cutting panel 2 Press ...
Page 68: ...2 28 ...
Page 138: ...4 22 ...
Page 168: ...6 24 ...
Page 169: ...D202786 14 30062016 ...