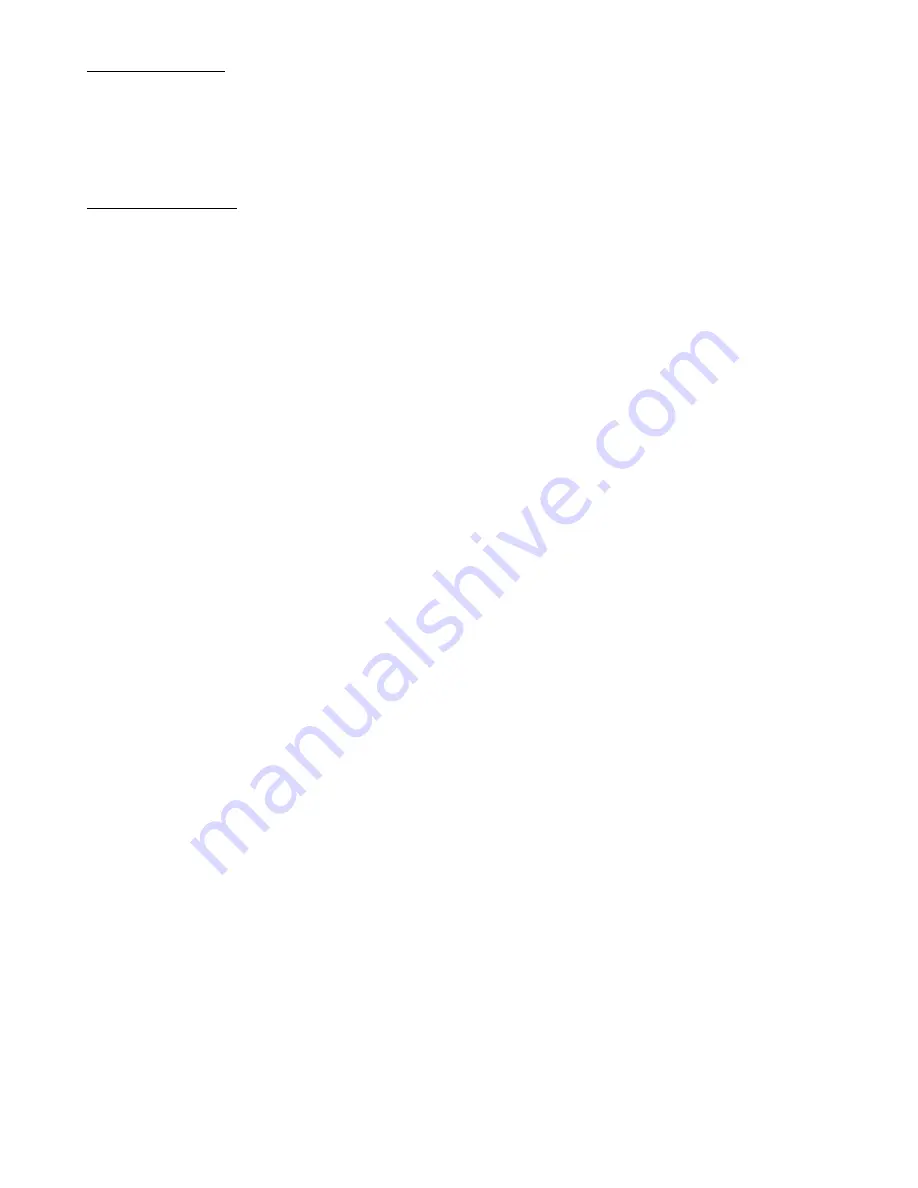
OM-172 324 Page 5
Pulse Panel Terms:
Card Mode
Is used to select use of the optional data card storage and retrieval capabilities.
Process Mode
Is used to select the type of process to be used, including Pulse, Adaptive
Pulse, or Mig.
Sequence Mode
Is used to select and program the weld sequences which include preflow, run-
in, weld, crater, burnback, and postflow.
Setup Screen Terms:
Access Code
NOTE: The optional Data Card is required to activate this feature. With code
off, access to the setup displays is not restricted. With code on, the operator
must know and enter the access code to access or change any of the setup
displays.
To use code, press Parameter Select button to enter access code. When the
correct letter is entered, the indicator automatically moves to the next charac-
ter. When the final access code letter is entered, the display automatically
changes to the initial setup display.
Arc Start
NOTE: Do not use the Hot Start setting for .035 in (9 mm) or smaller wire. Use
the Hot Start mode for pulse welding with 450 Ampere Inverter Model when
high initial weld current is necessary to start large diameter welding wires.
When in Hot Start, the 450 Ampere Inverter Model starts the arc in the CV
mode and switches to CC once the arc is started. Do not use Hot Start unless
using 450 Ampere Inverter Model
.
Arc Time
Allows actual arc time up to 9,999.99 hours and weld cycles up to 999,999 to
be accumulated and displayed on the digital display, and can be reset to zero
as required.
Mig Type (Voltage
Correction)
With DVC Voltage Correction On, the unit uses closed-loop feedback from the
17-pin cord or voltage sensing leads to maintain set voltage parameters. With
DVC Voltage Correction Off, feedback from the arc is not used for closed-loop
feedback to maintain voltage parameters. Feedback from the arc is still used
for other functions.
Be sure voltage sensing leads are connected or voltage feedback is available
through the 17-pin receptacle via the welding power source.
Name Feature
When using the optional Data Card and turning the name feature on, programs
written to the card can be identified by name, number, job number, etc.
Program Reset
By selecting program reset in the memory reset mode, the unit defaults to origi-
nal factory program settings for the program last active. All other program and
setup information remains the same.
Range
The interface requires that the voltage and amperage range of the welding
power source be entered. Obtain this information from the welding power
source Owner’s Manual.
Security
NOTE: The optional Data Card is required to activate this feature. Is used to
limit what the operator can control. This includes accessing the number of the
program, 1 through 8, and the range of welding parameters within the program.
Software Screen
Selection of this function will display the software version of the unit. When
talking with factory service personnel, this number may be required.
System Reset
By selecting system reset in the memory reset mode, the unit defaults to origi-
nal factory settings for all programs and all set up excluding System, Arc Time,
and Model Type.
Voltage (Control Feedback)
Allows voltage to be monitored at the output terminals by two methods. This
can be selected through the 17-pin cord connection if the welding power source
has a 17-pin receptacle, or through the unit’s external voltage sense lead.
If the 17 Pin setting is used, it is recommended that the voltage sensing termi-
nals on the welding power source be used to monitor arc voltage at the work-
piece.
When using the V. Sense setting, arc voltage feedback is through the voltage
sense leads connected to the feeder. Use this setting when there is more than
50 ft (15 m) of weld cable used.
Summary of Contents for Robotic Interface II
Page 2: ......
Page 57: ...OM 172 324 Page 51 SD 171 360 A...
Page 58: ...OM 172 324 Page 52 Figure 12 2 Circuit Diagram For Microprocessor Board PC1...
Page 59: ...OM 172 324 Page 53 SD 161 039 A...
Page 60: ...OM 172 324 Page 54 Figure 12 3 Circuit Diagram For Motor Board PC3...
Page 61: ...OM 172 324 Page 55 SD 083 388 B...
Page 62: ...OM 172 324 Page 56 Figure 12 4 Circuit Diagram For Customer Interface Board PC4...
Page 63: ...OM 172 324 Page 57 SD 166 275...
Page 64: ...OM 172 324 Page 58 Figure 12 5 Circuit Diagram For Interface Board PC5...
Page 65: ...OM 172 324 Page 59 SD 165 466...
Page 66: ...OM 172 324 Page 60 Figure 12 6 Circuit Diagram For Filter Board PC6 SB 159 412...
Page 67: ...OM 172 324 Page 61 Figure 12 7 Circuit Diagram For Display Board PC7 SC 165 462 A...
Page 69: ...OM 172 324 Page 63 NOTES...
Page 78: ......