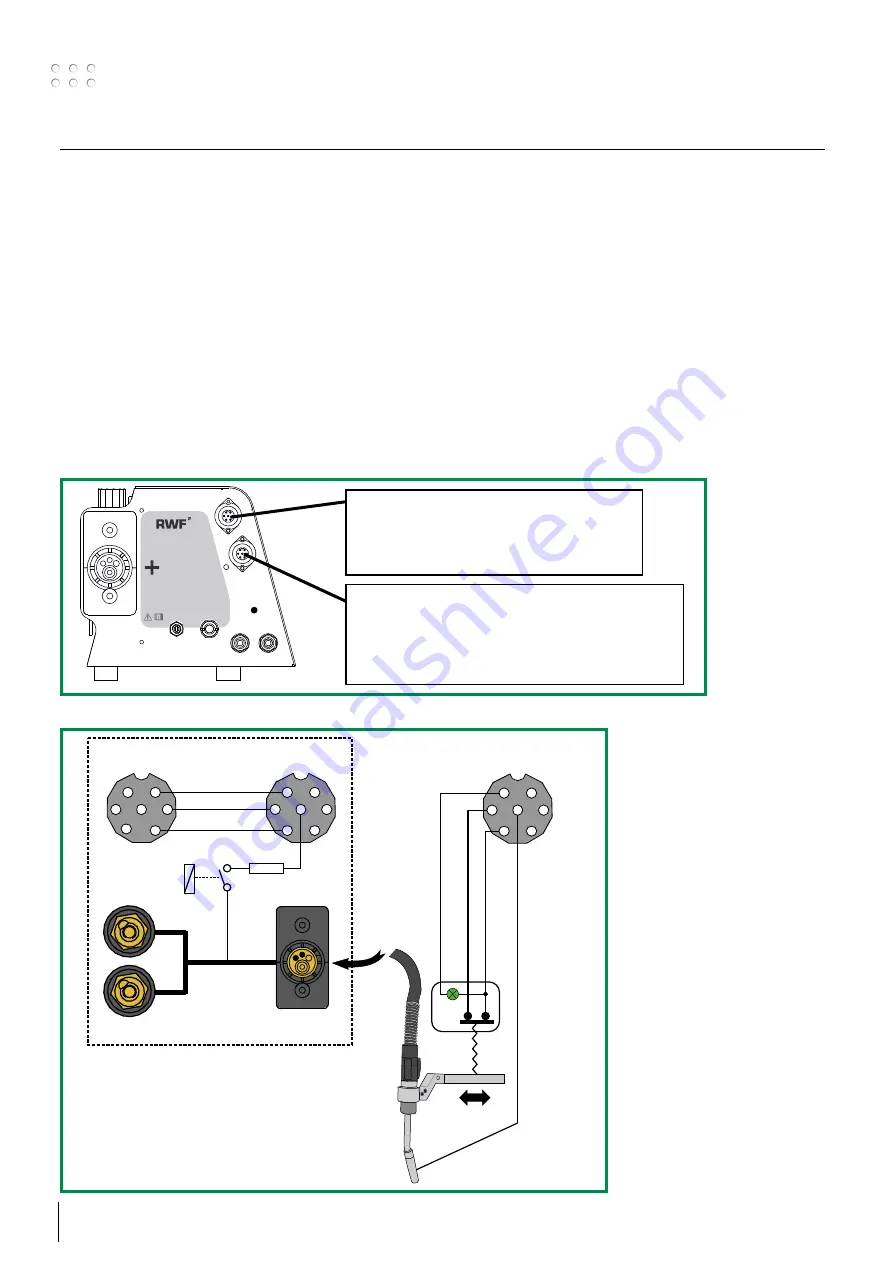
8
9
How to connect the installation
Touch sensing
For exact positioning of the welding torch, it is possible to use the Touch Sensing signal.
This option is available when using Fieldbus communication only.
When the welding wire has contact to the work piece, the robot/controller is told so by changing the
status of an output bit. Touch sensing can also be connected to the gas nozzle.
N.B. Gas nozzle sensing is automatically enabled through a relay when activating touch sensing. The relay
will, for safety reasons, disconnect the gas nozzle sense signal during welding.
Activate Touch sensing by enabling the Touch sensing input bit.
E.x. For Sigma Galaxy this is input Bit # 123. See Fieldbus configuration file for more details.
Read the Touch sensing status output bit.
When the welding wire (or optional the gas nozzle) has contact to work piece, while not welding:
E.x. For Sigma Galaxy output Bit # 147 is ON when there is contact, and OFF when no contact.
See Fieldbus configuration file for more details.
AIR Clean
Max.8 bar
Collision protection signal to robot controller
Pin 1: 0V from robot controller
Pin 2: +24V from robot controller
Pin 3: Collision signal to robot controller
Collision protection signal and touch sense to torch
Pin 1: 0V to collision sensor
Pin 2: +24V to collision sensor
Pin 3: Collision signal from collision sensor
Pin 7: Touch sense connection to gas nozzle
Male
1
2
3
Female
1
2
3
7
To robot controller
To collision sensor &
touch sensor
Collision signal
24V
0V
1K
50W
Ω
Torch gas
nozzle sense
relay
ZA
W
from power source
Male
1
2
3
7
To RWF² collision
sensor & touch sensor
Collision
sensor
Torch gas
nozzle sense
signal
RWF
2