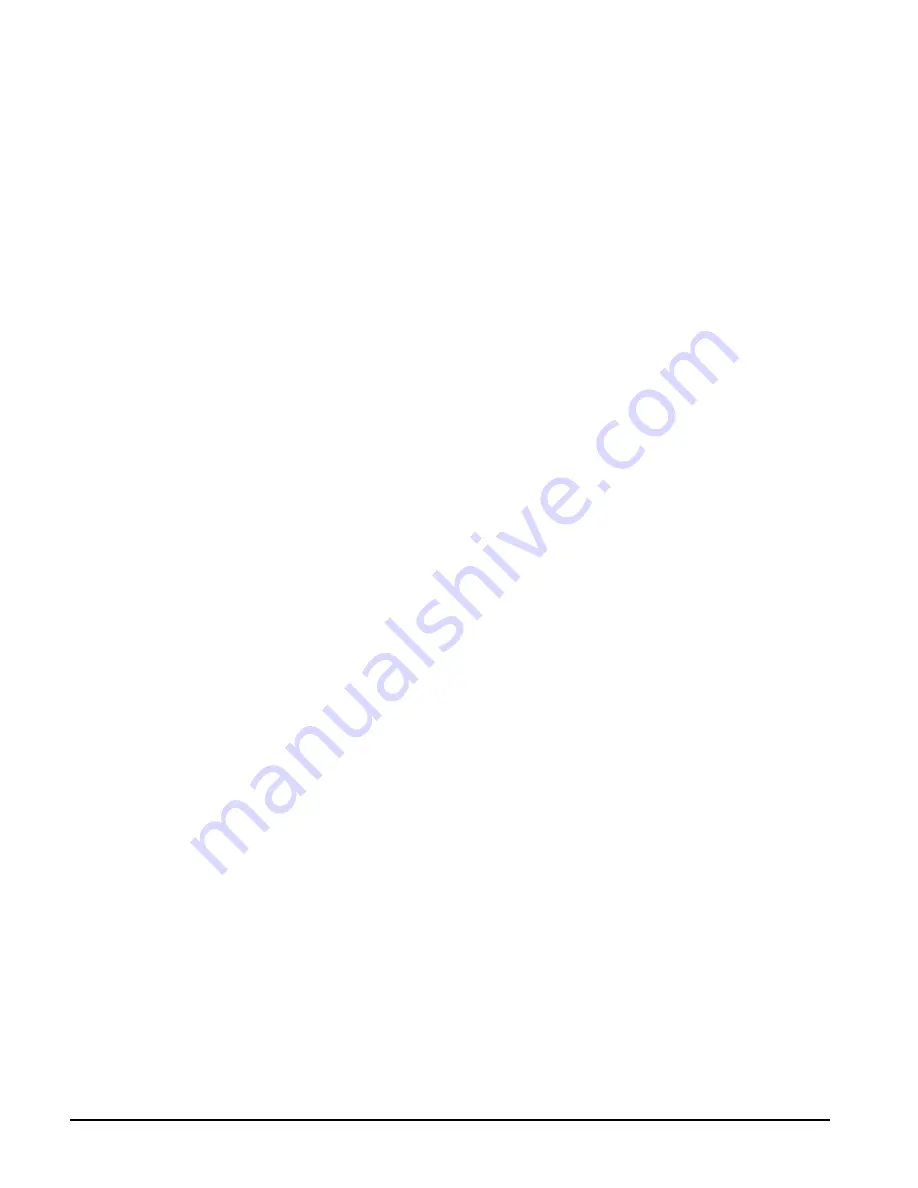
2
IOMM ACZ/AGZ-1
Table of Contents
Introduction .........................................3
Inspection ...........................................................3
Installation...........................................4
Handling..............................................................4
Location...............................................................5
Service Access ...................................................5
Vibration Isolators..............................................7
Water Piping .......................................................8
Flow Switch.........................................................9
Glycol Solutions...............................................10
Evaporator Flow and Pressure Drop.............12
Refrigerant Piping ............................................13
Physical Data.....................................18
Electrical Data...................................21
Field Wiring.......................................................21
Electrical Data AGZ-AM.................................22
Electrical Data ACZ..........................................22
Electrical Notes.................................................23
Wiring Diagrams ...............................................25
Dimensional Data..............................36
Startup ...............................................38
Pre Start-up .......................................................38
Start-Up .............................................................38
Shutdown ..........................................................38
Water Piping Checkout ...................................39
Refrigerant Piping Checkout ..........................39
Refrigerant Charging .......................................40
Electrical Check Out.........................................41
Operation...........................................42
Sequence of Operation....................................42
Hot Gas Bypass (Optional).............................43
Filter Driers........................................................44
System Adjustment..........................................44
Liquid Sightglass and Moisture Indicator ...44
Thermostatic Expansion Valve.......................44
Crankcase Heaters ...........................................45
Water Cooler.....................................................45
Global UNT Controller, AGZ-AM ....46
General Description .........................................46
Optional Sensors..............................................46
Controller Inputs /Outputs .............................48
Additional UNT Features ...............................51
Alarms ................................................................53
ZONE TERMINAL (optional) ........................54
Zone Terminal Glossary ..................................58
Global UNT Controller Troubleshooting
Chart...................................................................60
MicroTech Controller, AGZ-AM ......62
General Description .........................................62
Optional Sensor Packages ..............................62
Installation ........................................................62
Sequence of Operation....................................71
Start-Up and Shutdown ..................................73
Keypad / Display .............................................74
Menu Descriptions ..........................................77
Trouble Analysis for the AGZ MicroTech
Controller...........................................................87
Test Procedures................................................91
Unit Maintenance..............................98
Preventative Maintenance Schedule ............99
Service .............................................100
Liquid Line Solenoid Valve...........................100
Evaporator.......................................................101
Refrigerant Charging .....................................101
Troubleshooting Chart..................................103
Our facility is
ISO9002 Certified
"McQuay" is a registered trademark of McQuay International
1997 McQuay International
"Information represents McQuay International products at the time of publication and we reserve the right to
make changes in design and construction at anytime without notice"
Summary of Contents for ACZ 045A
Page 6: ...6 IOMM ACZ AGZ 1 Figure 3 Clearance Requirements...
Page 27: ...IOMM ACZ AGZ 1 27 Figure 12 AGZ AM Single point Connection with FanTrol...
Page 28: ...28 IOMM ACZ AGZ 1 Figure 13 AGZ AM Single point Connection with SpeedTrol...
Page 29: ...IOMM ACZ AGZ 1 29 Figure 14 AGZ AM Unit Control Schematic UNT...
Page 30: ...30 IOMM ACZ AGZ 1 Figure 15 AGZ AM Staging Schematic UNT...
Page 31: ...IOMM ACZ AGZ 1 31 Figure 16 AGZ AM MicroTech Controller Schematic...
Page 32: ...32 IOMM ACZ AGZ 1 Figure 17 AGZ AM Unit Control Schematic MicroTech...
Page 33: ...IOMM ACZ AGZ 1 33 Figure 18 AGZ AM Staging Schematic MicroTech...
Page 34: ...34 IOMM ACZ AGZ 1 Figure 19 ACZ Field Connection Diagram No Capacity Control...
Page 35: ...IOMM ACZ AGZ 1 35 Figure 20 ACZ Field Wiring Diagram Capacity Control Staging...
Page 104: ...Post Office Box 2510 Staunton Virginia 24402 2510 USA 800 432 1342 www mcquay com...