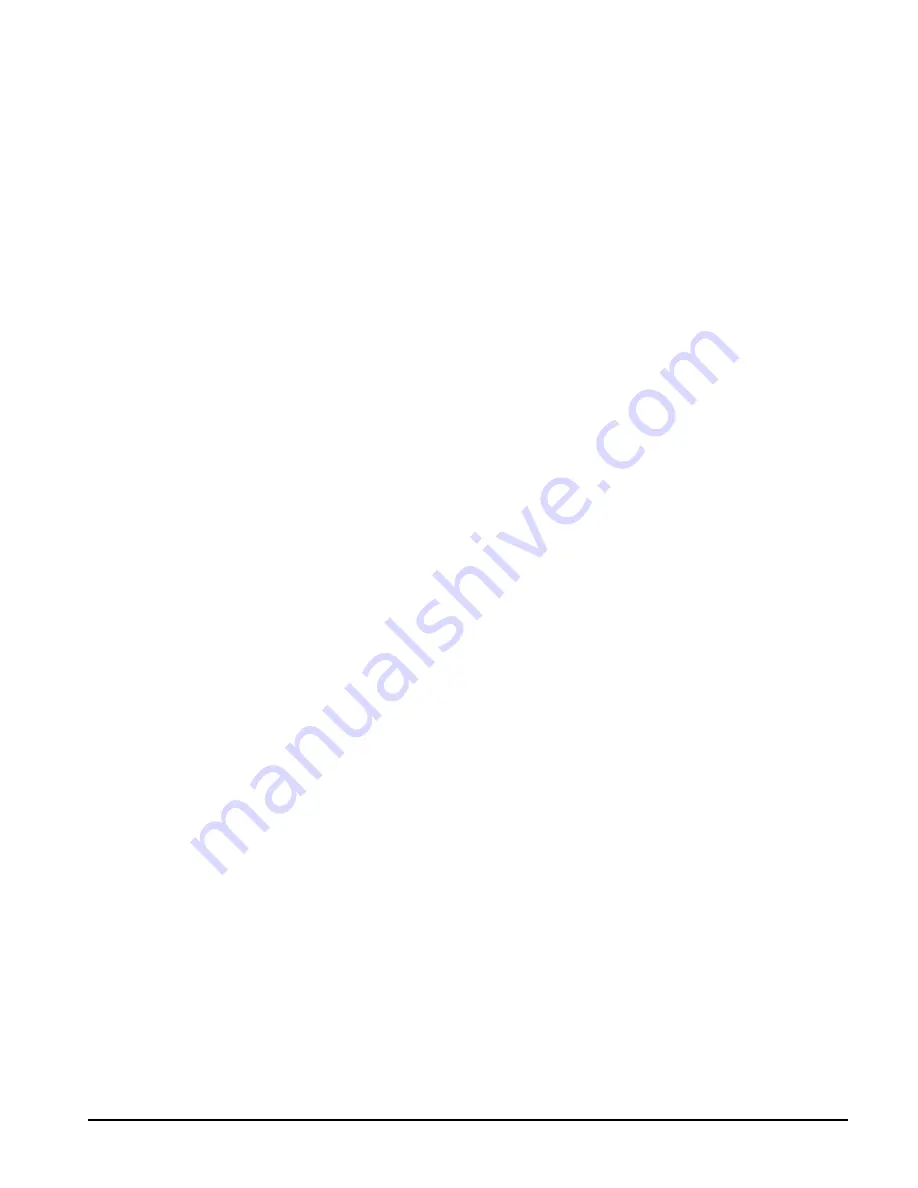
IOMM ACZ/AGZ-1
13
Refrigerant Piping
Introduction
Proper refrigerant piping can represent the difference between a reliable, trouble free system and
months or years of inefficient, problematic performance.
System concerns related to piping are:
1.
Refrigerant pressure drop
2.
Solid liquid feed to the expansion valve(s)
3.
Continuous oil return
The most important and least understood is number 3. “Continuous oil return”. The failure of oil to
return at or close to the rate of displacement from the compressor can result in oil trapping and
ultimate compressor failure.
On the other hand, the instantaneous return of a large volume of compressor oil (slug) can be equally
damaging to a compressor.
All compressors displace some oil during operation. Reciprocating compressors displace more than
centrifugals, scroll and McQuay screw compressors. Oil is carried into compressor cylinders with
suction gas; and that same gas entrains oil present on cylinder walls as it is being compressed. The
sum of the two is then pumped into the discharge piping.
More oil is displaced at compressor start-up than during the normal running periods. If a compressor
experiences excessive starts because of recycling pumpdown control, the oil may be pumped out and
trapped in the condenser with the refrigerant charge. This oil may not return regardless of the
adequacy of the piping system.
A similar problem to a lesser extent occurs when the equipment is oversized for the available cooling
load.
In short, extreme care should be exercised to assure that both piping and controls are suitable for the
application such that displaced oil is returned to the compressor moderately. Note that oil loss to the
system can be due to a hang up in the evaporator, as well as in the piping.
Suction Lines
McQuay recommends the use of ASHRAE for guidelines in sizing and routing piping with one
exception. See the 1998 ASHRAE Handbook Refrigeration Edition, Chapter 2 for tables and
guidelines. The single exception is to the piping of direct expansion cooling coils located above the
compressors. In all cases, regardless of whether the equipment has pumpdown control or not, a trap
in the suction line equal to the height of the coil section is recommended. In its absence, upon a
power failure, all of the liquid in the coil will fall by gravity to the compressor below.
Suction line gas velocities may range between 900 and 4000 feet per minute. Consideration should be
given to the possibility of objectionable noise in or adjacent to occupied space. Where this is a
concern, gas velocities on the low side are recommended.
Routing must also take into account the requirement established in the latest ANSI/ASHRAE 15.
To size the suction line, determine:
a.
The maximum tons for the circuit
b.
The actual length in feet
c.
The equivalent length contributed by elbows, fittings, valves or other refrigerant specialties.
ASHRAE Tables 2-10, 11 & 12
Summary of Contents for ACZ 045A
Page 6: ...6 IOMM ACZ AGZ 1 Figure 3 Clearance Requirements...
Page 27: ...IOMM ACZ AGZ 1 27 Figure 12 AGZ AM Single point Connection with FanTrol...
Page 28: ...28 IOMM ACZ AGZ 1 Figure 13 AGZ AM Single point Connection with SpeedTrol...
Page 29: ...IOMM ACZ AGZ 1 29 Figure 14 AGZ AM Unit Control Schematic UNT...
Page 30: ...30 IOMM ACZ AGZ 1 Figure 15 AGZ AM Staging Schematic UNT...
Page 31: ...IOMM ACZ AGZ 1 31 Figure 16 AGZ AM MicroTech Controller Schematic...
Page 32: ...32 IOMM ACZ AGZ 1 Figure 17 AGZ AM Unit Control Schematic MicroTech...
Page 33: ...IOMM ACZ AGZ 1 33 Figure 18 AGZ AM Staging Schematic MicroTech...
Page 34: ...34 IOMM ACZ AGZ 1 Figure 19 ACZ Field Connection Diagram No Capacity Control...
Page 35: ...IOMM ACZ AGZ 1 35 Figure 20 ACZ Field Wiring Diagram Capacity Control Staging...
Page 104: ...Post Office Box 2510 Staunton Virginia 24402 2510 USA 800 432 1342 www mcquay com...