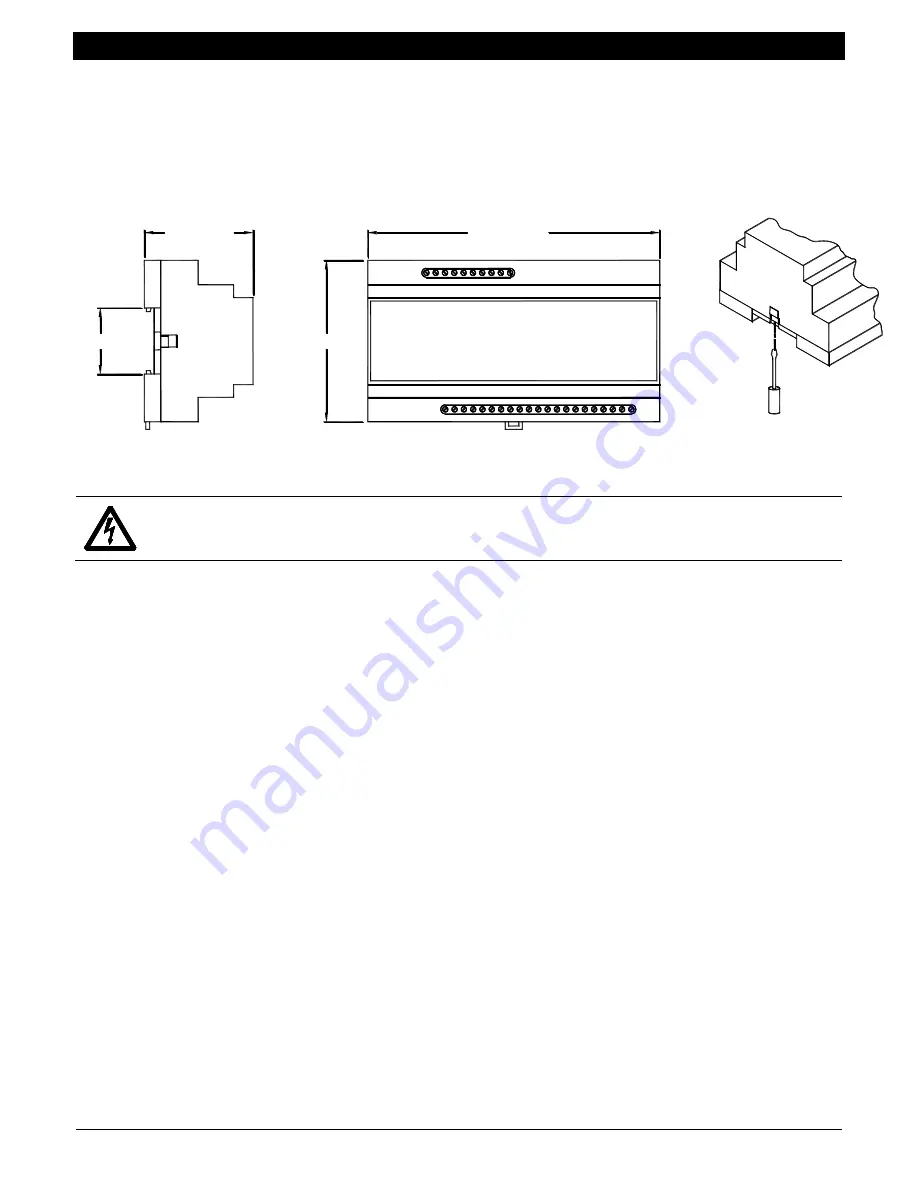
2.0
INSTALLATION
www.maxcessintl.com
MAGPOWR Spyder-Plus
MI 850A320 1 M
Page 8 of 60
The Spyder is intended for installation on a vertical or horizontal panel with a DIN35 rail. See Figure 2 for
dimensions. The Spyder provides an IP-20 environmental degree of protection.
Wiring to and from the enclosure must be done with double or reinforced insulation or protective screening which
provides protective separation. All wiring outside of the Spyder should comply with the essential requirements of
the appropriate local standard(s) and is the responsibility of the installer.
Figure 2
Outline Dimensions
Figure 3
Enclosure Top Removal
WARNING: DISCONNECT POWER BEFORE OPENING ENCLOSURE
58.4 [2.30]
35.2 [1.39]
85.8 [3.38]
157 [6.18]