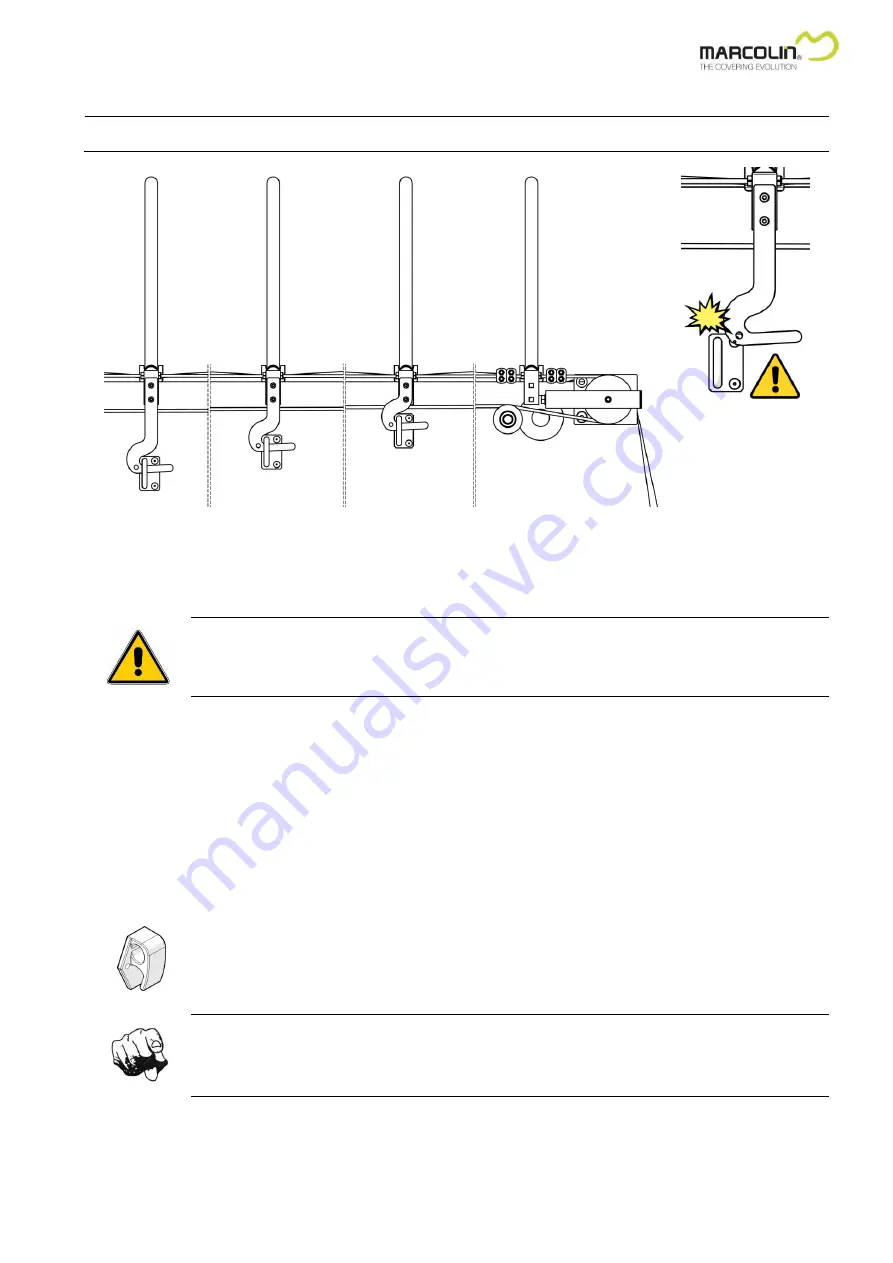
Installation manual - Eletta
®
- 29
•
Proceed installing the remaining safety hooks as shown in the figure below:
Note:
Before fastening the respective hooking, verify that while folding the tarpaulin the safety hook is fastened on a
different level than the foregoing one, in order not to interfere with the foregoing fastened hooking.
•
If obstacles interefere with the hookings, shift the hook upwards on the upper hole and repeat the above described
fastening operations.
•
In the absence of any obstacles while moving the tarpaulin, fasten the U-clamp of the respective hook.
•
Proceed with fastening the subsequent hooks.
WARNING!
We recommend taking care of each U-clamp terminal positioning in order to avoid operating troubles
while handling the covering system.
3.9.2 Hermetic closure with elastic strings
With this lateral closure system, the tarpaulin comes down a few centimetres from the upper edge of the tipper body and
then it is tightened by appropriate elastic strings with hooks.
The tarpaulin borders are equipped with fastening ropes with elastic strings, with plastic or iron hooks.
For fastening the hooks proceed as follows:
•
Move out the tarpaulin and cover entirely the tipper body.
•
Fasten the specific hooks using the supplied rivets on the hooking points in the bottom part of the tipper body.
•
Make sure that the fixing height of the hooks permits a proper tightening of the elastic strings.
INSTRUCTION!
During the training course REPEAT often to the operator that HE HAS NOT TO MOVE THE VEHICLE
while the elastic strings are still loose.