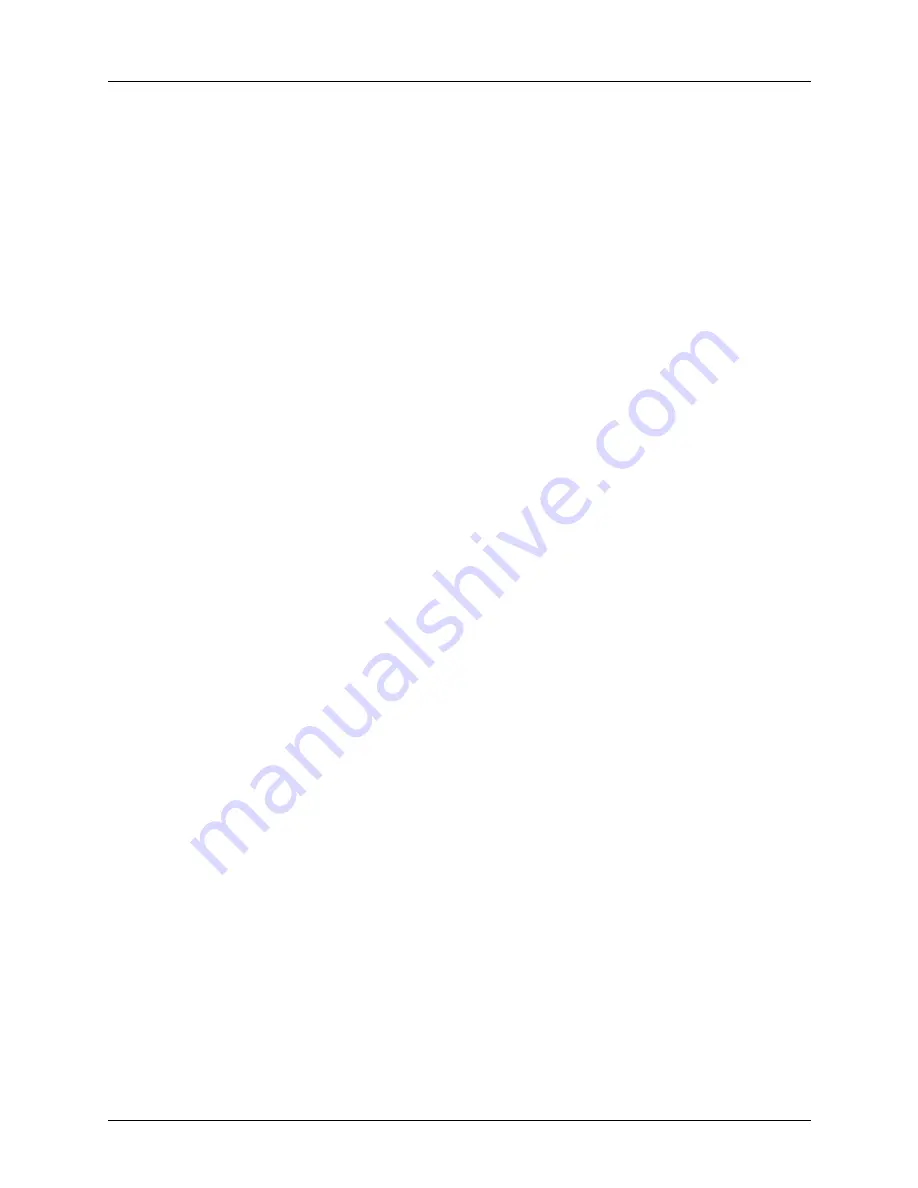
OPERATION SUMMARY - Section 3
MTS-3000 SERIES OPERATION AND REFERENCE MANUAL 3-19
CU M004 01A
###################################
0$17$
#
7(67
#
6<67(06
3.3.8.1 SETUP.
To test a single phase overcurrent relay, connect the test leads, as shown by the solid lines. A three-phase
relay or three single-phase devices on a relay panel require the additional connections shown as dashed
lines.
If the relay requires auxiliary DC power, connect it as shown by the dotted lines. If there are more than a
single set of contacts provided (e.g. separate timed and instantaneous contacts), it will be necessary to
move the contact operation sensing leads to the appropriate terminals for the separate element tests. If three
current modules are not fitted, it will be necessary to move the Ia output to the other phases in turn to verify
them.
The system should be in Vector fault mode, as shown in the fourth line of the CM display above. If it isn’t,
enter the following key sequence: MENU | Settings | Fault Type | Vector, and then press MENU again.
3.3.8.2 MINIMUM PICKUP TEST
.
1.
Disable the outputs, if necessary, by pressing ENABLE until its LED is out, and press FAULT. Its
LED should come on.
2.
Select the A phase of the current output module by pressing the F1 key on the module. Its LED will
come on and a cursor will flash slowly beneath the ‘A’ representing Amps in the F1 line of the
module’s display.
3.
Enter (via the MODIFY keyboard or rotary knob), a current value that’s somewhat less than the
expected minimum pickup level of the relay under test.
4.
Enable the outputs by pressing ENABLE. Press and hold FAULT, and rotate the MODIFY knob
clockwise until the relay begins to operate. The LED indicator on INPUT 1 of the DIGITAL I/O
module will light, and the audible tone, if enabled via the tone switch, will sound. The current may be
adjusted up or down via the MODIFY knob to verify the pickup level.
5.
Release the FAULT button when the test is complete.
TIP:
INPUT 2 on the DIGITAL I/O module can be configured as an external start input to work with a
foot switch, relieving the operator of the need to continuously press the FAULT pushbutton. See
the Advanced Operation section for information on configuring the input. Any commercial
normally open foot switch will work. A heavy duty one is available from Manta Test Systems.
3.3.8.3 INVERSE-TIME CHARACTERISTIC TEST.
If the expected current required for this test is higher than can be achieved from a single current output
channel, it will be necessary to parallel two or three channels to get the desired current. Use the heaviest
gage leads possible to minimize voltage drop in the leads. If the output channels are paralleled at the load
instead of at the output terminals, remember that the neutral lead will be carrying two or three times the
current of the individual phase leads. Ensure that the amplitudes and phase angles of each channel are
adjusted correctly (as described in previous item 3.3.7), or use the automated paralleling feature available
through the Control Module’s menu.