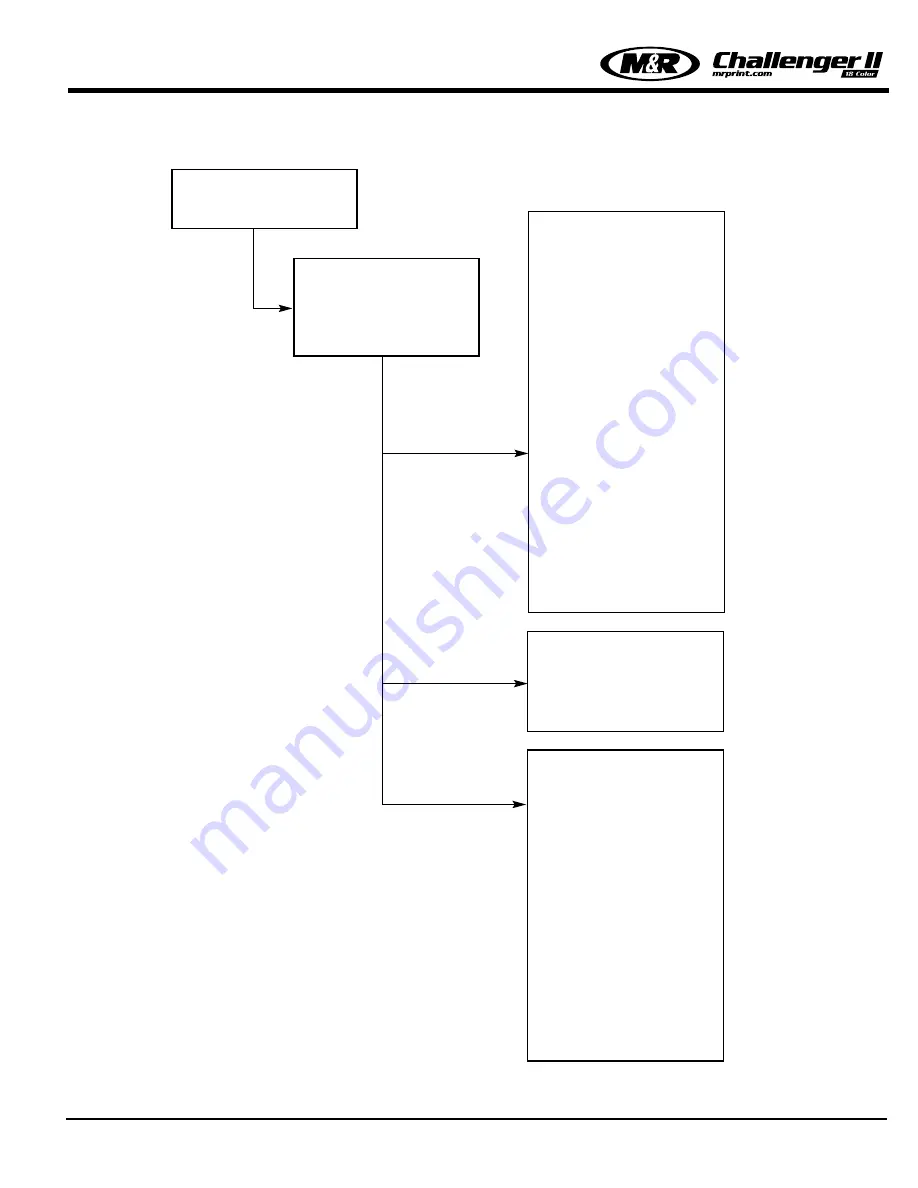
E 300 Operator Interface Logic Diagram
M&R Printing Equipment, Inc. - Glen Ellyn, Illinois
61
MAIN MENU SCREEN
PLC Identity No.
Program Version No.
MTA No.
SERVO DRIVE TEST
Regenerative load ratio:
0%
Effective load ratio:
0%
Peak load ratio:
0%
Motor Rotational Speed: 0.0 rpm
Actual Present:
0 pls
Feed Present:
0 pls
Deviation Counter:
0 pls
Motor Current:
0 R
Ready:
OFF
Servo On:
OFF
Zero Point Pass:
OFF
At In-Positon:
OFF
Zero Speed:
OFF
Torque Limit:
OFF
Servo Alarm:
OFF
Servo Warning:
OFF
Automatic Tuning:
0
Load Inertia Ratio:
0
Position Control Gain1
0
Speed Control Gain1:
0
Position Control Gain2:
0
Speed Control Gain2:
0
Speed Incremental Comp:
0
Servo Amp S/W Number:
Parameter Error 0-15:
0000
Parameter Error 16-31:
0000
Parameter Error 32-47:
0000
Servo Status:
0000
HARDWARE TEST
>Panel Test
>Proximities Test
>Motion Card Test
>Servo Drive Test
>Servo/Motion Card History
>Other Tests
SERVO MOTION CARD HISTORY
1:0000-NONE
2:0000-NONE
3:0000-NONE
4:0000-NONE
5:0000-NONE
6:0000-NONE
OTHER TESTS
Heads Print Pushbuttons 1
OFF
Heads Print Pushbuttons 2
OFF
Heads Print Pushbuttons 3
OFF
Heads Print Pushbuttons 4
OFF
Heads Print Pushbuttons 5
OFF
Heads Print Pushbuttons 6
OFF
Heads Print Pushbuttons 7
OFF
Heads Print Pushbuttons 8
OFF
Heads Print Pushbuttons 9
OFF
Heads Print Pushbuttons 10
OFF
Heads Print Pushbuttons 11
OFF
Heads Print Pushbuttons 12
OFF
Heads Print Pushbuttons 13
OFF
Heads Print Pushbuttons 14
OFF
Heads Print Pushbuttons 15
OFF
Heads Print Pushbuttons 16
OFF
Heads Print Pushbuttons 17
OFF
Heads Print Pushbuttons 18
OFF
Yellow Cords:
OFF
No T-Shirt Sensor:
OFF
Foot Pedal:
OFF
Air Pressure Switch:
OFF
PLC ERROR:
0
Summary of Contents for 12 COLOR
Page 4: ......
Page 6: ......
Page 8: ......
Page 18: ...M R Printing Equipment Inc Glen Ellyn Illinois 10 Specifications NOTES...
Page 38: ...Quartz Flash Operation M R Printing Equipment Inc Glen Ellyn Illinois NOTES 30...
Page 72: ...081200MS PREVENTIVE MAINTENANCE PROCEDURE CHALLENGER Series II NOTES 64...
Page 84: ...PREVENTIVE MAINTENANCE PROCEDURE CHALLENGER Series II NOTES 081200MS 76...
Page 88: ...081200MS PREVENTIVE MAINTENANCE PROCEDURE CHALLENGER Series II NOTES 80...
Page 104: ...PREVENTIVE MAINTENANCE PROCEDURE CHALLENGER Series II NOTES 96...
Page 112: ...PREVENTIVE MAINTENANCE PROCEDURE CHALLENGER Series II NOTES 104...
Page 114: ...081200MS PREVENTIVE MAINTENANCE PROCEDURE CHALLENGER Series II NOTES 106...
Page 116: ...PREVENTIVE MAINTENANCE PROCEDURE CHALLENGER Series II NOTES 108...
Page 118: ...081200MS 110 This page left blank intentionally...
Page 122: ...Leveling the Pallets M R Printing Equipment Inc Glen Ellyn Illinois 114 NOTES...
Page 128: ...Idec Relay Identification NOTES 120...
Page 144: ...Trouble Shooting Procedure NOTES 136...
Page 153: ......
Page 154: ......
Page 156: ......
Page 160: ......
Page 162: ......
Page 164: ......
Page 166: ......
Page 168: ......
Page 172: ......
Page 174: ......
Page 176: ......
Page 178: ......
Page 180: ......
Page 182: ......
Page 184: ......
Page 186: ......
Page 188: ......
Page 190: ......
Page 192: ......
Page 194: ......
Page 196: ......
Page 198: ......
Page 200: ......
Page 202: ......
Page 204: ......
Page 206: ......
Page 208: ......
Page 210: ......
Page 212: ......
Page 214: ......
Page 216: ......
Page 218: ......
Page 220: ......
Page 222: ......
Page 224: ......
Page 228: ......
Page 230: ......
Page 232: ......
Page 234: ......
Page 240: ......