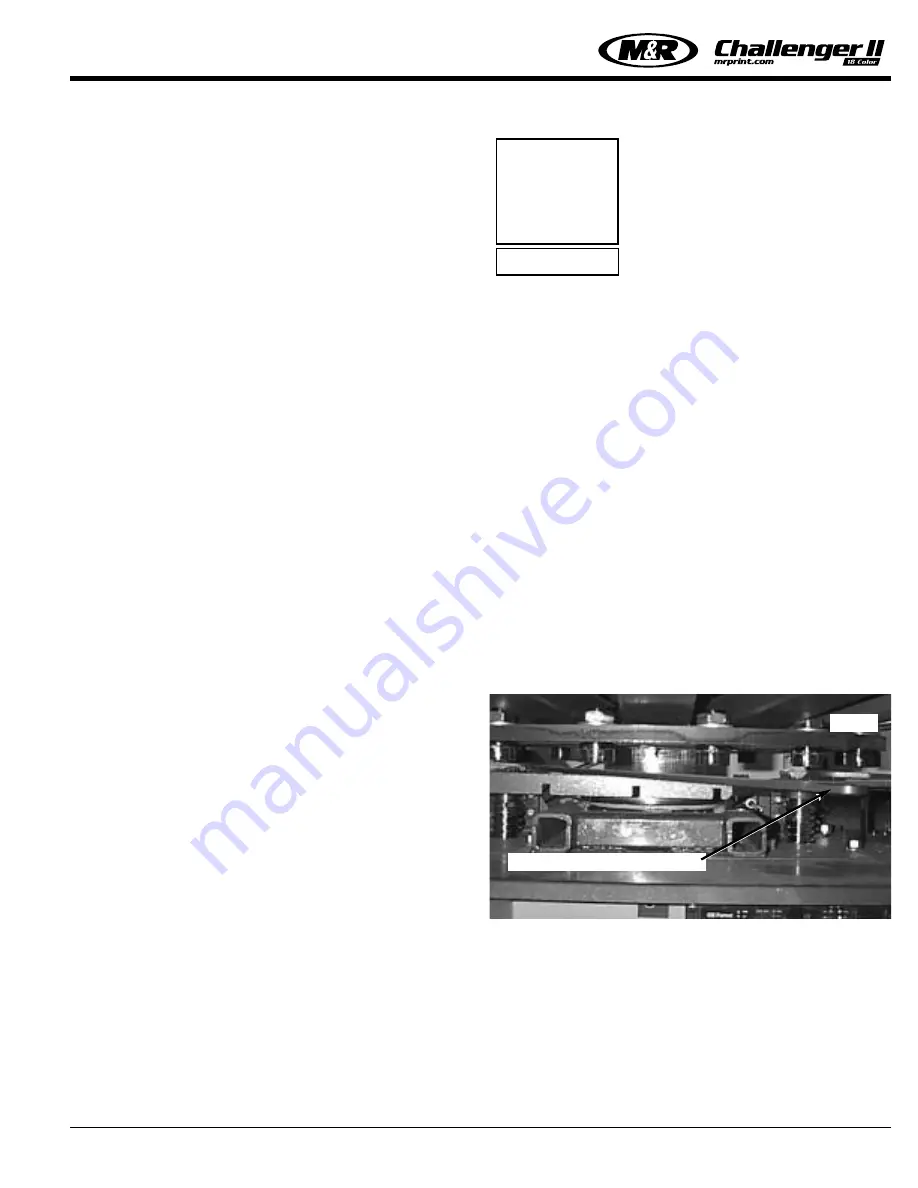
21
General Setup & Registration
1. Before installing screens into the print stations, check the
recommended print order, consider the mesh count, type of
ink, and area (image size) of ink deposit. This is the best
time to eliminate problems, such as ink build-up and butt-
to-butt registration blurring due to mesh count or ink type,
or improper screen tension. Experience is always the best
teacher for pre-press trouble shooting. It is always better to
eliminate problems before you start to print.
2. Once you determine print order, install all your screens in
their print stations and zero out the micros. Locate and align
the “trap” screen or screen that has the main image to
which all other colors register. When setting this screen, be
sure to leave 3/8" (9mm) to l/2" (12mm) between the inside
of the front screen holder and the frame. Leaving this gap
will help you later as you align the rest of your screens
because not all the screens are going to be in the exact
location as the first one. This gap should give you enough
room to align “mis-exposed” screens without running out of
room in the frame holders.
3. Install the flood bar, squeegee and add ink in your “trap”
screen, making sure that all adjustments are secure, then
print it on a Pelon. Be sure you have the proper ink deposit
and squeegee pressure before you register the rest of your
screens to this image.
4. Rotate the index table and pallet with the image around,
printed in step No. 3, to the remaining screens and register
them visually. You may find that registering your screen
slightly above the trap print will help, due to mesh
elongation during the print stroke. When locking down a
registered screen, do not tighten down the rear hand knob
because you are going to need to release the rear clamps
later when doing any micro-registration unless you have the
optional rear micro.
5. Install all squeegees and flood bars. Place a small
amount of ink in the screen to start with. This way, if the
color is incorrect, clean-up won’t be much of a problem.
6. Walk around the press and print one screen at a time.
Check the print for proper ink deposit, adjust print speed,
squeegee angle and pressure accordingly.
7. Once you have your desired ink deposit on all screens,
start to fine tune your registration. Remember to use the
same pallet and plenty of spray tack (adhesive) when
making test prints for registration.
NOTE: When using the micro-
registration, you must have the rear
screen frame clamps released to
allow the screen frame to move
freely and to avoid side loading of the
screen frame.
8. When using the micro register adjustments, be sure to
back the adjustment knob off after you lock down the Kipp
Elisa handles. This will take any side load or torque off of the
adjuster so the next time you release the Kipp Elisa handle,
the screen won’t shift.
9. Once you have a good print and it’s been approved, go
back and add ink to your screens.
10. When finished with the job, and during tear down,
always clean the press and make sure to keep the carriage
shafts clear of ink or pallet adhesive and well lubricated.
CENTRAL OFF-CONTACT LEVER:
The Central Off-Contact Lever provides a single point
adjustment that allows the press Operator to change the
off-contact dimension of all the screens with a simple
adjustment of a lever. This eliminates the need to
individually adjust off-contact for screens when printing
different thickness garments. i.e. (T-shirts to sweat-shirts).
(See Fig. 1)
This convenient control lever allows the press Operator to
adjust the off-contact setting for the press from a maximum
of 3/16" (5mm) to the minimum setting. The adjustment is
calibrated in three settings at 1/16" (1.5mm) increments.
M&R Printing Equipment, Inc. - Glen Ellyn, Illinois
i
IMPORTANT!
Fig. 1
Central Off-Contact Adj. Lever
Summary of Contents for 12 COLOR
Page 4: ......
Page 6: ......
Page 8: ......
Page 18: ...M R Printing Equipment Inc Glen Ellyn Illinois 10 Specifications NOTES...
Page 38: ...Quartz Flash Operation M R Printing Equipment Inc Glen Ellyn Illinois NOTES 30...
Page 72: ...081200MS PREVENTIVE MAINTENANCE PROCEDURE CHALLENGER Series II NOTES 64...
Page 84: ...PREVENTIVE MAINTENANCE PROCEDURE CHALLENGER Series II NOTES 081200MS 76...
Page 88: ...081200MS PREVENTIVE MAINTENANCE PROCEDURE CHALLENGER Series II NOTES 80...
Page 104: ...PREVENTIVE MAINTENANCE PROCEDURE CHALLENGER Series II NOTES 96...
Page 112: ...PREVENTIVE MAINTENANCE PROCEDURE CHALLENGER Series II NOTES 104...
Page 114: ...081200MS PREVENTIVE MAINTENANCE PROCEDURE CHALLENGER Series II NOTES 106...
Page 116: ...PREVENTIVE MAINTENANCE PROCEDURE CHALLENGER Series II NOTES 108...
Page 118: ...081200MS 110 This page left blank intentionally...
Page 122: ...Leveling the Pallets M R Printing Equipment Inc Glen Ellyn Illinois 114 NOTES...
Page 128: ...Idec Relay Identification NOTES 120...
Page 144: ...Trouble Shooting Procedure NOTES 136...
Page 153: ......
Page 154: ......
Page 156: ......
Page 160: ......
Page 162: ......
Page 164: ......
Page 166: ......
Page 168: ......
Page 172: ......
Page 174: ......
Page 176: ......
Page 178: ......
Page 180: ......
Page 182: ......
Page 184: ......
Page 186: ......
Page 188: ......
Page 190: ......
Page 192: ......
Page 194: ......
Page 196: ......
Page 198: ......
Page 200: ......
Page 202: ......
Page 204: ......
Page 206: ......
Page 208: ......
Page 210: ......
Page 212: ......
Page 214: ......
Page 216: ......
Page 218: ......
Page 220: ......
Page 222: ......
Page 224: ......
Page 228: ......
Page 230: ......
Page 232: ......
Page 234: ......
Page 240: ......