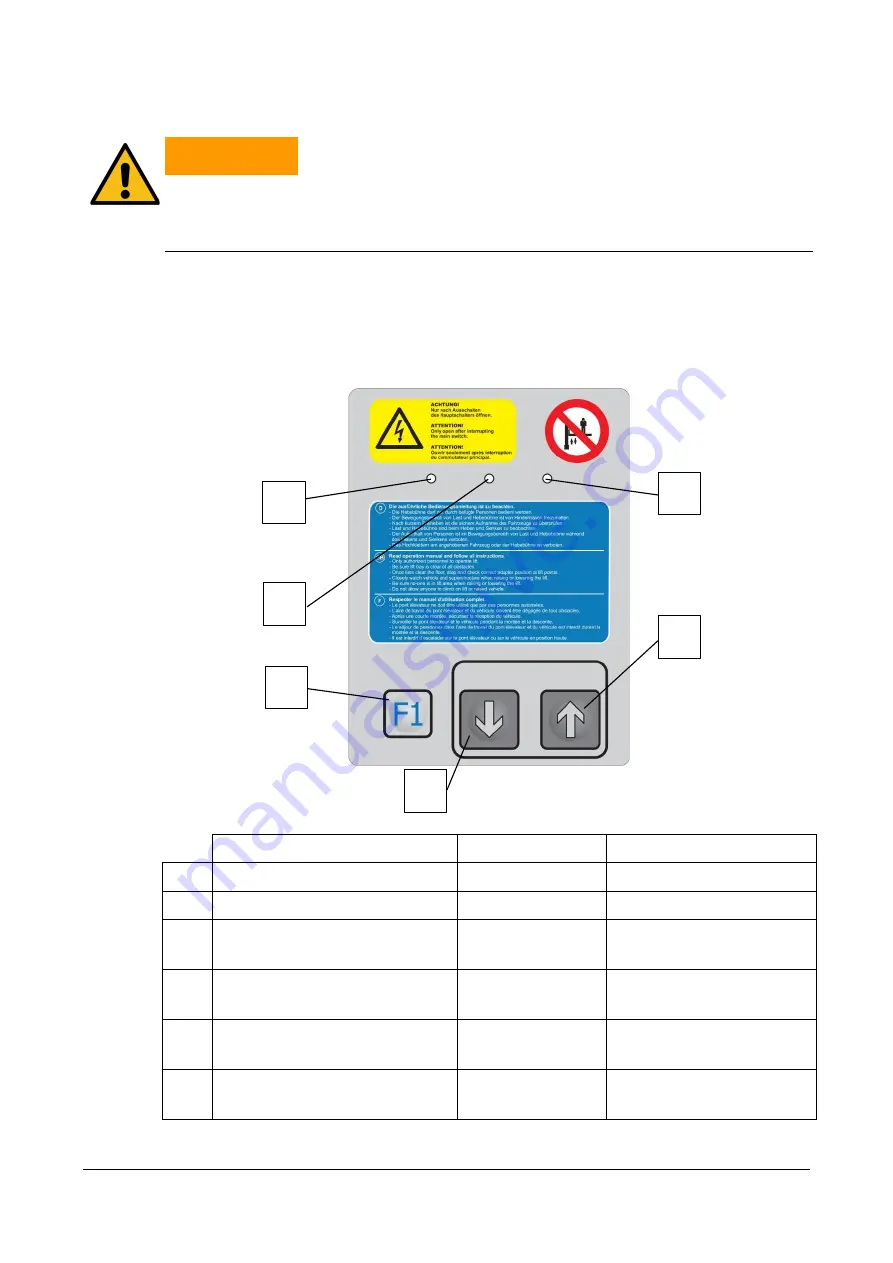
BA322301-en
25
4.3
Raising and Lowering Cycles
WARNING
When installing or removing heavy vehicle components, ensure that the centre
of gravity does not shift to a dangerous extent! The vehicle may tip off the lift.
The vehicle must be secured against tipping by suitable means.
4.3.1
Control Elements
The buttons of the control elements are assigned with the following functions:
Small control element
Function
Short form
Comments
A
Raise the lift
LIFT UP
---
B
Lower the lift
LIFT DOWN
---
C
Multifunction key 1
F1
without function, only
for service personnel
D
LED light, red:
Malfunction or error code
---
see section “LED signal
codes”
E
LED light, yellow:
Warning or error code
---
see section “LED signal
codes”
F
LED light, green:
Ready for operation
---
---
D
E
C
B
A
F
Summary of Contents for ZS SQUARE II 3.5
Page 16: ...16 BA322301 en 2 4 3 Set up Diagrams...
Page 32: ...32 BA322301 en B B 3 4 B C 5...
Page 52: ...20 PL670000_002 de...