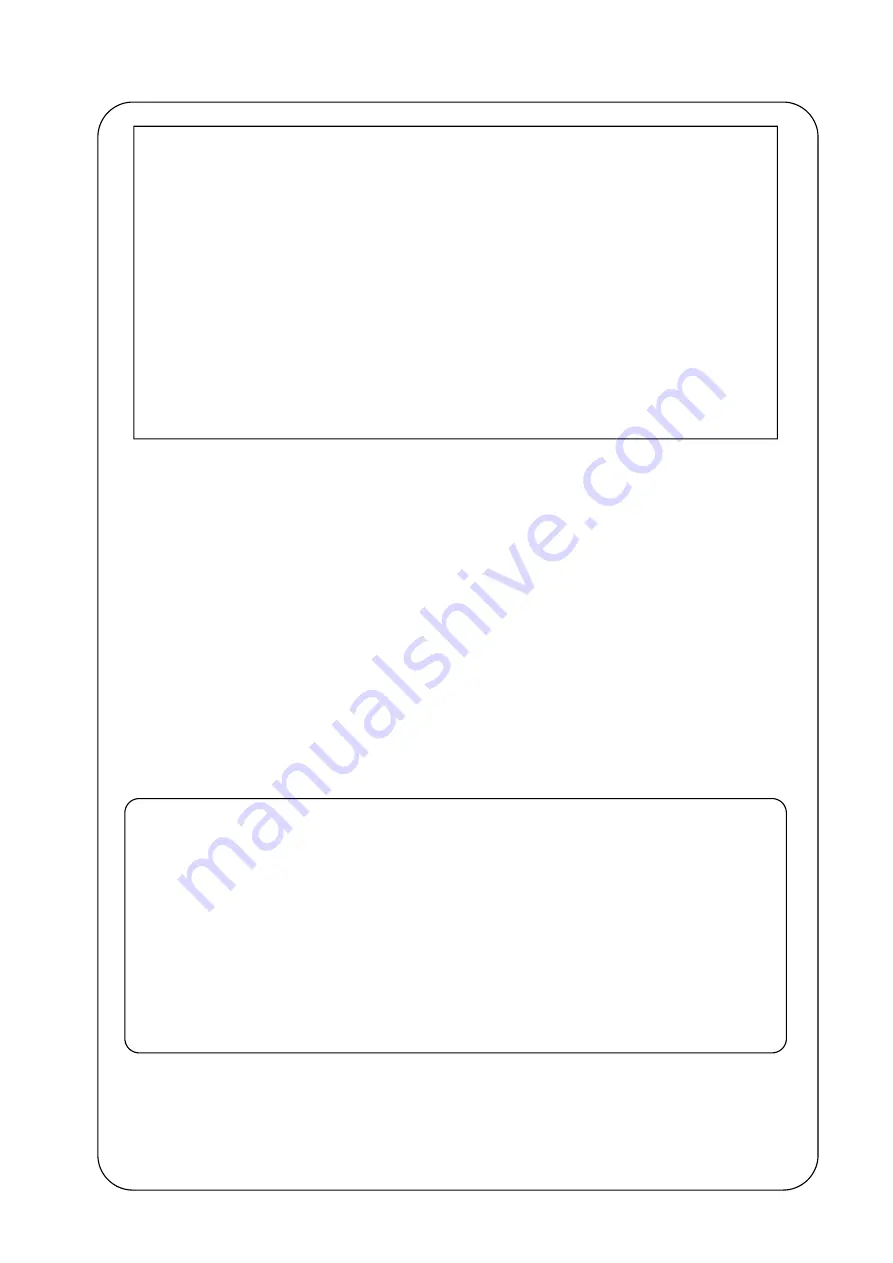
OPERATION
MANUAL
Inverter CO
2
/MAG Gas Shielded
Welding Machine
NBC-250D/350M
Attention:
For your safety, please only allow technicians to operate, maintain
and repair this machine.
You are advised to read this operation manual thoroughly before
operating the machine. Please keep this manual for future reference
and safety information.