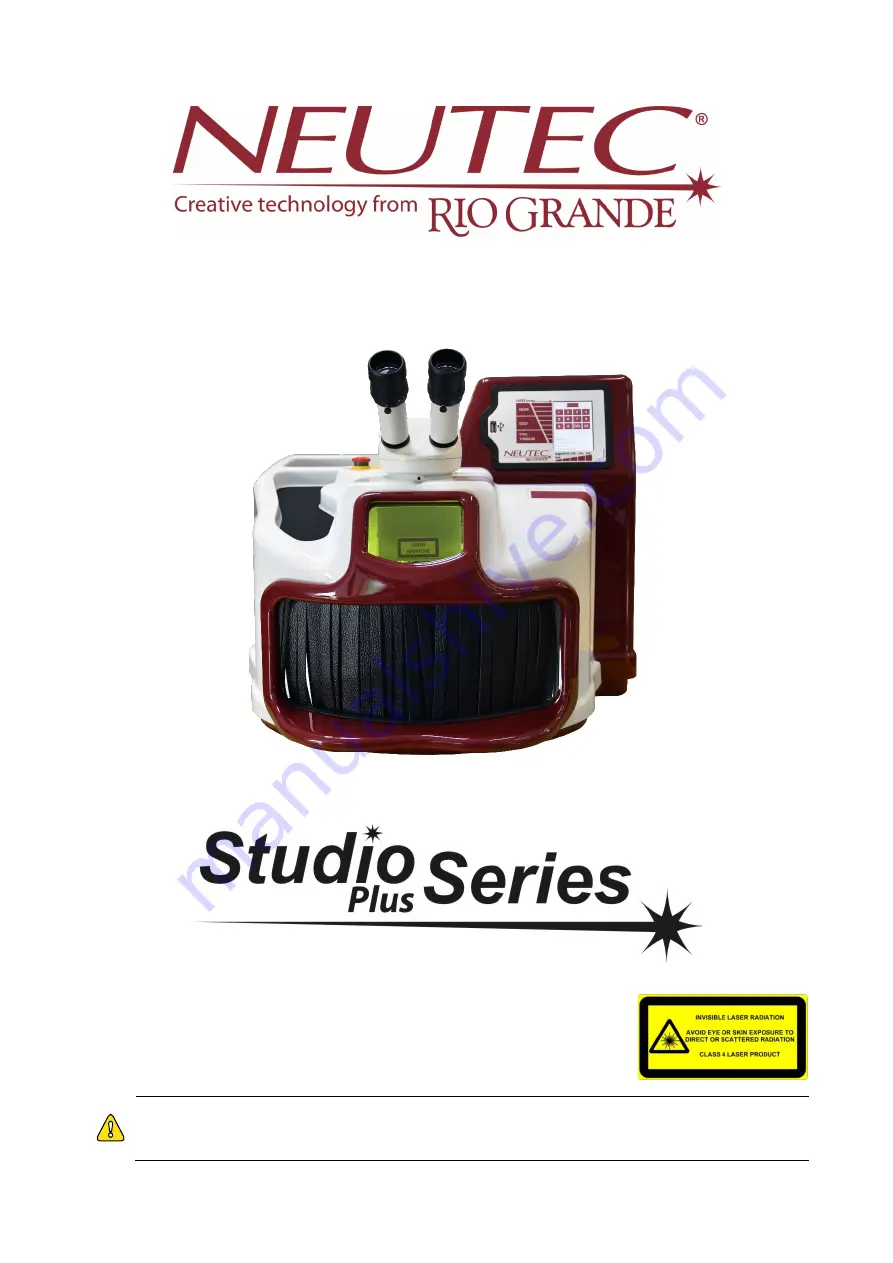
MAN00080-01-EN
IMPORTANT:
Please read this handbook before using
the Neutec/USA® Studio™ Plus
Laser Welder
MIDI00SP
This device has been designed in compliance with IEC EN 61010-1 and IEC EN 60825-1 safety standards to prevent injury to the
operator if used correctly and properly. However, no engineering design can make this device safe if it is not used and maintained
properly and in compliance with safety standards. This manual should be read carefully and in its entirety before performing any
operation. Failure to follow instructions and safety standards may cause injury to the operator and the device.