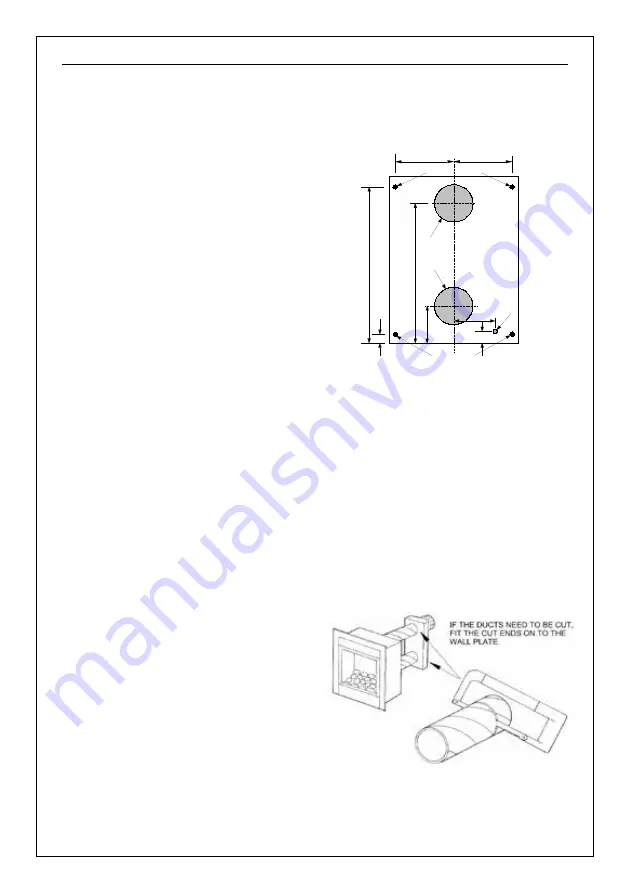
Page 23
3.9.3.
Surface Mounted Firebox Preparation
On the inside wall:
1. Measure the height of the hearth (in the
case of a raised installation ascertain the
height of the top surface of the hearth)
and mark a horizontal line on the wall at
the same height.
2. Mark a vertical line on the wall on the
centre line of the installation. From the
horizontal line measure up and mark
125mm and 470mm. At these two points
drill 125mmØ holes with a core drill (see
3. Ensure that any loose cavity wall
insulation is replaced with Rockwool or
equivalent material.
4. Erect the false chimney breast or deep
rebate fire surround. Any items made of
combustible materials shall be suitably
protected with 12mm thick ‘Superlux’ or
equivalent material and at least 50mm
thickness Rockwool or equivalent
material inserted between the top, back
and sides of the appliance and the
superlux. If the appliance is to be
installed on a wall made of combustible
materials the flue must be encased in a
metal so that there is at least 50mm
space between the flue and the duct.
This space must be filled with mineral
wool.
5. If the enclosure is to be plastered it must
be allowed to dry before proceeding.
The plaster must be completely dry
before any prolonged use of the
appliance.
6. Any combustible material to the rear of
the firebox, on the inside wall and within
the false surround shall be removed.
7. Mark out, drill, plug and fit the four eye
screws onto the rear wall of the fireplace
opening as shown in
8. At this point install the hearth, back panel
and mantel if one is to be used.
9. Bring the gas supply into the recess and
position so it lines up with the gas entry
port in the rear of the convector box. This
is situated 105 - 165mm to the left of
centre and 40mm above the floor of the
recess (see
540
30
470
1
25
40
200
200
105 - 165
eye-screw
positions
125 dia.
125 dia.
Gas Inlet
eye-screw
positions
C
L
Figure 31
10. Measure the distance
L
between the
face side of the back panel and the
outside surface of the outer leaf through
the drilled Ø125mm holes (see
). From this figure
deduct 170mm
.
Cut two pieces of Ø100mm duct to the
new figure and deburr the ends. (Note;
Two 440mm lengths of 100mmØ duct
are supplied which is sufficient for most
inset installations. Extra lengths of duct
up to 1000mm can be supplied. (This is
also the maximum length of duct that is
permitted to be used.)