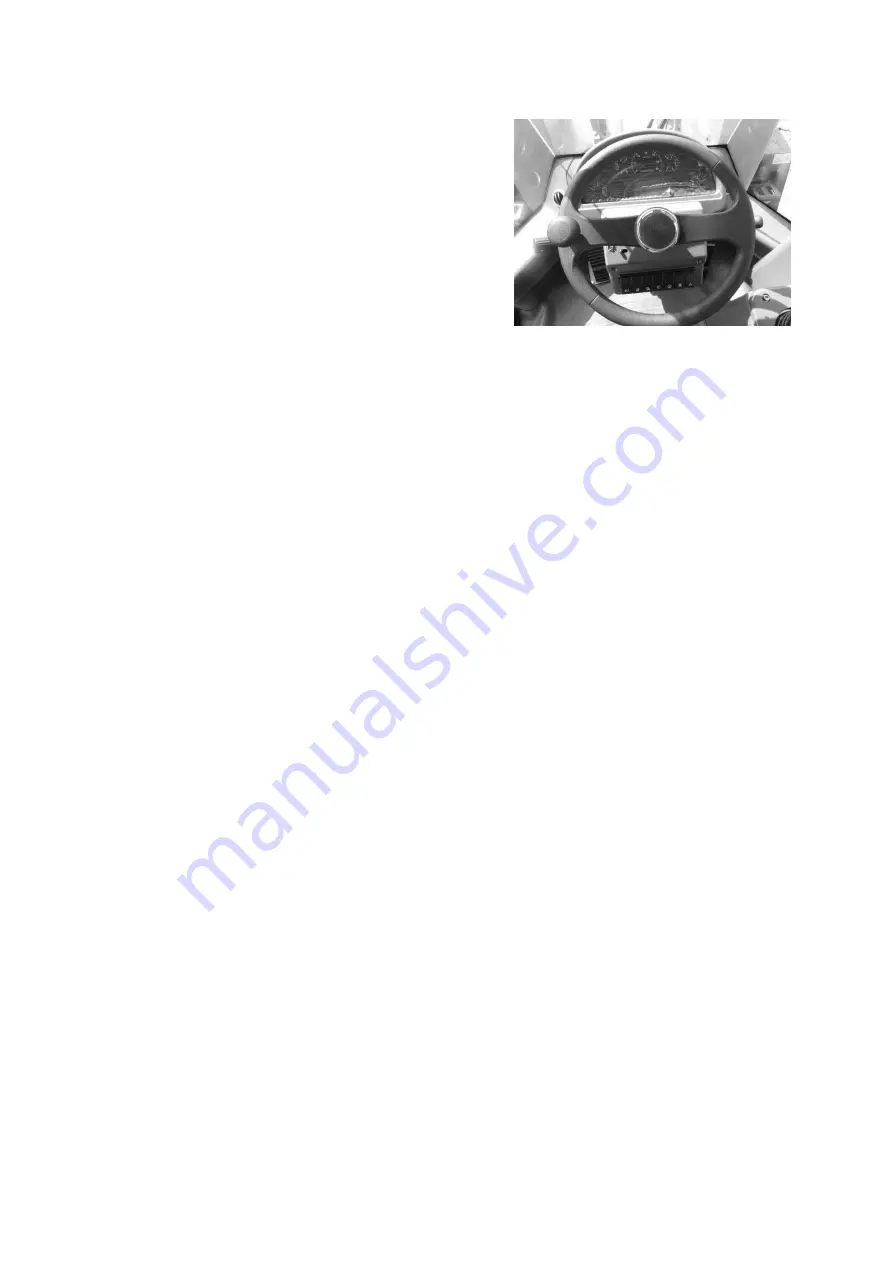
88
6. In case there is a corner ahead, please
operate the loader in accordance with the
local laws and regulations relating to traffic.
When the loader is about to turn, pull or push
the turn lamp handle in the corresponding
direction. As indicated in the figure below,
push forwards the handle if the loader will turn
left, and pull backwards the handle if the
loader will turn right. Now the front/rear turn
lamps on one side of the loader and the
corresponding turn indicating lamp on the
instrument board will come on, so as to warn
the loaders and persons around the loader
that this loader is about to turn. Thereafter,
turn the steering wheel in the turning
direction, so as to make the loader to turn.
The loader is equipped with the articulated-type fully-hydraulic coaxial-flow-amplifying
powered steering gear, and the turning angle of the steering wheel is not equal to the
turning angle of the loader. When the steering wheel is turned continuously, the turning
angle of the loader will increase until the intended angle is obtained. The turning speed of
the loader will increase as the turning speed of the steering wheel increases.
After being turned, the steering wheel will not return to the original position automatically,
and the turning angle of the loader will remain unchanged. Therefore, after the turning of
the loader is completed, be sure to turn the steering wheel in opposite direction so as to
eliminate the relative angle between front and rear frames and make the loader run
straightly. After the turning operation is completed, pull the turn lamp switch to the middle
position, so as to turn off the turn lamps and turn indicating lamp.
For the purpose of carrying out the turning operation when the loader is travelling at high
speed, be sure to release the accelerator pedal firstly. If necessary, apply the service
brake to slow down the loader and then carry out the turning operation, so as to ensure
the safety.
WARNING: Do not carry out turning operation on a slope. The turning operation
may be completed only after the loader has been driven to the flat ground.
7. For the purpose of braking the loader, just release the accelerator pedal, and then
smoothly push down the brake pedal.
WARNING: When the loader is running at high speed, unless any emergency
circumstance occurs, be sure not to push down the brake pedal to the end violently,
otherwise the emergency braking may cause safety accident or damage the loader.
4.3.4 PARKING OF LOADER
Drive the loader to a flat place which is free from the risk of falling stone, landslide or