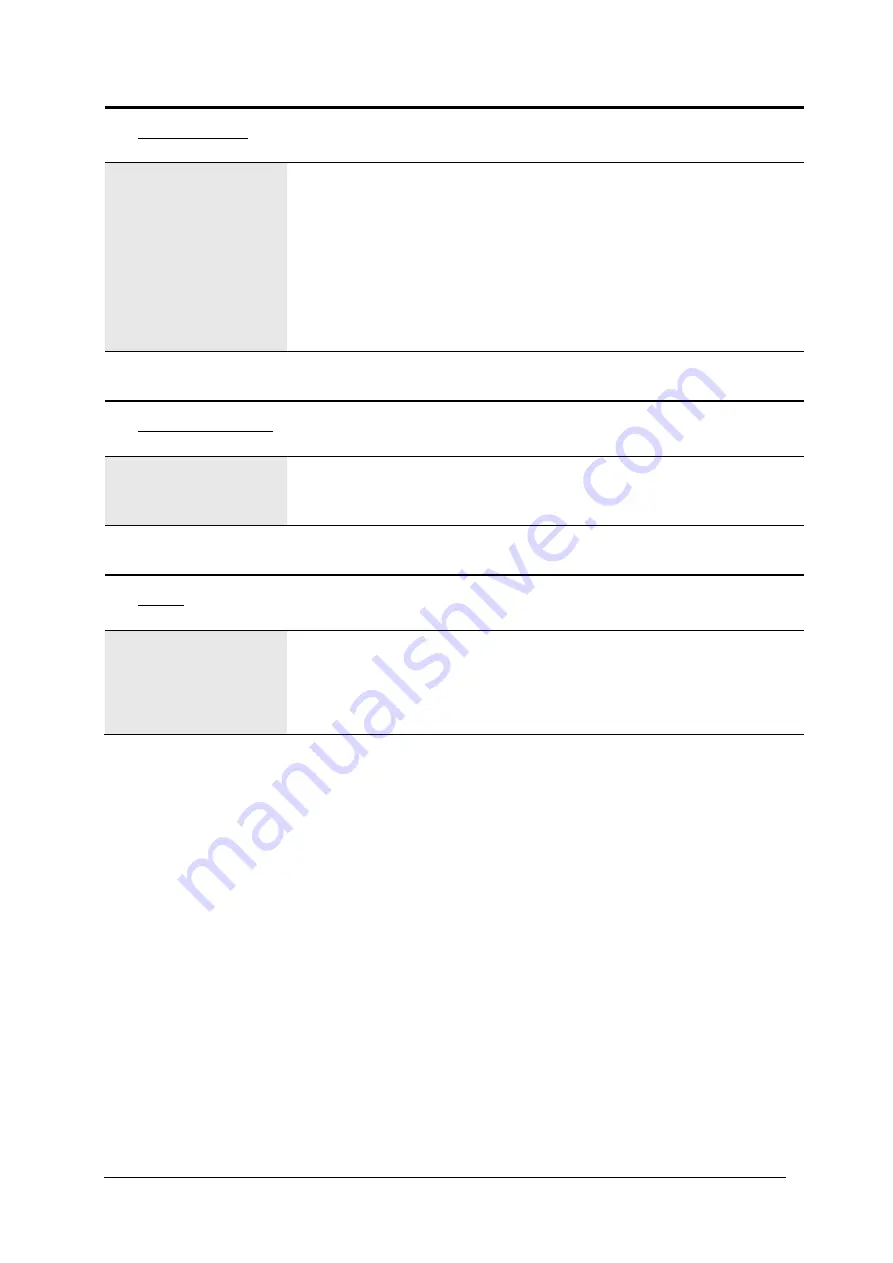
17/84
2.7.
Packing and Storage
In order to ensure sufficient protection during dispatch and transport, the machine and its components
were packed carefully. The machine should be checked for damage upon receipt. The packing of the
device consists of recyclable materials. Place them into the containers provided for recycling so that
they can be recycled.
The machine may not be operated in case of damage. Damaged cables and plug connectors also pose
a safety risk and must not be used.
If the machine is not operated immediately after unpacking, it must be protected from moisture and
dirt.
2.8.
Environmental protection
Packaging material, cleaning agents, used or remaining operating supplies, and unwrapped wear
parts, such as drive belts or engine oils, must be recycled in accordance with local environmental
regulations.
2.9.
Disposal
Render the worn out devices unusable once the period of use has expired, and especially when there
are malfunctions.
Dispose of the machine according to the environmental regulations valid in your country.
Electrical waste must not be dumped in general waste. Take the machine to a central collection point.
Summary of Contents for COMPACTCUT 201 D
Page 2: ...2 84...
Page 9: ...9 84 10 Spare parts 52...
Page 52: ...52 84 10 SPARE PARTS...
Page 53: ...53 84 Fig 0...
Page 54: ...54 84 Fig 01 Fig 1 12 CC201D Abb 1 11 CC201P PL PV...
Page 55: ...55 84 Fig 1 11 CC201P PL PV...
Page 57: ...57 84 Fig 1 12 CC201D...
Page 59: ...59 84 Fig 01 2...
Page 61: ...61 84 Fig 01 3...
Page 63: ...63 84 Fig 02 CC201D 1 1 7 8 6 CC201PV CC201P CC201PL 10 9 11 CC201P CC201PL CC201PV CC201PL 16...
Page 65: ...65 84 Fig 03...
Page 66: ...66 84 Fig 03 1 CC201D...
Page 68: ...68 84 Fig 03 1 CC201P PV PL 8 1...
Page 70: ...70 84 Fig 03 2...
Page 72: ...72 84 Fig 03 3...
Page 74: ...74 84 Fig 03 4...
Page 76: ...76 84 Fig 03 5 Fig 03 6...
Page 78: ...78 84 Fig 04...
Page 80: ...80 84 Fig 05 Fig 06...
Page 83: ...83 84...
Page 84: ...84 84...