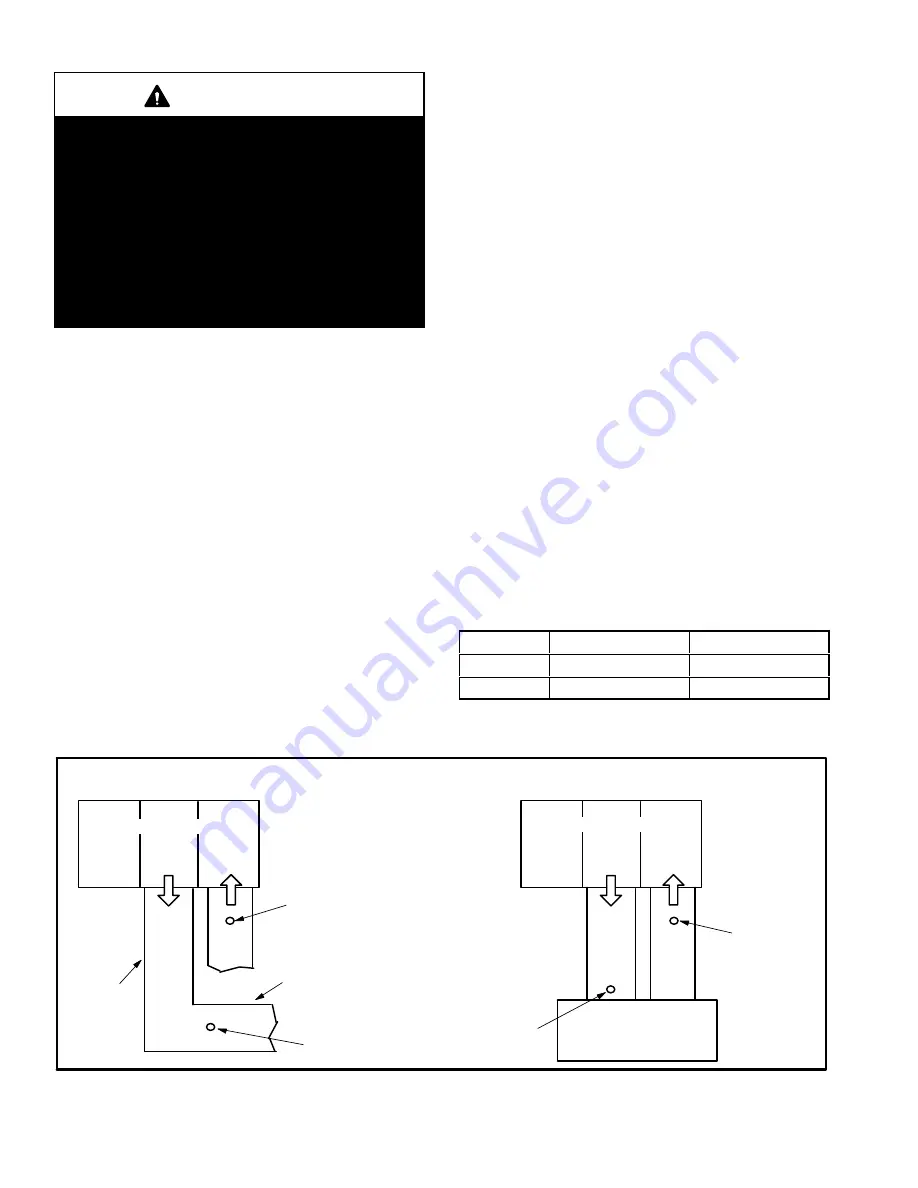
Page 13
508117-01 2/2021
WARNING
1-Make sure that unit is installed in accordance with the
installation instructions and applicable codes.
2-Inspect all electrical wiring, both field‐ and factory‐
installed, for loose connections. Tighten as required.
3-Check to ensure that refrigerant lines do not rub against
the cabinet or against other refrigerant lines.
4-Check voltage at disconnect switch. Voltage must be
within range listed on nameplate. If not, consult power
company and have voltage condition corrected before
starting unit.
5-Make sure filters are new and in place before start‐up.
B-Blower Access
1- Disconnect jack/plug connector to blower motor. Also
disconnect jack/plug connector heating limit switches
on gas units.
2- Remove screws on either side of blower assembly
3- Pull base toward outside of unit.
C-Determining Unit CFM
IMPORTANT - Multi-staged supply air
units are
factory-set to run the blower at full speed when there is a
blower (G) demand without a heating or cooling demand.
Refer to the field-provided, design specified CFM for all
modes of operation. Use the following procedure to adjust
motor pulley to deliver the highest CFM called for in the
design spec. See Inverter Start-Up section to set blower
CFM for all modes once the motor pulley is set.
Variable Air Volume Units - Refer to the Variable Air
Volume Start-Up section.
1- The following measurements must be made with a
dry indoor coil. Run blower (G demand) without a
cooling demand. Measure the indoor blower shaft
RPM. Air filters must be in place when measurements
are taken.
2- With all access panels in place, measure static
pressure external to unit (from supply to return).
Blower performance data is based on static pressure
readings taken in locations shown in figure 14.
Note - Static pressure readings can vary if not taken
where shown.
3- Referring to page 17, use static pressure and RPM
readings to determine unit CFM. Use page 18 when
installing units with any of the optional accessories
listed.
4- The blower RPM can be adjusted at the motor pulley.
Loosen Allen screw and turn adjustable pulley
clockwise to increase CFM. Turn counterclockwise to
decrease CFM. See figure 15. Do not exceed
minimum and maximum number of pulley turns as
shown in table 3.
TABLE 3
MINIMUM AND MAXIMUM PULLEY ADJUSTMENT
Belt
Minimum Turns Open
Maximum Turns Open
A Section
No minimum
5
B Section
1*
6
*No minimum number of turns open when B belt is used on
pulleys 6” O.D. or larger.
FIGURE 14
LOCATION OF STATIC PRESSURE READINGS
SUPPLY AIR
READING
LOCATION
SUPPLY
RE
TURN
INSTALLATIONS WITH DUCTWORK
SUPPLY
RE
TURN
INSTALLATIONS WITH CEILING DIFFUSERS
MAIN
DUCT RUN
FIRST BRANCH
OFF OF MAIN RUN
DIFFUSER
ROOFTOP UNIT
ROOFTOP UNIT
SUPPLY AIR
READING
LOCATION
RETURN AIR
READING LOCATION
RETURN AIR
READING
LOCATION