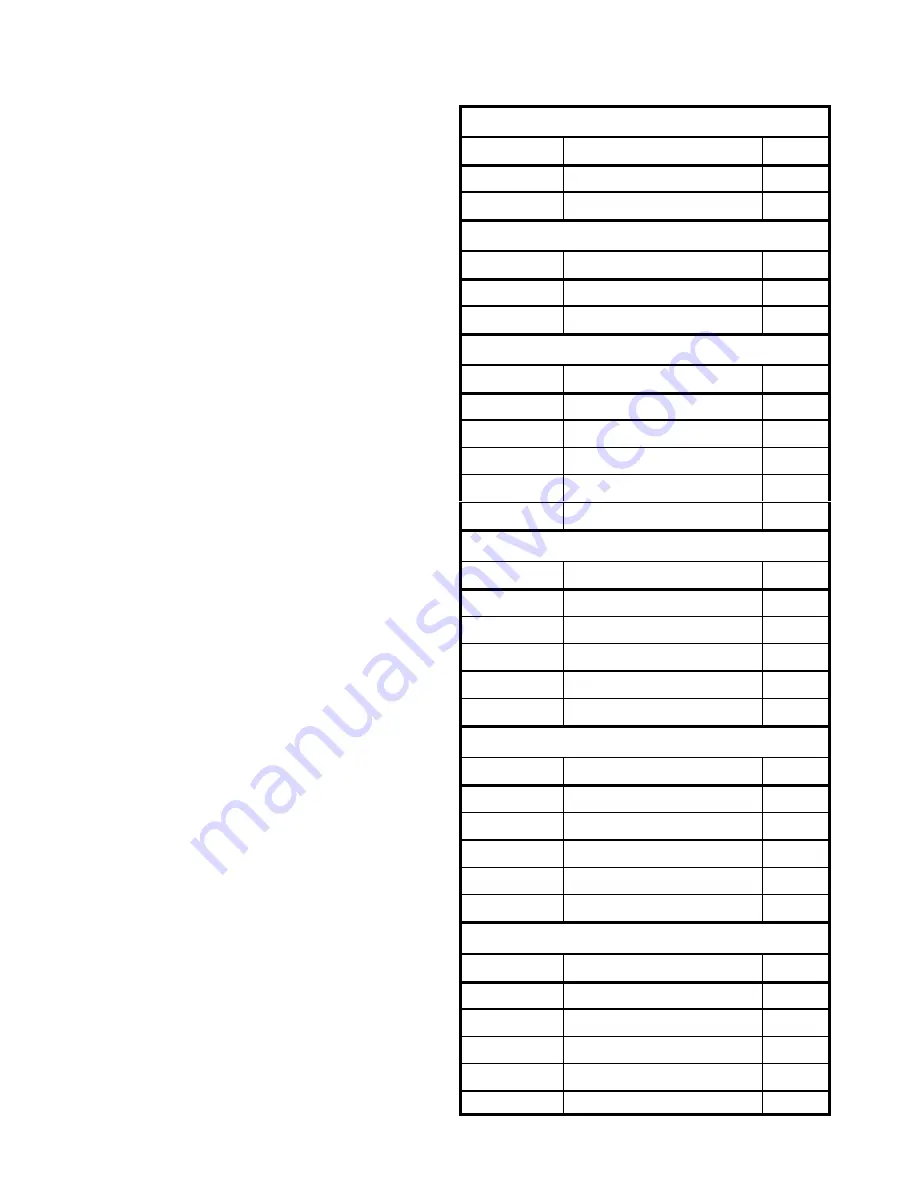
Page 33
508117-01 2/2021
Set Minimum Position 2
Use the following mobile service app menu in the Unit
Controller to set “Min OCP Blwr Low” for the blower CFM
below the “midpoint” CFM. When navigating into this
menu, the Unit Controller will run damper calibration and
allow damper position adjustment.
RTU MENU > SETTINGS > RTU OPTIONS > DAMPER
Tap "Next" to skip tabs and complete damper position
calibration until "Damper Calibration Blower Speed High"
tab appears.
Measure the intake air CFM. If the CFM is lower than the
design specified CFM for ventilation air, use the Unit
Controller to increase the damper percent open. If the
CFM is higher than specified, decrease the damper
percent open.
Note - Intake air CFM can also be determined using the
outdoor air temperature, return air temperature and
mixed air temperature. Refer to the economizer or
outdoor air damper installation instructions.
E-Inverter Bypass Option
The supply air inverter is factory-set to by-pass the
inverter manually. To by-pass the inverter and operate the
blower in the constant air volume mode, use the following
Unit Controller menu and set to “engaged”:
SETTINGS > RTU OPTIONS > BLOWER > VFD
BYPASS
To configure the unit to by-pass the inverter automatically,
use the following Unit Controller menu.
SETUP > INSTALL
Press SAVE until the menu reads:
CONFIGURATION ID 1
Change the 6
th
character position to A for automatic
bypass option.
Press SAVE
Caution - Units not equipped with an inverter will have the
6
th
character set to N, indicating the inverter is not
bypassed. The blower motor could be damaged and/or
result in product or property damage if the setting is
changed to automatic or manual.
TABLE 19
MINIMUM AND MAXIMUM CFM
Gas Heat Minimum CFM
Unit
Gas Heat Size
Airflow CFM
LGM156-300
Low, Std. Med.
4500
LGM156-300
High
5125
Electric Heat Minimum CFM
Unit
Heat Size (kW)
Airflow CFM
LCM156
All
5200
LCM180-300
All
6000
Cooling Minimum CFM - 220 CFM/ton
Unit
Blower Speed
Airflow CFM
LGM/LCM156
Low, Med. Low, Med., Med. High
2860
LGM/LCM180
Low, Med. Low, Med., Med. High
3300
LGM/LCM210
Low, Med. Low, Med., Med. High
3850
LGM/LCM240
Low, Med. Low, Med., Med. High
4400
LGM/LCM300
Low, Med. Low, Med., Med. High
5500
Cooling Minimum CFM - 280 CFM/ton
Unit
Blower Speed
Airflow CFM
LGM/LCM156
High
3640
LGM/LCM180
High
4200
LGM/LCM210
High
4900
LGM/LCM240
High
5600
LGM/LCM300
High
7000
Smoke and Ventilation Minimum CFM - 150 CFM/ton
Unit
Not Applicable
Airflow CFM
LGM/LCM156
NA
1950
LGM/LCM180
NA
2250
LGM/LCM210
NA
2625
LGM/LCM240
NA
3000
LGM/LCM300
NA
3750
Heating and Cooling Maximum CFM - 480 CFM/ton
Unit
Blower Speed
Airflow CFM
LGM/LCM156
High
6240
LGM/LCM180
High
7200
LGM/LCM210
High
8400
LGM/LCM240
High
9600
LGM/LCM300
High
12000