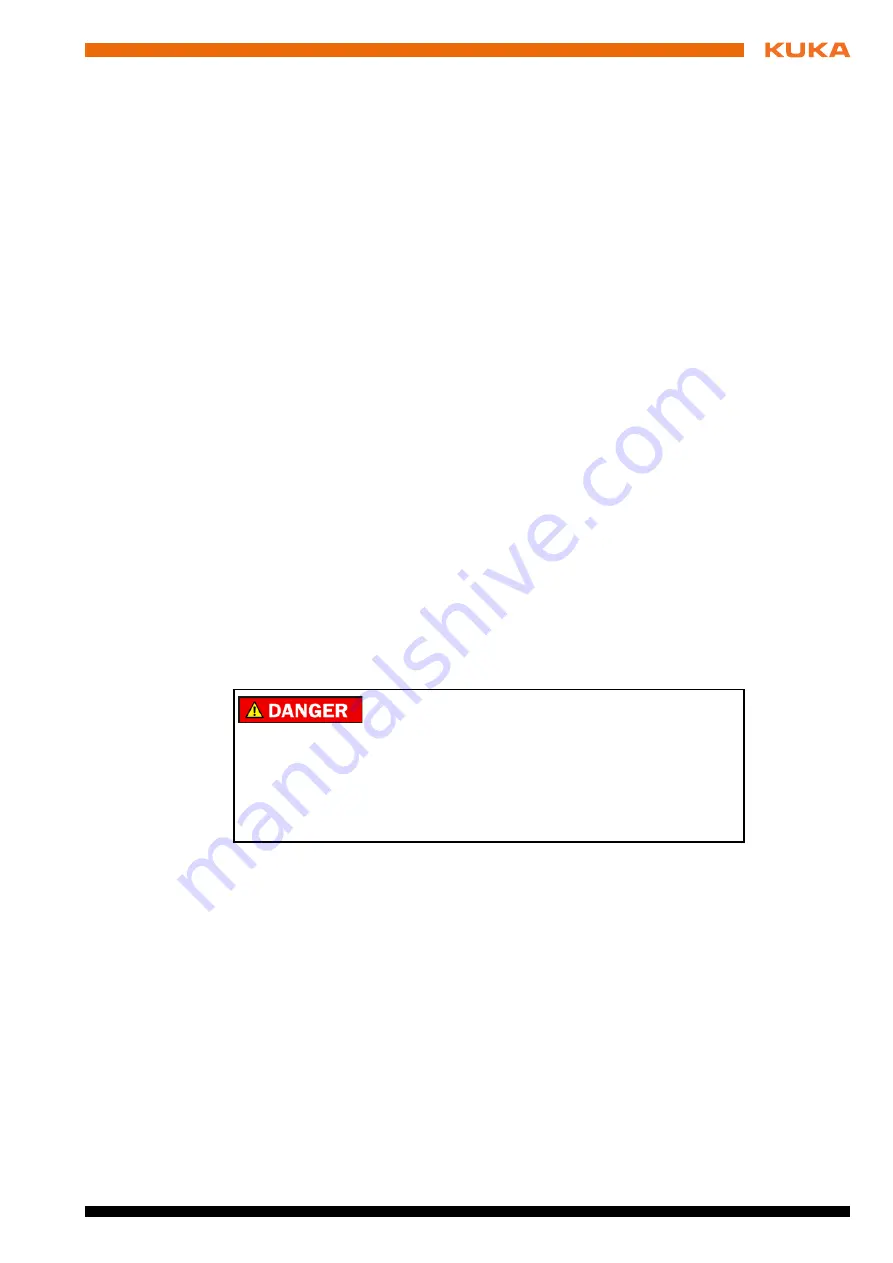
Issued: 08.09.2015 Version: Spez KR 30, 60-2 JET V1
5 Safety
If the manipulator or an external axis (optional) comes to a standstill for no ap-
parent reason, the danger zone must not be entered until an EMERGENCY
STOP has been triggered.
5.5.6
Maintenance and repair
After maintenance and repair work, checks must be carried out to ensure the
required safety level. The valid national or regional work safety regulations
must be observed for this check. The correct functioning of all safety functions
must also be tested.
The purpose of maintenance and repair work is to ensure that the system is
kept operational or, in the event of a fault, to return the system to an operation-
al state. Repair work includes troubleshooting in addition to the actual repair
itself.
The following safety measures must be carried out when working on the indus-
trial robot:
Carry out work outside the danger zone. If work inside the danger zone is
necessary, the user must define additional safety measures to ensure the
safe protection of personnel.
Switch off the industrial robot and secure it (e.g. with a padlock) to prevent
it from being switched on again. If it is necessary to carry out work with the
robot controller switched on, the user must define additional safety mea-
sures to ensure the safe protection of personnel.
If it is necessary to carry out work with the robot controller switched on, this
may only be done in operating mode T1.
Label the system with a sign indicating that work is in progress. This sign
must remain in place, even during temporary interruptions to the work.
The EMERGENCY STOP devices must remain active. If safety functions
or safeguards are deactivated during maintenance or repair work, they
must be reactivated immediately after the work is completed.
Faulty components must be replaced using new components with the same
article numbers or equivalent components approved by KUKA Roboter GmbH
for this purpose.
Cleaning and preventive maintenance work is to be carried out in accordance
with the operating instructions.
Robot controller
Even when the robot controller is switched off, parts connected to peripheral
devices may still carry voltage. The external power sources must therefore be
switched off if work is to be carried out on the robot controller.
The ESD regulations must be adhered to when working on components in the
robot controller.
Voltages in excess of 50 V (up to 600 V) can be present in various components
for several minutes after the robot controller has been switched off! To prevent
life-threatening injuries, no work may be carried out on the industrial robot in
this time.
Water and dust must be prevented from entering the robot controller.
Before work is commenced on live parts of the robot sys-
tem, the main switch must be turned off and secured
against being switched on again. The system must then be checked to en-
sure that it is deenergized.
It is not sufficient, before commencing work on live parts, to execute an
EMERGENCY STOP or a safety stop, or to switch off the drives, as this does
not disconnect the robot system from the mains power supply. Parts remain
energized. Death or severe injuries may result.
Summary of Contents for KR 30-2
Page 6: ...6 85 Issued 08 09 2015 Version Spez KR 30 60 2 JET V1 KR 30 2 JET KR 60 2 JET...
Page 8: ...8 85 Issued 08 09 2015 Version Spez KR 30 60 2 JET V1 KR 30 2 JET KR 60 2 JET...
Page 12: ...12 85 Issued 08 09 2015 Version Spez KR 30 60 2 JET V1 KR 30 2 JET KR 60 2 JET...
Page 62: ...62 85 Issued 08 09 2015 Version Spez KR 30 60 2 JET V1 KR 30 2 JET KR 60 2 JET...
Page 66: ...66 85 Issued 08 09 2015 Version Spez KR 30 60 2 JET V1 KR 30 2 JET KR 60 2 JET...
Page 72: ...72 85 Issued 08 09 2015 Version Spez KR 30 60 2 JET V1 KR 30 2 JET KR 60 2 JET...
Page 74: ...74 85 Issued 08 09 2015 Version Spez KR 30 60 2 JET V1 KR 30 2 JET KR 60 2 JET...
Page 82: ...82 85 Issued 08 09 2015 Version Spez KR 30 60 2 JET V1 KR 30 2 JET KR 60 2 JET...
Page 85: ...85 85 Issued 08 09 2015 Version Spez KR 30 60 2 JET V1 KR 30 2 JET KR 60 2 JET...