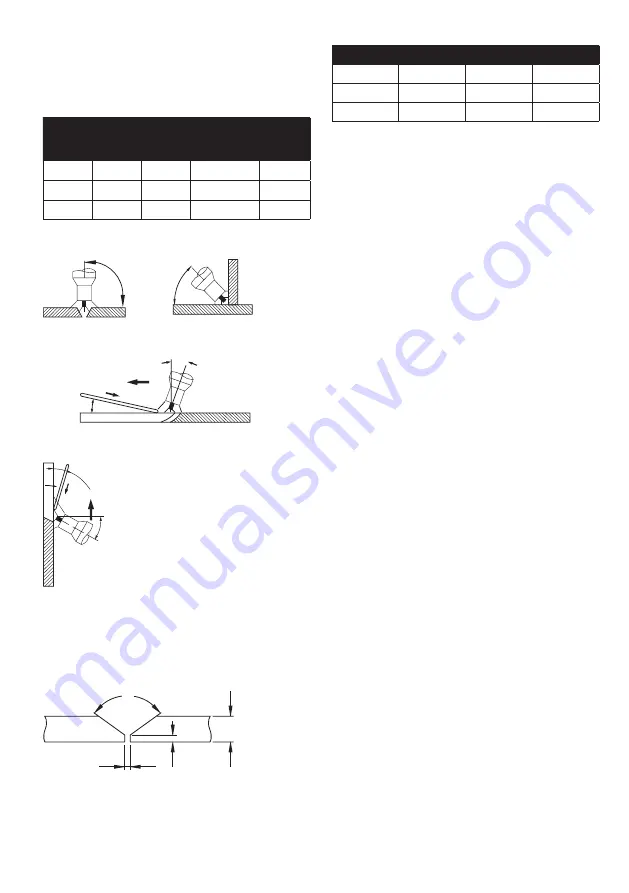
| 39
EN
Protective gas:
For TIG welding, it is necessary to use argon with a puri-
ty of 99.99%. Determine the amount of flow according
to Table 3.
Table 3
Welding
current
(A)
Diameter of
electrode
(mm)
Welding nozzle
Flow of
gas
(l/min)
n (°)
Ø (mm)
6 - 70
1.0
4/5
6/8,0
5 - 6
60 - 140
1.6
4/5/6
6.5/8.0/9.5
6 - 7
120 - 240
2.4
6/7
9.5/11.0
7 - 8
Holding the welding torch during welding:
90°
45°
Position W (PA)
Position H (PB)
10 – 30°
15 – 40°
Position S (PF)
10
- 30°
20 - 30°
Position S (PF)
Preparation of basic material:
Table 4 lists the material preparation values.
Dimensions are determined according to pic. 6.
Picture 6
a
s
α
d
Table 4
s (mm)
a (mm)
d (mm)
α (°)
0 - 3
0
0
0
3
0
0.5 (max)
0
4 - 6
1 - 1.5
1 - 2
60
Basic rules during welding by TIG method:
1. Purity - grease, oil and other impurities must be
removed from the weld during welding. It is also
necessary to mind purity of additional material and
clean gloves of the welder during welding.
2. Leading additional material - oxidation must be
prevented. To do so, flashing end of additional ma-
terial must be always under the protection of gas
flowing from the hose.
3. Type and diameter of tungsten electrodes - it is
necessary to choose them according to the values
of the current, polarity, type of basic material and
composition of protective gas.
4. Sharpening of tungsten electrodes - sharpening the
tip of the electrode should be done in trav-erse/
horizontal direction. The tinier the roughness of
the surface of the tip is, the calmer the burning of
the el. arc is as well as the greater durability of the
electrode is.
5. The amount of protective gas - it has to be adjust-
ed according to the type of welding or according to
the size of gas hose. After finishing the welding gas
must flow sufficiently long to protect material and
tungsten electrode against oxidation.
Typical TIG welding errors and their impact on weld
quality:
The welding current is too -
Low:
unstable welding arc
High:
Tungsten electrode tip breaks lead to turbulent
arcing.
Further, mistakes may be caused by poor welding torch
guidance and poor addition of additive material.
Welding in method MMA
Switch the machine to MMA mode - coated electrode.
Table 5 lists the general values for the choice of the
electrode, depending on its diameter and the thickness
of the base material. These data are not absolute and
are informative only. For exact selection, follow the in-
structions provided by the manufacturer of the electro-
des. The current used depends on the position of the
welding and the joint type and increases according to
the thickness and dimensions of the part.