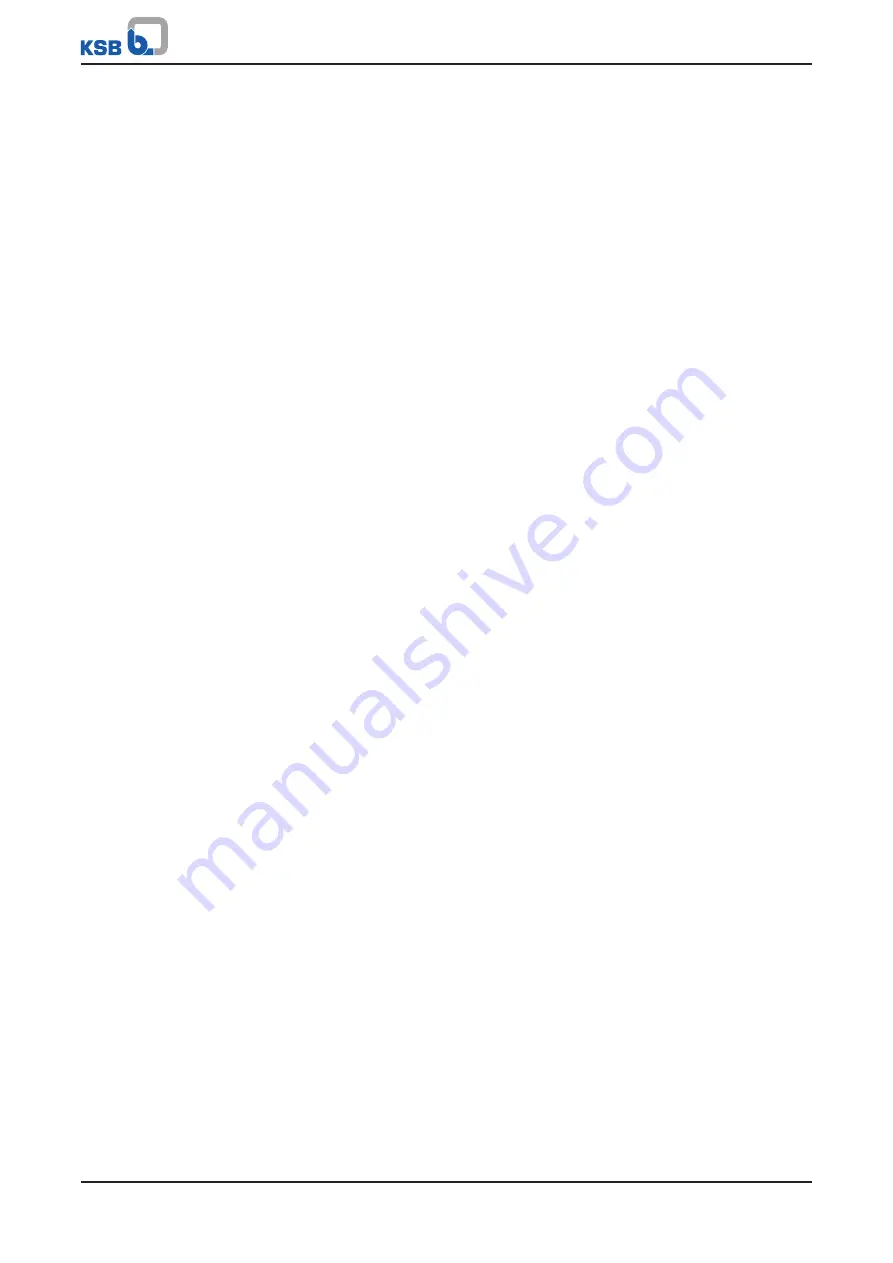
2 Safety
11 of 126
Amacan S
1589.837/01-EN
▪
When taking the pump set out of service always adhere to the procedure
described in the manual. (
▪
Decontaminate pumps which handle fluids posing a health hazard.
▪
As soon as the work has been completed, re-install and re-activate any safety-
relevant devices and protective devices. Before returning the product to service,
observe all instructions on commissioning. (
2.8 Unauthorised modes of operation
Never operate the pump (set) outside the limits stated in the data sheet and in this
operating manual.
The warranty relating to the operating reliability and safety of the pump (set)
supplied is only valid if the equipment is used in accordance with its intended use.
Summary of Contents for Amacan S 1000-600
Page 125: ......