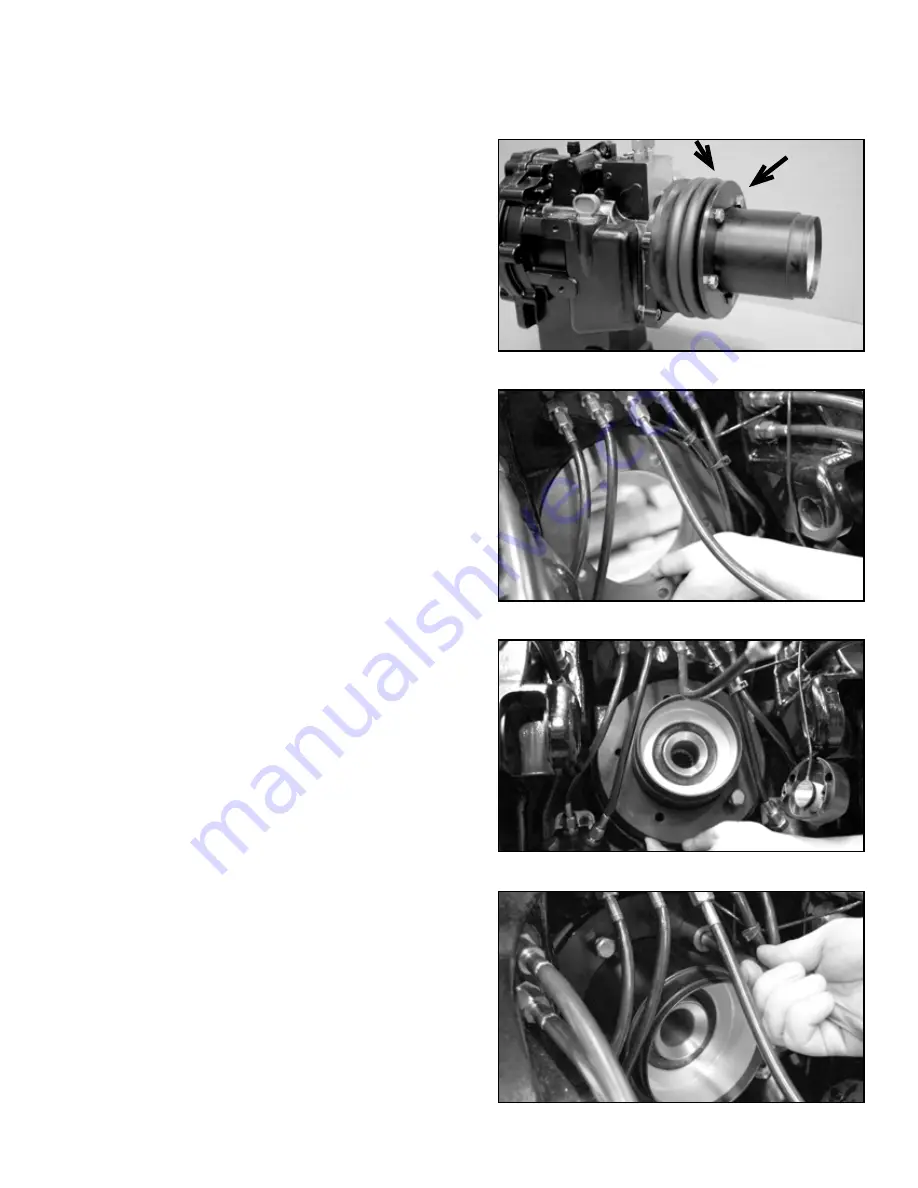
KONRAD 600B SERIES INSTALLATION GUIDE
JANUARY 2019 - V4.0
PAGE 13
Step 2: Direct Mount / Tailpiece installation
2.1
Remove the tailpiece compression ring and
oring from the transmission tailpiece by removing
the five (5) H.H.C.S. and washers.
2.2
Position the tailpiece compression ring and
oring onto the gimbal housing by sliding the ring
and gasket from the bottom of the gimbal housing
upward under the trim hoses and into position.
2.3
With the transmission and tailpiece mounted
on the engine, position the tailpiece to slide
through the gimbal housing. Hold the tailpiece
compression ring and oring so it will slide onto the
tailpiece housing while positioning the engine and
transmission into place.
2.4
Apply red
Loctite
to the (5) H.H.C.S. that
were removed in Step 2.1. Start the bolts by hand
and tighten in a star pattern at 5 lb ft (6.8 Nm)
increments until 35 lb ft (47.5 Nm) is obtained.