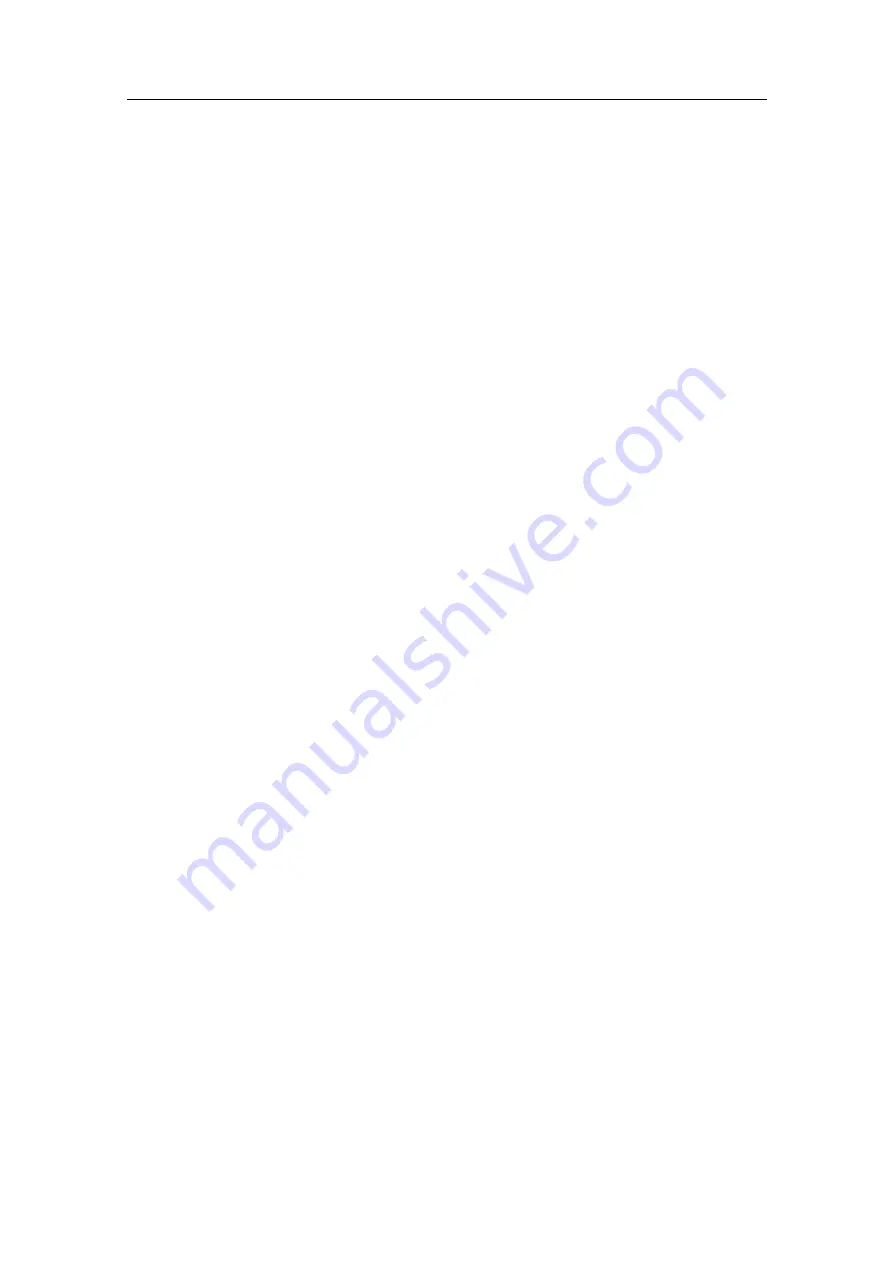
Kongsberg EM 710
If there is any point in the fore-aft direction which does not
change height with respect to the water line with changes in
vessel speed, this will be the ideal location for the motion sensor
as it will eliminate any errors from squat induced height changes
which is not measured by current motion sensors.
8.3.2 Heading sensor
This sensor can either be based upon:
• GPS measurements like Seapath 200 or POS/MV
• Fibre optic gyro compass
• Standard gyro compass
The heading sensor dynamic accuracy should be in the order
of one third of the transmit transducer beamwidth or better (i.e.
0.3º for a 1º beamwidth).
The sensor must be aligned to the vessel centre line to provide an
accuracy better than a fifth of the transmit transducer beamwidth
(i.e. 0.2º for a 1º beamwidth).
Compasses sensitive to acceleration should be mounted close to
CG (Centre of Gravity)
Please see the sensor installation manual for any further
instructions on installation and alignment.
The output of the sensor must be verified with the vessel having
a known heading such as when it is in drydock. Alignment
accuracy can also be evaluated with the vessel tied (in opposite
directions) along a quay with known heading. A calibration
survey should afterwards be performed at sea to confirm correct
performance.
8.3.3 Positioning system
Most positioning systems are today based on Global Navigation
Satellite System technology (GNSS) such as GPS, GLONASS
and/or (later) GALILEO. The location of the positioning system,
antenna must be measured, including its height (if geoide height
is a measured and used parameter). It should be noted that some
GNSS based systems use two (or more) antennas to provide
vessel heading, if so the installation manual for the system should
be consulted for how these antennae are to be aligned and how
accurately the location of the antennae need to be measured.
8.3.4 Water line
With the vessel in normal trim, i.e with an indicated pitch angle
of zero from the motion sensor, the distance to the waterline
may be measured anywhere on the vessel. Otherwise it must be
measured at the alongship physical location of the motion sensor.
100
164851/C
Summary of Contents for EM 710
Page 1: ...Installation Manual EM 710 Multibeam echo sounder ...
Page 2: ......
Page 44: ...Kongsberg EM 710 Figure 10 Transducer mounting principles 42 164851 C ...
Page 63: ...Cable layout Figure 20 Transceiver Unit front view 0 5 x 1 degree 164851 C 61 ...
Page 88: ...Kongsberg EM 710 Figure 42 Cable clamp Transceiver Unit cable clamp on page 133 86 164851 C ...
Page 113: ...Installation drawings 164851 C 111 ...
Page 114: ...Kongsberg EM 710 10 1 2 1 mounting frame assembly RX module 112 164851 C ...
Page 115: ...Installation drawings 164851 C 113 ...
Page 116: ...Kongsberg EM 710 10 1 3 2 mounting frame assembly TX RX module 114 164851 C ...
Page 117: ...Installation drawings 164851 C 115 ...
Page 118: ...Kongsberg EM 710 10 1 4 0 5 x 1 gondola 116 164851 C ...
Page 119: ...Installation drawings 164851 C 117 ...
Page 120: ...Kongsberg EM 710 10 1 5 Transducer TX1 Outline dimensions 118 164851 C ...
Page 121: ...Installation drawings 164851 C 119 ...
Page 122: ...Kongsberg EM 710 10 1 6 Transducer TX2 Outline dimensions 120 164851 C ...
Page 123: ...Installation drawings 164851 C 121 ...
Page 124: ...Kongsberg EM 710 10 1 7 Transducer RX1 Outline dimensions 122 164851 C ...
Page 125: ...Installation drawings 164851 C 123 ...
Page 126: ...Kongsberg EM 710 10 1 8 Transducer RX2 Outline dimensions 124 164851 C ...
Page 127: ...Installation drawings 164851 C 125 ...
Page 128: ...Kongsberg EM 710 10 1 9 HWS Operator Station Outline dimensions 126 164851 C ...
Page 129: ...Installation drawings 10 1 10 Transceiver Unit Outline dimensions 164851 C 127 ...
Page 130: ...Kongsberg EM 710 128 164851 C ...
Page 132: ...Kongsberg EM 710 130 164851 C ...
Page 133: ...Installation drawings 10 1 12 Transceiver Unit mounting bracket 164851 C 131 ...
Page 134: ...Kongsberg EM 710 10 1 13 Junction Box outline dimensions 132 164851 C ...
Page 135: ...Installation drawings 10 1 14 Transceiver Unit cable clamp 164851 C 133 ...