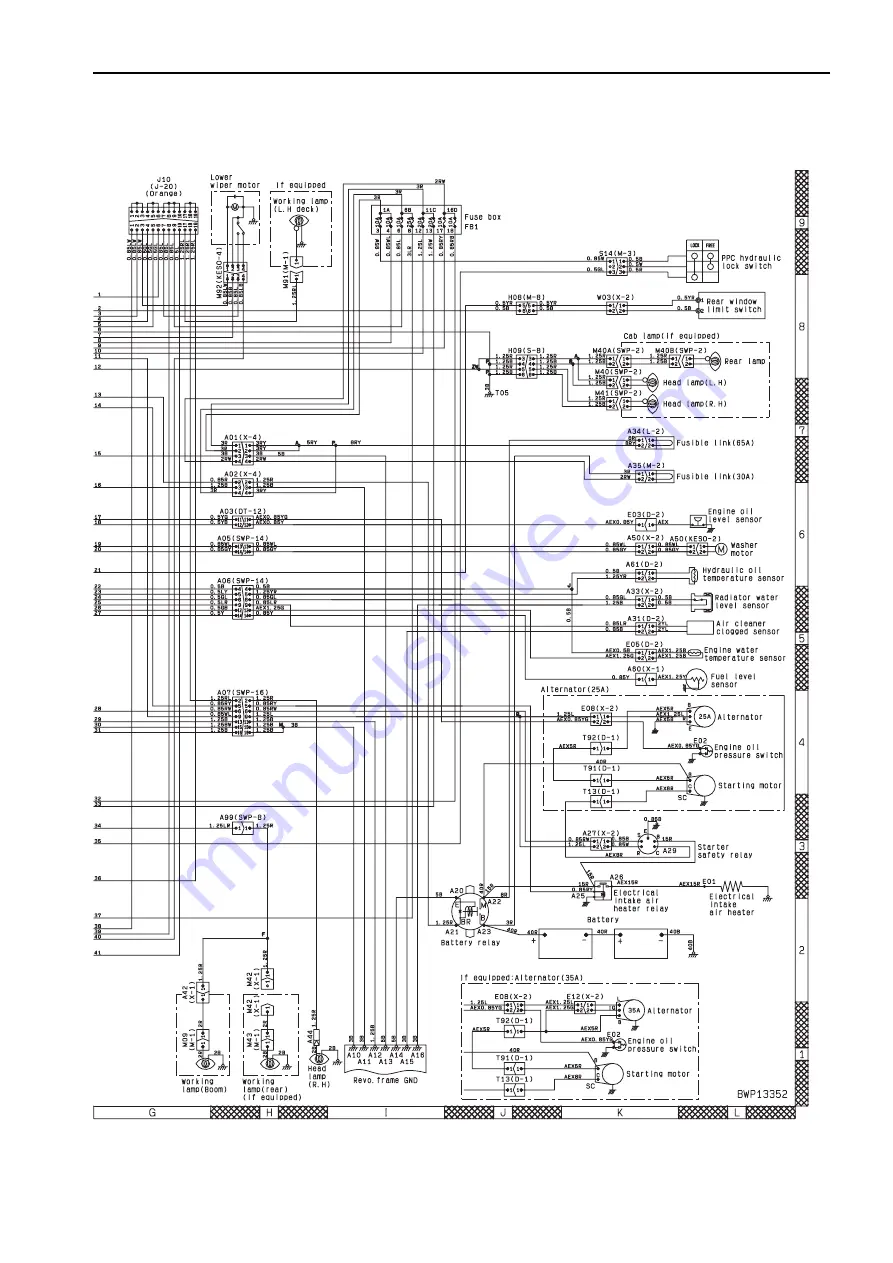
PC130-7
20-229
TROUBLESHOOTING
CONNECTOR ARRANGEMENT DRAWING AND ELECTRIC
CIRCUIT DIAGRAM OF EACH SYSTEM
(1)
a
This circuit diagram is made by excerpting the monitor panel system, engine preheating/starting/charging
system, lower wiper system, and light system from the general electric circuit diagram.
Summary of Contents for PC130-7
Page 6: ......
Page 18: ......
Page 86: ...20 168 PC130 7 TESTING AND ADJUSTING Items related to engine 1 PM CLINIC SERVICE...
Page 87: ...PC130 7 20 169 TESTING AND ADJUSTING Items related to hydraulic equipment 1 PM CLINIC SERVICE...
Page 90: ......
Page 111: ......
Page 117: ......
Page 157: ......
Page 161: ...PC130 7 20 313 TROUBLESHOOTING Circuit diagram related to wiper motor 112 1...
Page 163: ...PC130 7 20 315 TROUBLESHOOTING Circuit diagram related to wiper motor 113 1...
Page 165: ...PC130 7 20 317 TROUBLESHOOTING Circuit diagram related to windshield washer motor 114 1...
Page 167: ...PC130 7 20 319 TROUBLESHOOTING Circuit diagram related to wiper motor 115 1...
Page 169: ...PC130 7 20 321 TROUBLESHOOTING Circuit diagram related to wiper motor 116 1...
Page 171: ...PC130 7 20 323 TROUBLESHOOTING Circuit diagram related to swing holding brake solenoid 203 1...
Page 173: ...PC130 7 20 325 TROUBLESHOOTING Circuit diagram related to 2 stage relief solenoid 205 1...
Page 175: ...PC130 7 20 327 TROUBLESHOOTING Circuit diagram related to travel speed shifting solenoid 206 1...
Page 177: ...PC130 7 20 329 TROUBLESHOOTING Circuit diagram related to swing holding brake solenoid 213 1...
Page 179: ...PC130 7 20 331 TROUBLESHOOTING Circuit diagram related to 2 stage relief solenoid 215 1...
Page 181: ...PC130 7 20 333 TROUBLESHOOTING Circuit diagram related to travel speed shifting solenoid 216 1...
Page 183: ...PC130 7 20 335 TROUBLESHOOTING Circuit diagram related to model selection connector 217 1...
Page 185: ...PC130 7 20 337 TROUBLESHOOTING Circuit diagram related to S NET 218 1...
Page 189: ...PC130 7 20 341 TROUBLESHOOTING Circuit diagram related to pump pressure sensor 224 1...
Page 191: ...PC130 7 20 343 TROUBLESHOOTING Circuit diagram related to sensor power supply 226 1...
Page 193: ...PC130 7 20 345 TROUBLESHOOTING Circuit diagram related to engine speed sensor 227 1...
Page 195: ...PC130 7 20 347 TROUBLESHOOTING Circuit diagram related to PC EPC solenoid 232 1...
Page 197: ...PC130 7 20 349 TROUBLESHOOTING Circuit diagram related to PC EPC solenoid 233 1...
Page 199: ...PC130 7 20 351 TROUBLESHOOTING Circuit diagram related to overload pressure sensor 251 1...
Page 201: ......
Page 205: ...PC130 7 20 357 TROUBLESHOOTING Circuit diagram related to fuel control dial 308 1...
Page 207: ...PC130 7 20 359 TROUBLESHOOTING Circuit diagram related to battery relay 315 1...
Page 209: ......
Page 214: ......
Page 221: ......
Page 233: ...PC130 7 20 419 TROUBLESHOOTING Circuit diagram related to PPC lock solenoid E 8 1...
Page 247: ...PC130 7 20 433 TROUBLESHOOTING Circuit diagram related to swing lock switch E 18 1...
Page 249: ......
Page 253: ...PC130 7 20 439 TROUBLESHOOTING Circuit diagram related to windshield washer motor E 20 1...
Page 255: ...PC130 7 20 441 TROUBLESHOOTING Circuit diagram related to lower windshield wiper E 21 1...
Page 257: ...PC130 7 20 443 TROUBLESHOOTING Circuit diagram related to caution buzzer stop switch E 22 1...
Page 263: ...PC130 7 20 449 TROUBLESHOOTING Circuit diagram related to arm IN oil pressure switch E 25 1...
Page 265: ...PC130 7 20 451 TROUBLESHOOTING Circuit diagram related to arm OUT oil pressure switch E 26 1...
Page 284: ...20 470 PC130 7 TROUBLESHOOTING Circuit diagram related to air conditioner E 32 1...
Page 288: ...20 474 PC130 7 TROUBLESHOOTING Circuit diagram related to air conditioner E 32 1...
Page 293: ......
Page 316: ......
Page 342: ......