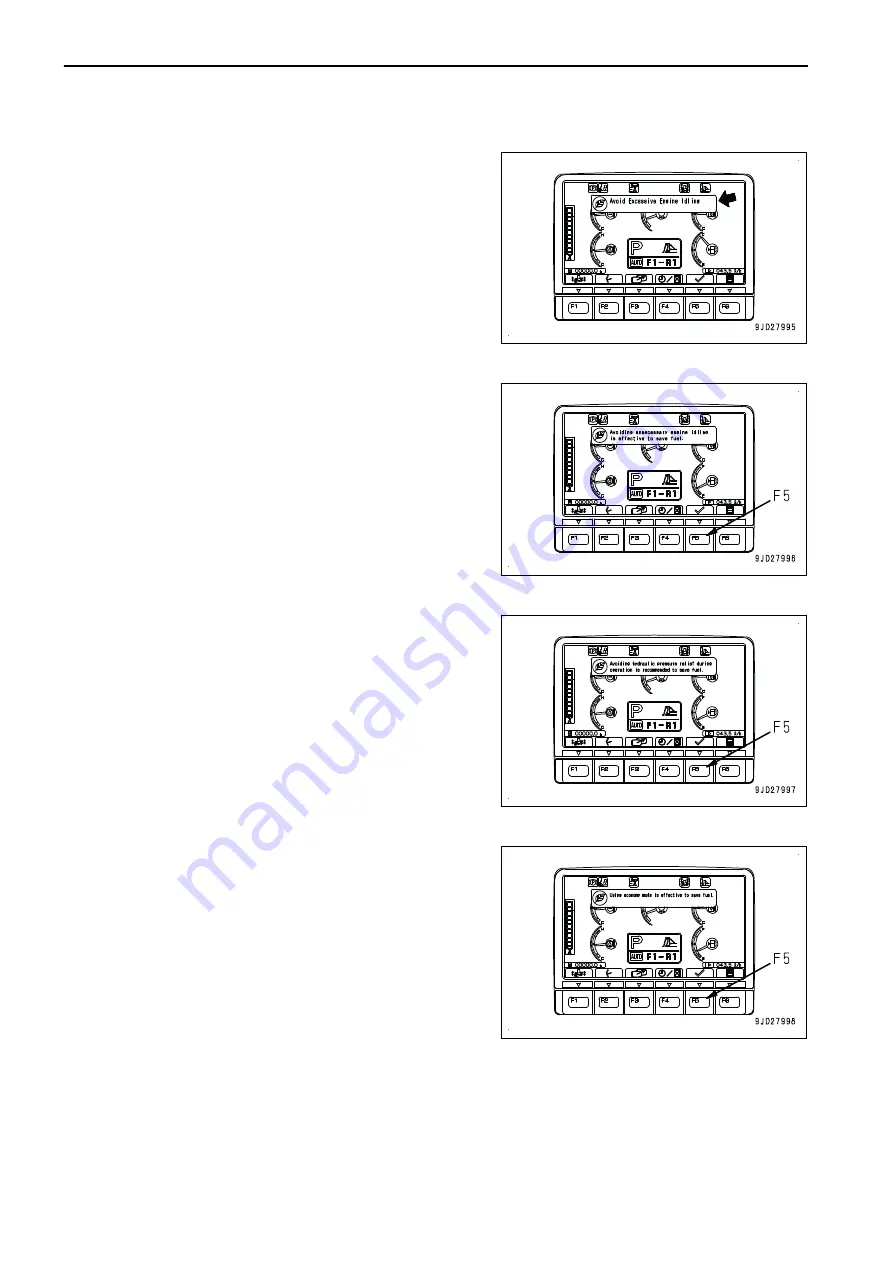
ECO GUIDANCE
The guidance for energy saving operation to reduce the fuel
consumption may be displayed during operation.
The details of the guidance are as follows:
Idling Stop Guidance
If no operation is performed for more than 5 minutes, and the
engine is idling, the idling stop message is displayed on the
machine monitor. When waiting for work or taking short break,
stop the engine to reduce unnecessary fuel consumption.
The idling stop guidance goes out if any lever is operated again
or switch F5 is pressed.
Guidance To Avoid Hydraulic Relief
If the hydraulic oil is kept relieved for more than 10 seconds
during operation, the hydraulic relief deterrence message is
displayed on the machine monitor.
The hydraulic relief deterrence message goes out 5 seconds
later or when switch F5 is pressed.
E Mode Recommendation Guidance
If light-load work is continued for more than 10 minutes in P
mode, E mode recommendation message is displayed. When
working on light load, set the operation mode to E to reduce
unnecessary fuel consumption.
E mode recommendation guidance goes out more than 5 sec-
onds after or when switch F5 is pressed.
EXPLANATION OF COMPONENTS
OPERATION
3-32
Summary of Contents for D375A-8
Page 2: ......
Page 11: ...Do not repeatedly handle and lift loads FOREWORD VIBRATION LEVELS 1 9...
Page 13: ...Scale interval of the circles is 1 m FOREWORD INTRODUCTION 1 11...
Page 310: ......
Page 394: ......
Page 395: ...SPECIFICATIONS 5 1...
Page 448: ......
Page 449: ...REPLACEMENT PARTS 7 1...
Page 465: ......