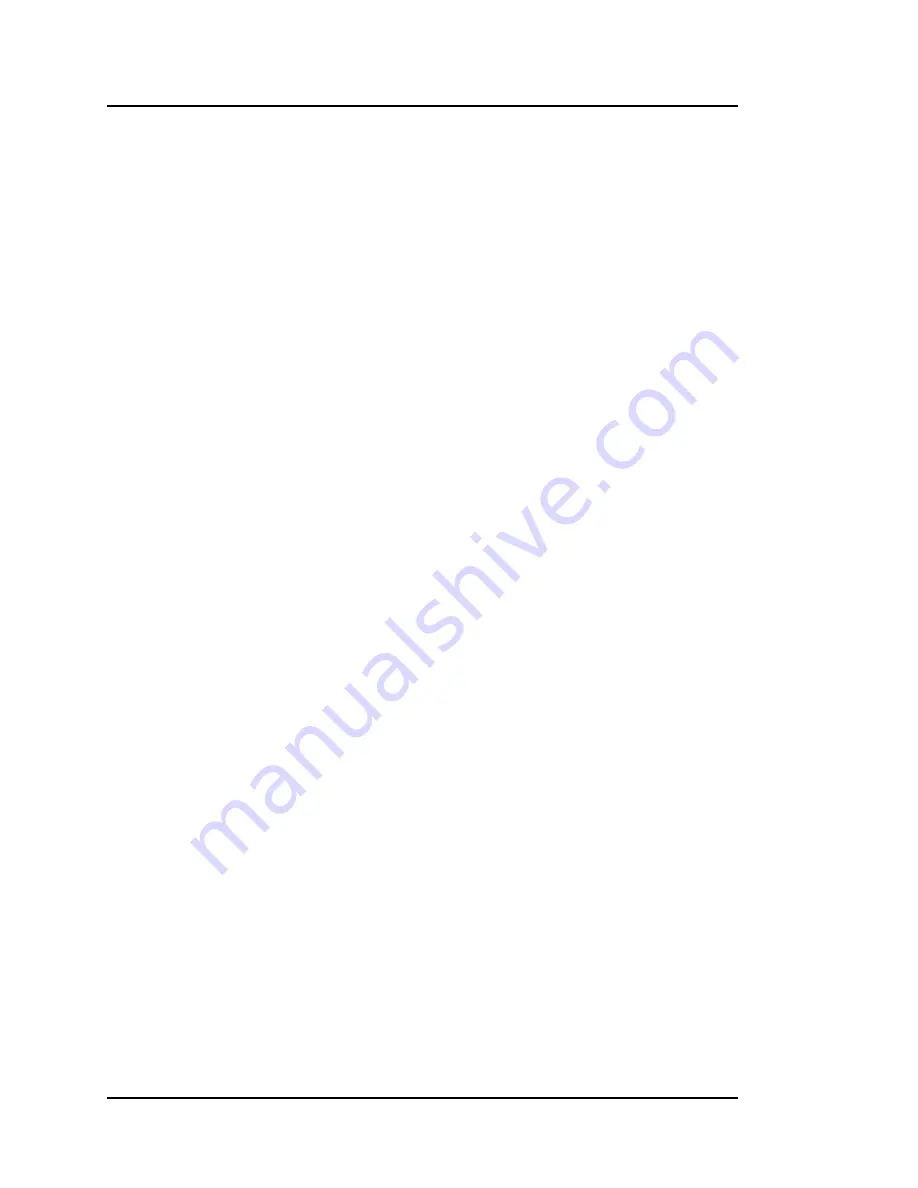
Danaher Motion
06/2005
Master-Slave
M-SS-005-03 Rev
E
119
5. 4
S
IMULATED AND
M
ASTER
-S
LAVE
A
XES
Simulated axes are used to enhance machine control. They typically are with
gearing and camming. Three common uses are:
1.
To act as fixed speed masters for slaved axes.
2.
To monitor physical axes.
3.
To synchronize slaved axes.
5.4.1. Fixed-Speed
Masters
The most common use for a simulated axis is as a fixed-speed master axis
for geared or cammed axes. This is used for testing or as part of normal
operation. The simulated axis is normally set to a fixed speed using
JOG
.
Slave axes are driven without a physical motor. For example, if you want to
view a cam table, you can use a simulated axis running at a fixed speed. In a
sense, the simulated axis provides the ideal condition where the master
speed is precisely fixed. This can allow you to fine-tune cams and carefully
inspect the synchronization of geared axes.
Fixed-speed simulated axes and cams are combined to allow you to produce
virtually any profile you need for a machine. You need only load the profile,
cam table and drive the axis with a fixed-speed simulated axis.
5.4.2.
Monitor Physical Axes
Simulated axes are used to monitor physical axes for machine control by
slaving a simulated axis to a physical axis and monitoring the position and/or
velocity of the simulated axis. For example, if you slave a non-rotary
simulated axis to a rotary physical axis, you can monitor the total distance
the physical axis has traveled because any variable from a simulated axis
can be used to fire events. You can generate events based on the simulated
axis. The position feedback of a simulated axis can drive a Programmable
Limit Switch (PLS) to add more monitoring flexibility.
5.4.3.
Synchronize Slave Axes
Many machines have multiple slaved axes that are controlled as a group.
Normally, synchronization is maintained when these axes share a single
physical axis as a master. However, on some machines, there are special
modes of operation where a physical axis cannot provide all the necessary
functions. Consider a machine where a minimum speed must be maintained
on the slave axes even if the master axis stops. In this case, you can insert a
simulated axis between the physical master and slave drives. To do this,
slave a simulated axis to the physical master and then slave the other axes
to the simulated axis. Use events to tell when the physical axis is above or
below the minimum and use
JOG
to keep the simulated axis above the
desired minimum to keep the slave axes moving even if the physical master
stops.