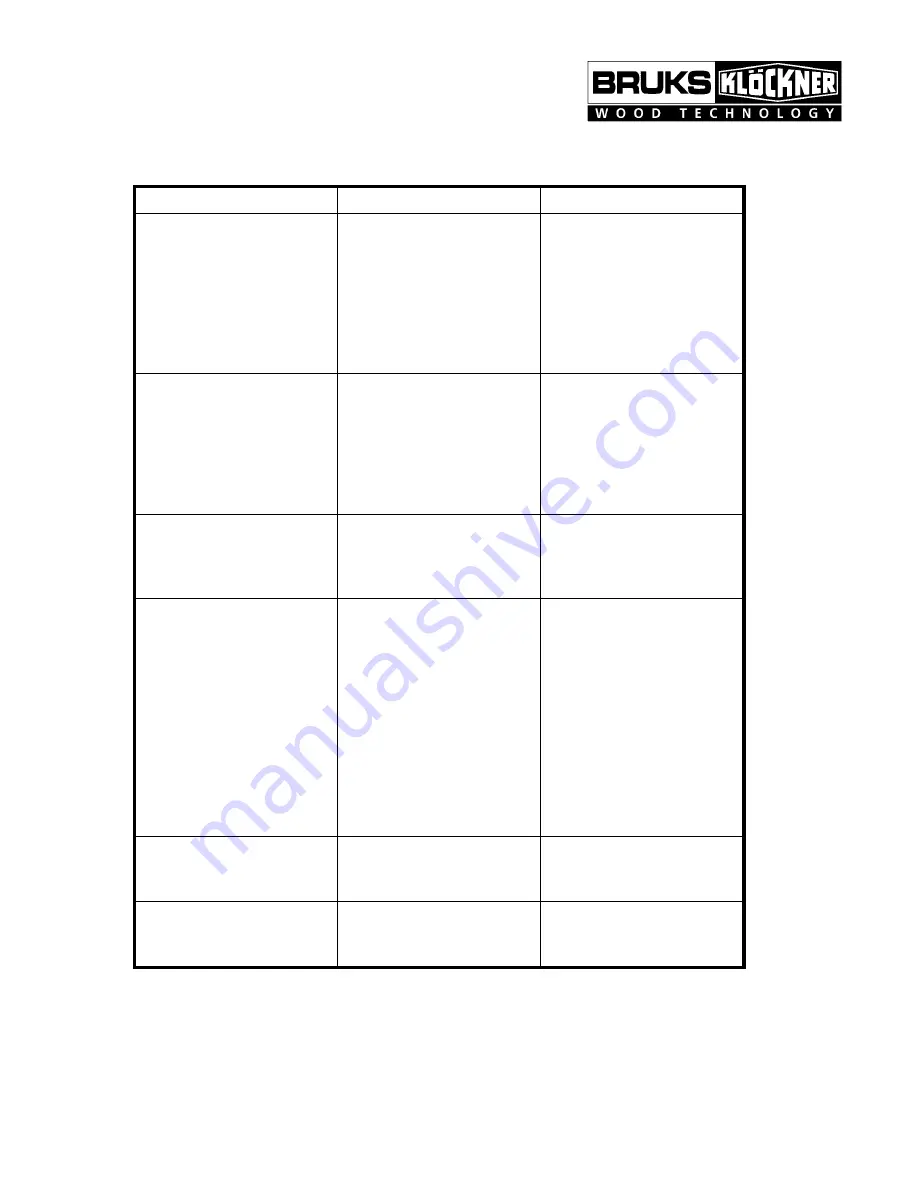
Operating manual 17.410+411
Pos.: 20
Dateiname
Firma
Datum
Rev
BK-DH 700 x 1000 eng.doc
BRUKS-KLÖCKNER
27.02.09
00
Seite 52 von
61
9.2
Problems with the machine
problem
possible cause
suggested solution
rotor slow down
automatic feed control
defective
dull knives
take away conveyor of
inadequate capacity
check controls and repair
if necessary
grind knives
(see chap-
ter „inspection and
maintenance works“)
increase capacity
frequent activation of the
load control
dull knives
load control defective
main motor too small
chipping volume too high
regrind or change knives
check control and repair
if necessary
check and increase mo-
tor power
reduce volume
machine vibrates
imbalance of rotor due to
uneven ground knives
grind all knives in one set
to equal width
(see chap-
ter „inspection and
maintenance“)
unsatisfactory indeed
teeth of feedrolls worn
oil pressure (p3) too high
or too low
gas pressure (p1) wrong
feedroll carrier lowers too
slowly
replace feedrolls
adjust oil pressure (p3)
(see chapter „inspec-
tion and maintenance“)
adjust gas pressure (p1)
(see chapter „inspec-
tion and maintenance
works“)
adjust lowering speed
(see chapter „installa-
tion“)
feedroll carrier stops too
hard
feedroll carrier drops too
fast
adjust lowering speed
(see chapter „installa-
tion“)
gear motor cannot start
lower feedrolls
feedrolls jammed with
material between feedroll
and troughside
remove material re-adjust
trough side with adjusting
screws