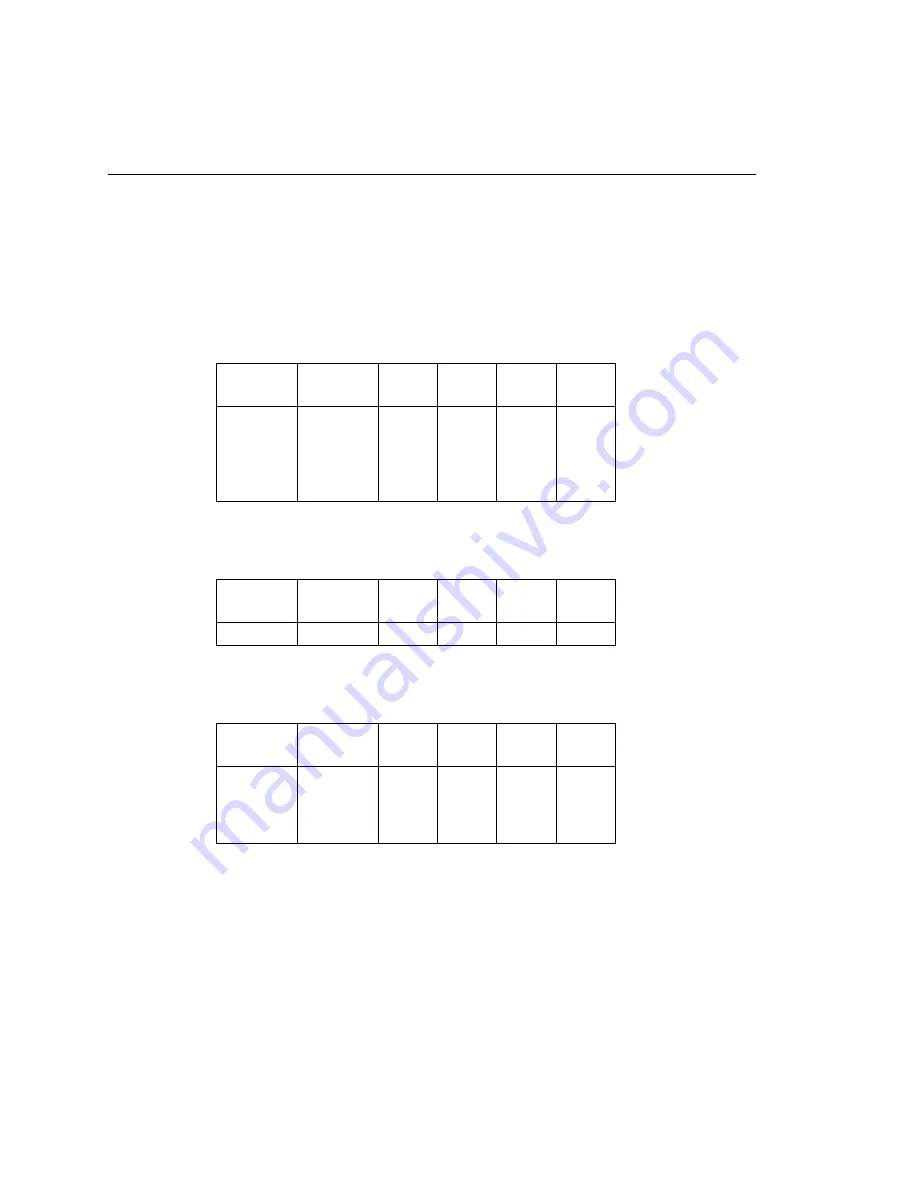
4-22
Troubleshooting
Model 2750 Multimeter/Switch System Service Manual
through
can be used to trace the analog signal through the A/D mul-
tiplexer (U163) to the final amplifier stage. These tables show the MUX lines (S3, S4, S6,
S7) that are selected for measurement during the SIGNAL phase of the multiplexing
cycle. Also included are switching states of analog switches (U129) that set up the gain for
the final amplifier stage (U166).
Table 4-14
DCV signal multiplexing and gain
Range
Signal
(U163)
U129
Pin 1
U129
Pin 8
U129
Pin 9
Gain
(U166)
100mV
1V
10V
100V
1000V
S4
S4
S4
S4
S4
OFF
OFF
ON
OFF
ON
OFF
ON
OFF
ON
OFF
ON
OFF
OFF
OFF
OFF
100
10
1
10
1
Table 4-15
ACV and ACA signal multiplexing and gain
Range
Signal
(U163)
U129
Pin 1
U129
Pin 8
U129
Pin 9
Gain
(U166)
All
S3
ON
OFF
OFF
1
Table 4-16
DCA signal multiplexing and gain
Range
Signal
(U163)
U129
Pin 1
U129
Pin 8
U129
Pin 9
Gain
(U166)
20mA
100mA
1A
3A
S6
S6
S6
S6
OFF
OFF
OFF
OFF
OFF
OFF
OFF
ON
ON
ON
ON
OFF
100
100
100
10
Summary of Contents for 2750
Page 13: ...1 PerformanceVerification...
Page 48: ...1 36 Performance Verification Model 2750 Multimeter Switch System Service Manual...
Page 49: ...2 Calibration...
Page 74: ...2 26 Calibration Model 2750 Multimeter Switch System Service Manual...
Page 75: ...Routine Maintenance 3 RoutineMaintenance...
Page 86: ...3 12 Routine Maintenance Model 2750 Multimeter Switch System Service Manual...
Page 87: ...Troubleshooting 4 Troubleshooting...
Page 111: ...Disassembly 5 Disassembly...
Page 118: ...5 8 Disassembly Model 2750 Multimeter Switch System Service Manual...
Page 119: ...Replaceable Parts 6 ReplaceableParts...
Page 135: ...Specifications A AccuracyandOptimization...
Page 140: ...A 6 Accuracy and Optimization Model 2750 Multimeter Switch System Service Manual...
Page 141: ...Calibration Reference B CalibrationReference...
Page 167: ...Calibration Program C CalibrationProgram...
Page 178: ......
Page 179: ......