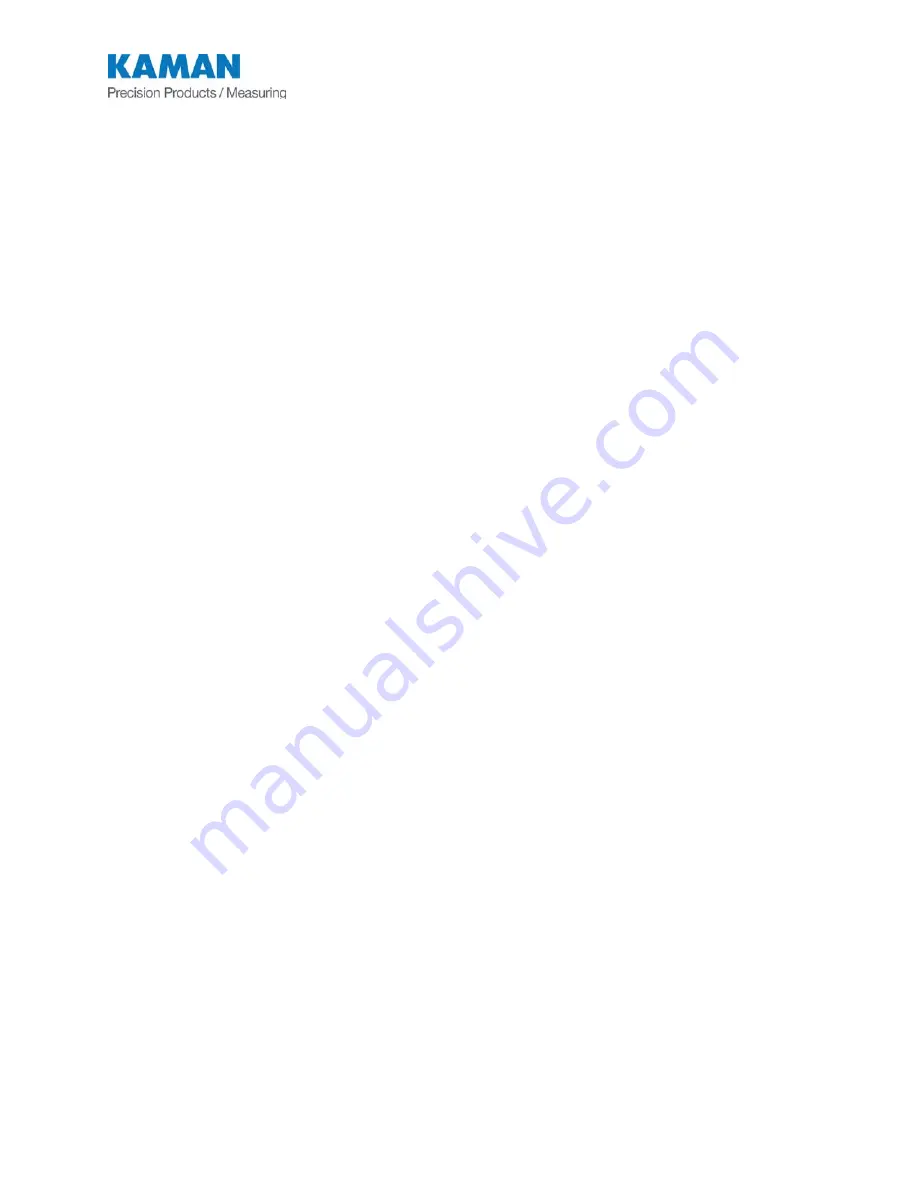
www.kamansensors.com
34
PART NO: 860029-001
Last Revised 01/06/15
Method of Computing Performance
These results are based mainly on simulations. First the sensor inductance and resistance was
computed using a modeling program. Then the effect of 2 meters of cable was factored in
taking in consideration the transmission line effects of the cable. After that the resultant
inductance and resistance was put in a model to simulate the circuit bridge network. The
performance in each case was optimized to provide temperature coefficient as close to .02%FR
as possible while adjusting the parameters for optimal linearity and reasonably good output.
The resulting data was then fit to exponential curves to provide a continuous function of non-
linearity and temperature coefficient vs. coil diameter (and the fit was very good). Finally, the
results were then adjusted slightly based on data from actual systems and engineering
judgment.
This means the system can be adjusted for better temperature coefficient if linearity and
resolution are not a concern. Better resolution can be obtained at the expense of temperature
coefficient. The tradeoffs were made to provide the best overall accuracy. What good is
excellent resolution if the temperature coefficient causes the output to drift out of range?
In general, the results are reasonably accurate from about 10-50% of the coil diameter. Ranges
of less than 10% will have additional errors not accounted for such as thermal expansion of the
sensor body. Ranges less than 10% and greater than 50% will also have errors due to
mismatch in the sensors and electronics.
A Note about Small Ranges
There is a point of diminishing returns when the range is small relative to the coil diameter. At a
range of about 20% of the coil diameter, the amount of change in the measured variable
becomes small rapidly. This causes the inherent output of the system to be reduced such that
as more gain is added in the electronics to compensate, effective resolution does not increase.
In fact, noise as a % of the range starts to increase. Significant errors can also occur from
sensor body thermal expansion and component matching in the electronics. The ‘break even’
point is at a range of about 5% of the coil diameter. This means that reducing the range will not
improve effective performance and dynamic range will be reduced. A range that is too small
also makes it more difficult to set up the sensor within its measurement range.
Other Observations
1.
Performance degrades rapidly when the range exceeds 50% of the coil diameter.
2.
There is a limit (floor) to the resolution and accuracy when operating over very small
ranges (< 5% of the coil diameter).
3.
Optimum performance is obtained with a measuring range approximately 35% of the coil
diameter. This is where the best tradeoff between resolution, non-linearity, and
temperature coefficient will be achieved.