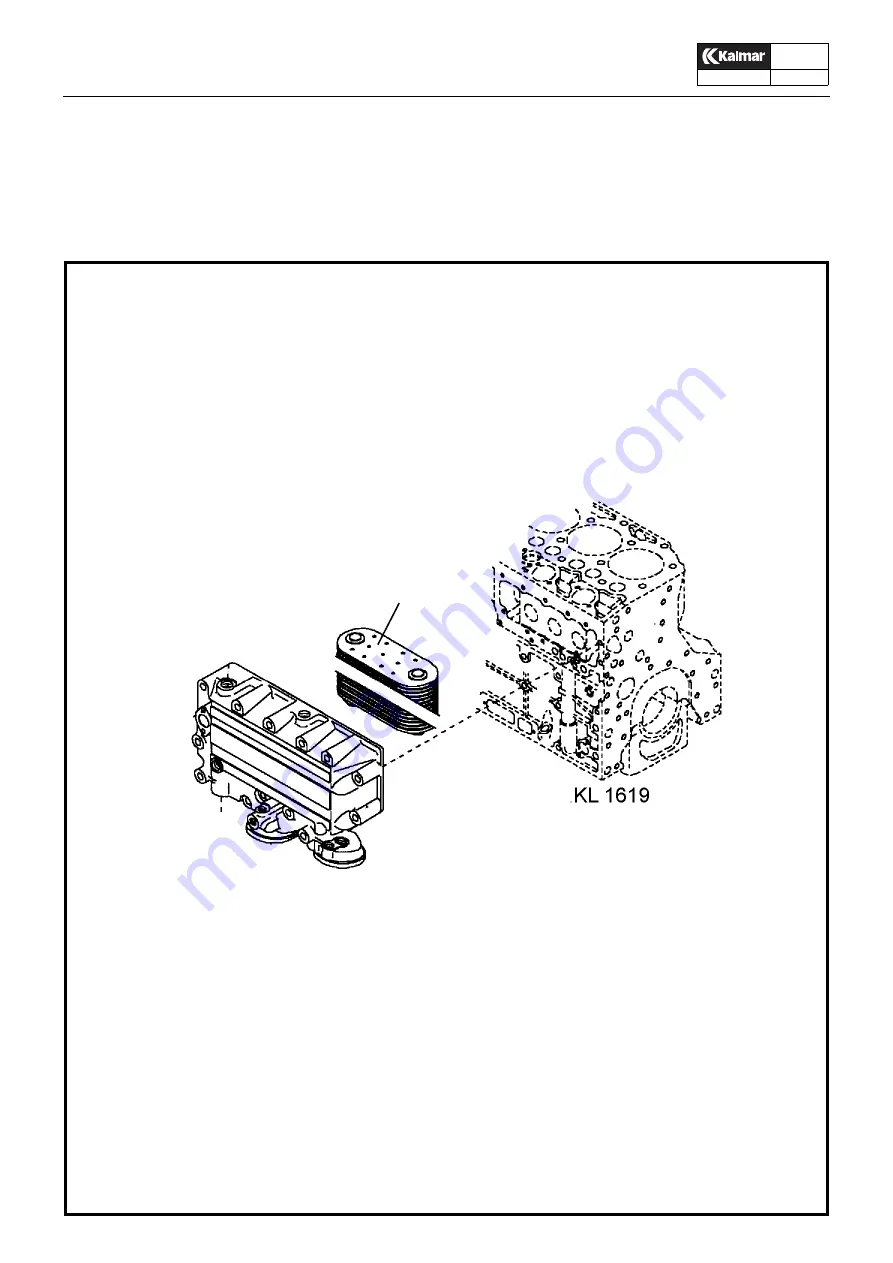
DCE80-100E
Technical Handbook
Engine TAD720VE
Description
23
P.
Group 30
TDCE01
04GB
The cooling system is equipped with a sensor which activates the
”Low coolant level” warning lamp on the instrument panel.
The engine lubricating oil is cooled efficiently and reliably in a
plate oil cooler. The gearbox oil is also cooled by the engine cool-
ant, but in a separate shell-and-tube cooler.
1
1. Plate oil cooler
Summary of Contents for DCE80-100E
Page 2: ......
Page 30: ...DCE80 100E Technical Handbook Empty page 16 P Group 10 TDCE01 04GB ...
Page 43: ......
Page 44: ......
Page 45: ......
Page 46: ......
Page 47: ......
Page 48: ......
Page 49: ......
Page 50: ......
Page 51: ......
Page 52: ......
Page 53: ......
Page 54: ......
Page 55: ......
Page 56: ......
Page 57: ......
Page 58: ......
Page 59: ......
Page 60: ......
Page 61: ......
Page 62: ......
Page 63: ......
Page 64: ......
Page 65: ......
Page 66: ......
Page 67: ......
Page 68: ......
Page 69: ...A35093 0200 04 ...
Page 70: ......
Page 71: ......
Page 72: ......
Page 73: ......
Page 74: ......
Page 75: ......
Page 76: ......
Page 77: ......
Page 78: ......
Page 79: ......
Page 80: ......
Page 81: ......
Page 82: ......
Page 83: ......
Page 84: ......
Page 85: ......
Page 86: ......
Page 87: ......
Page 88: ......
Page 89: ......
Page 90: ......
Page 91: ......
Page 92: ......
Page 111: ......
Page 112: ......
Page 114: ...DCE80 100 Technical Handbook Contents 2 P Group 30 TDCE01 04GB ...
Page 131: ...DCE80 100E Technical Handbook 18 P Group 30 TDCE01 04GB Volvo TAD720VE ...
Page 162: ......
Page 235: ...DCE80 100E Technical Handbook Empty page 43 P Group 70 TDCE01 04GB ...
Page 242: ...DCE80 100E Technical Handbook Empty page 50 P Group 70 TDCE01 04GB ...
Page 243: ...4YFP RS 7YTTPIQIRX HVEYPMG PMRHIVW 8IGLRMGEP ERHFSSO PP 8VYGOW ...
Page 244: ......
Page 246: ......
Page 259: ......
Page 260: ... 4EVXIO SQTER EPQEV RHYWXVMIW 7ZIVMKI 7 0NYRKF 7 IHIR XIP JE OEPQEVMRH GSQ ...
Page 304: ...DCE80 100E Technical Handbook Empty page 2 P Group 90 TDCE01 04GB ...
Page 317: ...DCE80 100E Technical Handbook Empty page 15 P Group 90 TDCE01 04GB ...