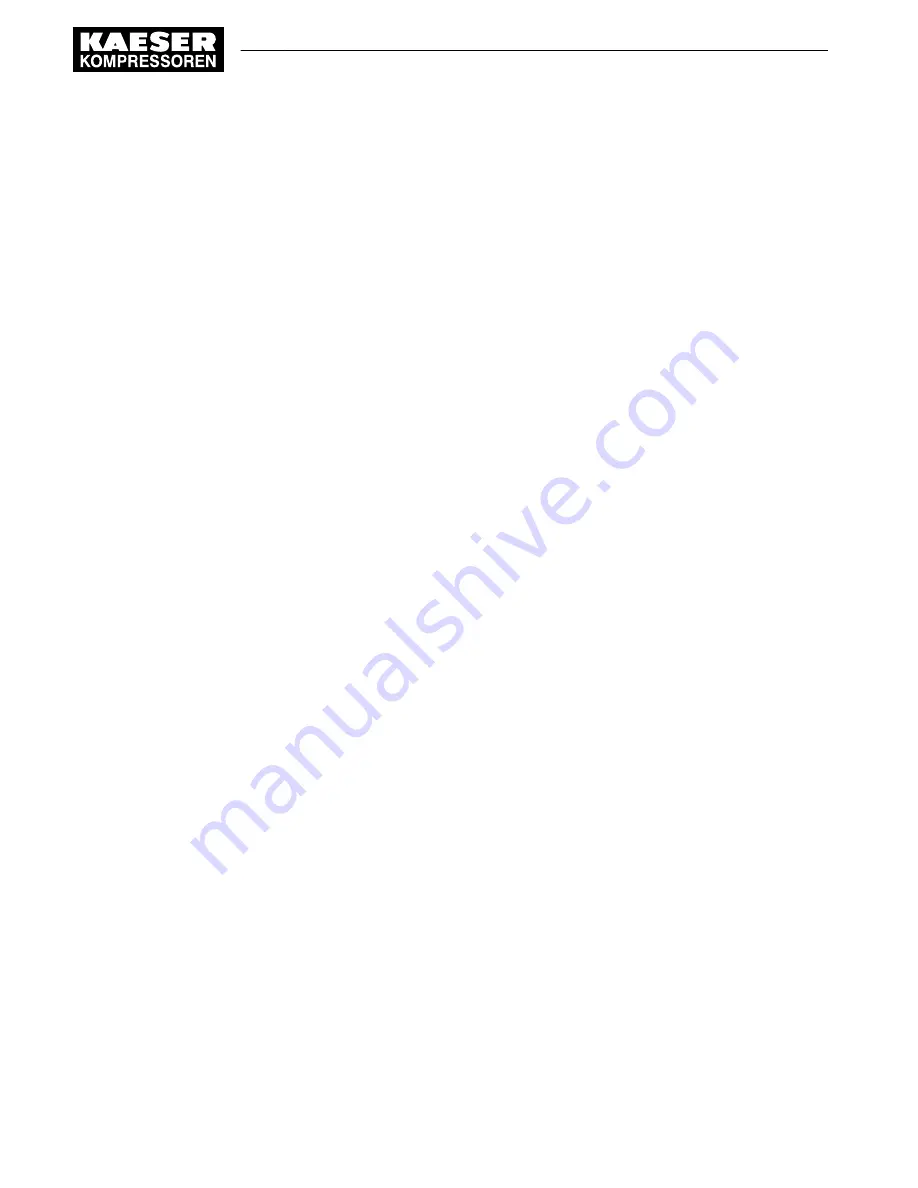
Transport
➤ Use suitable lifting gear that conforms to local safety regulations.
➤ Allow transport only by personnel trained in the safe movement of goods.
➤ Attach lifting gear only to suitable lifting points.
➤ Note the centre of gravity to avoid danger of the load tipping over.
➤ Make sure the danger zone is clear of personnel.
Installation
➤ Make sure no power is applied when electrical connections are made.
➤ Only use only electrical cables that are suitable and approved for the surroundings and electri‐
cal loads applied.
➤ Never dismantle compressed air pipes until they are fully vented.
➤ Only use pressure lines that are suitable and approved for the maximum working pressure and
the intended medium.
➤ Do not allow connection pipes to be placed under mechanical stress.
➤ Do not step onto machine components to climb up the machine.
Positioning
➤ Install the machine in a suitable compressor room.
➤ If installed outdoors, the machine must be protected from frost, direct sunlight, dust, rain and
splashing water.
➤ Do not operate in areas in which specific requirements regarding explosion protection are in
force.
For instance, the requirements of ATEX directive 94/9/EC "Equipment and Protective Systems
intended for use in Potentially Explosive Atmospheres".
➤ Ensure adequate ventilation.
➤ Ensure that required ambient conditions are maintained with regard to:
■ Ambient temperature and humidity
■ Clean inlet air with no damaging contaminants.
■ Inlet air free of explosive or chemically unstable gases or vapours.
■ acid/alkaline forming substances, particularly ammonia, chlorine or hydrogen sulphide.
➤ Do not position the machine in warm exhaust air from other machines.
➤ Ensure accessibility so that all work on the machine can be carried out without danger or hin‐
drance.
Operation
➤ Keep the machine enclosure closed for safety and to ensure correct cooling function.
➤ Carry out regular inspections:
■ for visual damage,
■ of safety devices,
■ of parts needing monitoring.
3
Safety and Responsibility
3.5
Dangers
16
Service Manual Reciprocating compressor
Premium compact W
No.: 9_9418 20E
Summary of Contents for Premium Compact W 200/4
Page 2: ...Original instructions KKW PPWCO 2 00 en SBA PREMIUM COMPACT TRAGBAR 20120822 115136 ...
Page 6: ...Contents iv Service Manual Reciprocating compressor Premium compact W No 9_9418 20E ...
Page 10: ...List of Tables viii Service Manual Reciprocating compressor Premium compact W No 9_9418 20E ...