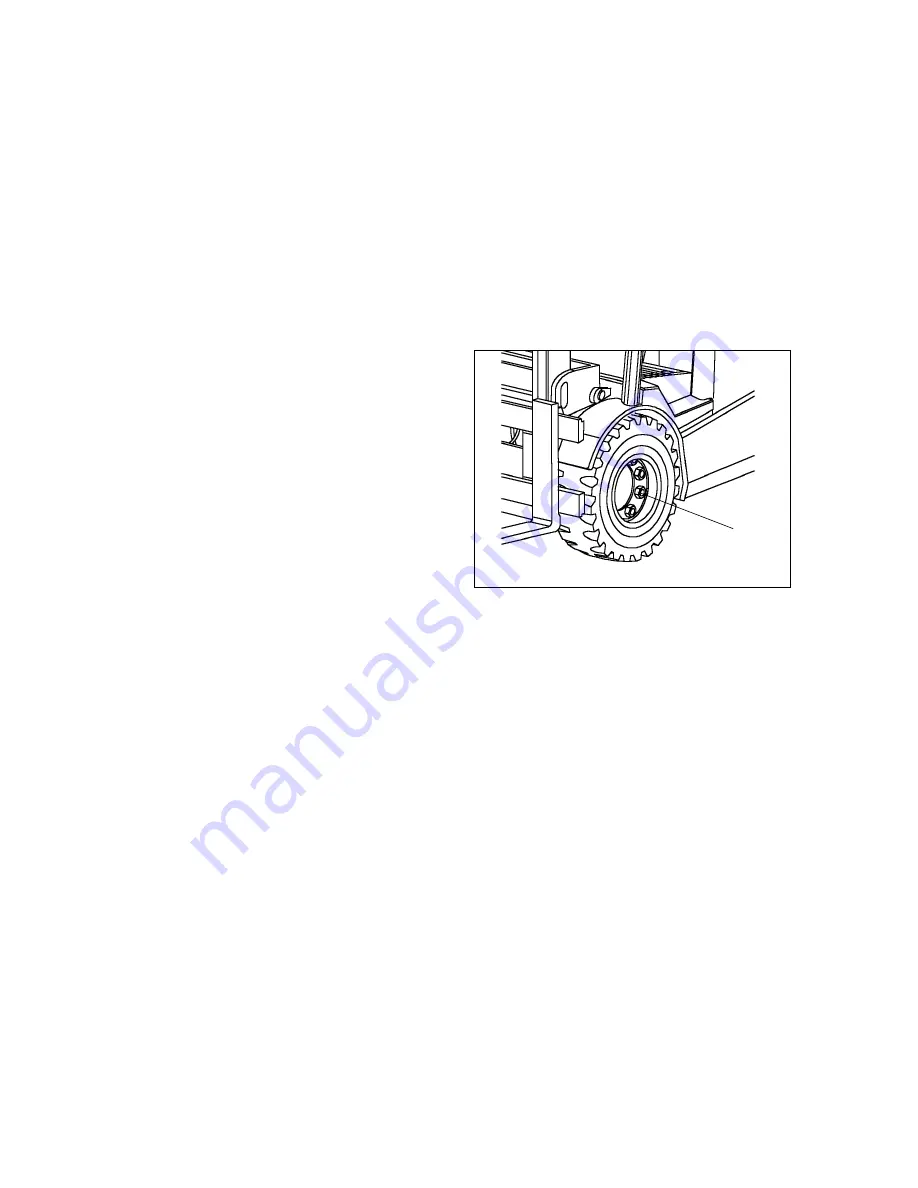
508
2973
- 501
1633
3 GB
F 8
6
Description of servicing and maintenance operations
6.1
Prepare truck for the servicing and maintenance operations
All required safety measures must be taken to prevent any accidents in the course of
the servicing and maintenance operations. The following preparatory operations
must be performed:
– Expose the batteries (refer to chapter D).
6.2
Check attachment of tyres
– Park and lock the truck (refer to
chapter E).
– Crosswise tighten the wheel nuts (1)
with a torque wrench.
Torque
Wheels/Drive axle 6-hole Wheel rim
M
A
= 330 Nm
Wheels/Drive axle 10-hole Wheel rim
M
A
= 220 Nm
Wheels/Steering axle M
A
= 170 Nm
6.3
Tyre pressure
Wheels/Drive axle 10 bar
Wheels/Steering axle 7 - 8 bar
1
508
2973
- 501
1633
3 GB
F 8
6
Description of servicing and maintenance operations
6.1
Prepare truck for the servicing and maintenance operations
All required safety measures must be taken to prevent any accidents in the course of
the servicing and maintenance operations. The following preparatory operations
must be performed:
– Expose the batteries (refer to chapter D).
6.2
Check attachment of tyres
– Park and lock the truck (refer to
chapter E).
– Crosswise tighten the wheel nuts (1)
with a torque wrench.
Torque
Wheels/Drive axle 6-hole Wheel rim
M
A
= 330 Nm
Wheels/Drive axle 10-hole Wheel rim
M
A
= 220 Nm
Wheels/Steering axle M
A
= 170 Nm
6.3
Tyre pressure
Wheels/Drive axle 10 bar
Wheels/Steering axle 7 - 8 bar
1
Summary of Contents for EFG-Vac 22
Page 1: ...Operating instructions 50116333 EFG Vac 22 30 25L S SL G 01 01 12 03...
Page 3: ...0108 GB...
Page 7: ...5082973 50116333 GB I 4...
Page 9: ...5082973 50116333 GB A 2...
Page 15: ...5082973 50116333 GB B 6...
Page 23: ...5082973 50116333 GB B 14...
Page 27: ...5082973 50116333 GB C 4...
Page 35: ...5082973 50116333 GB D 8...
Page 65: ...5082973 50116333 GB E 30...
Page 81: ...5082973 50116333 GB F 16...