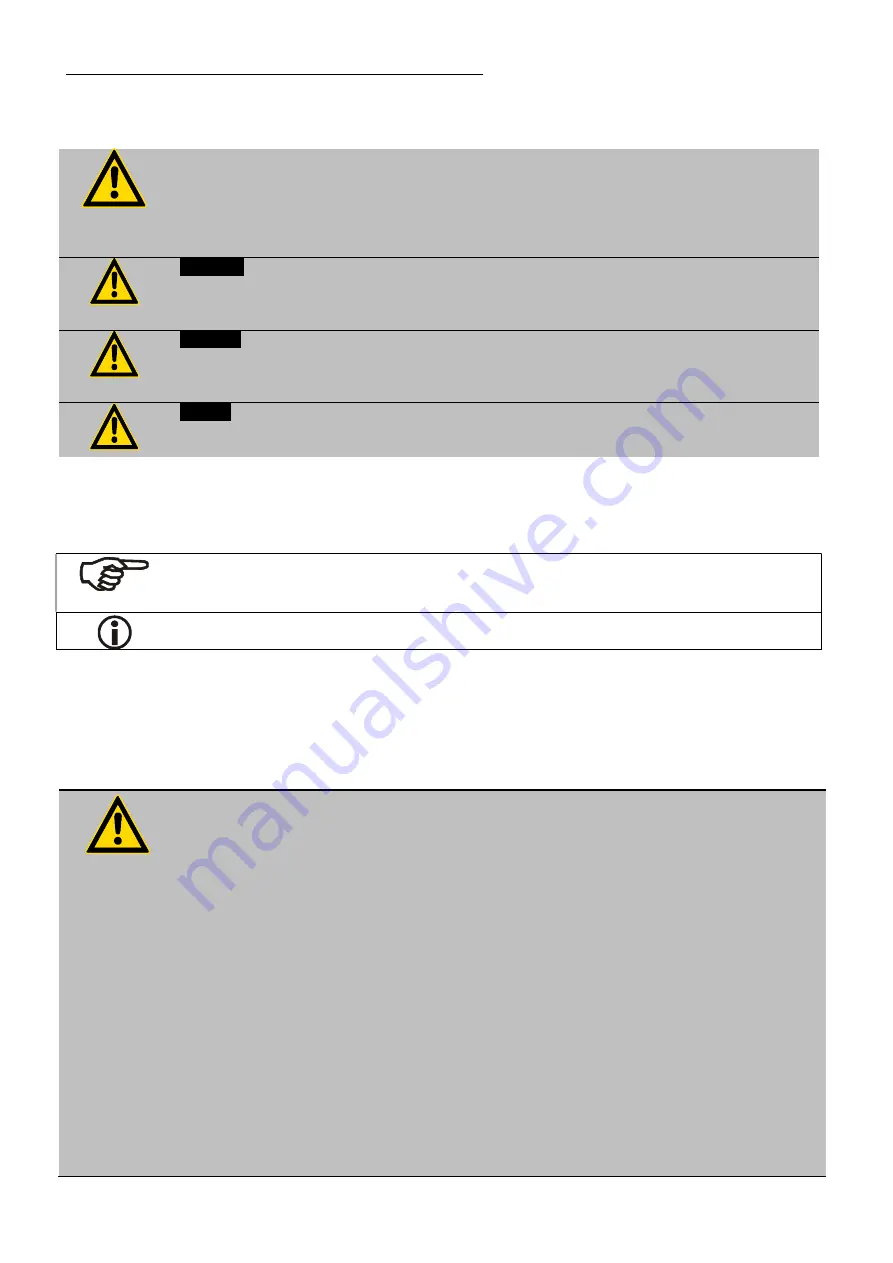
Safety notes for the user
16
4. Safety notes for the user
4.1. Explanation of safety notes
In addition to the safety warnings listed above, warnings are posted throughout the manual.
These warnings are designated by an exclamation mark inside an equilateral triangle.
“Warning of a dangerous situation (Attention! Please follow the documentation).”
The danger is classified using a signal word.
Read and follow these important instructions.
Warning
:
Describes a possibly highly dangerous situation. If these instructions are not followed, serious
injury and danger to life could result.
Caution:
Describes a possibly dangerous situation. If this is not avoided, slight or minor injuries could
result. A warning of possible property damage may also be contained in the text.
Notice:
Describes a possibly harmful situation. If this is not avoided, the product or anything in its
surroundings can be damaged.
4.2. Explanation of other notes
Note!
Draws attention to something special.
Important!
Indicates usage tips and other useful information.
4.3. Safety instructions
Follow the safety recommendations to prevent damage to persons or property. Further, the
valid safety instructions for working places must be followed.
Only connect the unit to a power socket with earthing contact (PE – protective earth)!
The power supply plug serves as safe disconnecting device from the line and must be
always freely accessible.
Place the instrument on an even surface on a pad made of
non-flammable
material.
Do not stay in the area below the unit.
Make sure you read and understand all instructions and safety precautions listed in this
manual before installing or operating your unit.
Set the safety temperature.
Never operate the unit without bath fluid in the bath.
Pay attention to the thermal expansion of bath oil during heating to avoid overflowing of
the fluid.
Prevent water from penetrating into the hot bath oil.
Do not drain the bath fluid while it is hot!
Check the temperature of the bath fluid prior to draining (by switching the unit on for a
short moment for example).
Employ suitable connecting tubing.
Avoid sharp bends in the tubing, and maintain a sufficient distance from surrounding walls.