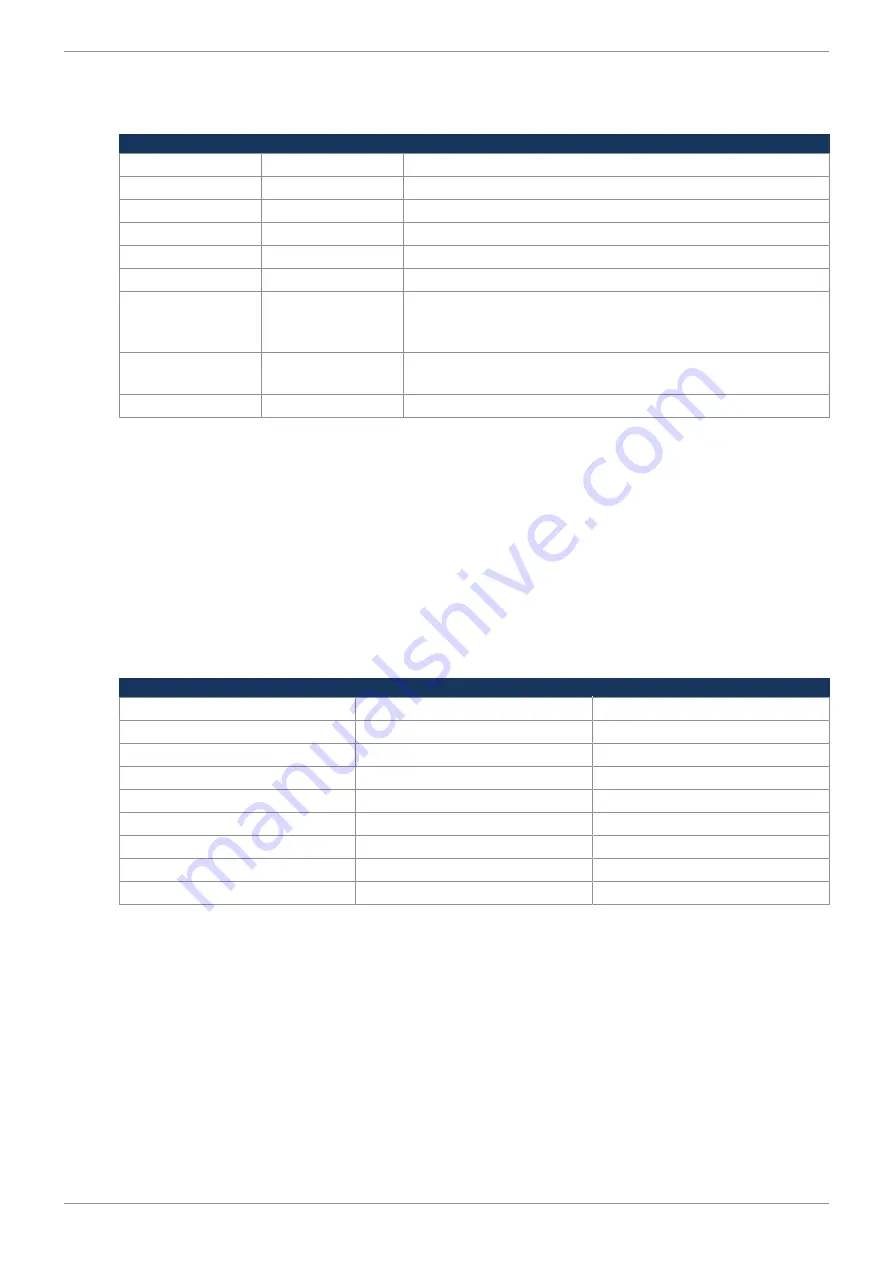
Jetter AG
Programming | 8
jxm-io-ew30_ba_2151_manual
38 / 56
Status of IO interface
Bit
Status
Description
0x00000001
INACTIVE
This port is disabled.
0x00000002
ERROR
An undefined error has occurred.
0x00000004
CONFIG
A configuration error has occurred.
0x00000008
OVERVOLTAGE
Overvoltage is present at the input.
0x00000010
OVERCURRENT Overcurrent is present at the input/output.
0x00000020
SUPPLY_FAULT
The supply voltage VEXT_SEN is not correct.
0x00000080
OPEN_CIRCUIT
There is no load at the output, e.g. in case of cable
breakage. This status entry is only checked while the de-
vice is booting!
0x00000100
TIMEOUT
The time for frequency measurement has been ex-
ceeded.
0x00000200
CC_UNLOCK
The current control is not within the control range.
Tab. 31:
Status of IO interface
8.2 Setting the node ID
The base node ID can be set in the
The configuration inputs (CFG1_IN and CFG2_OUT) generate an offset to the set base node ID.
CFG1_IN and CFG2_OUT may have one of the following 3 states:
■
Jumpered to GND → Low (L)
■
Jumpered to VBAT → High (H)
■
Open → O
The offset corresponds to the values in the following table:
CFG1_IN
CFG2_OUT
Offset of module ID
O
O
0
L
O
1
H
O
2
O
L
3
L
L
4
H
L
5
O
H
6
L
H
7
H
H
8