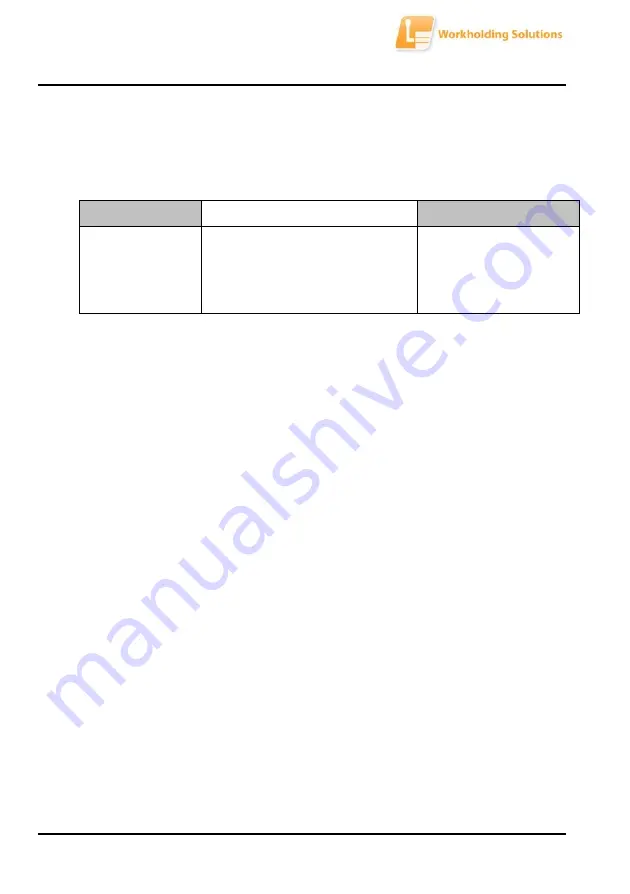
INSTALLATION MANUAL
ZPS-
K5.3,
K10.3, K20.3 CLAMPING
MODULE WITH SENSOR
MONITORING, MOUNTING FLANGE
877.426.2504
SUBJECT TO TECHNICAL CHANGES.
23
JERGENS INC. · PHONE: 216.486.5540 · FAX: 216.481.6193 /553720 / 553721/
7.
POSSIBLE PROBLEMS AND HOW TO REMEDY THEM
The information contained in this section supports the user in
identification of malfunctions that can occur during operation of the
system.
Malfunction
Cause
Remedy
The ZPS no
longer opens
completely
-
Opening pressure is too low.
-
"Reclamping" connection is
not free of pressure
-
Check operating
pressure at the
pressure generator
8.
DECOMMISSIONING AND DISPOSAL
8.1
Decommissioning
If the equipment is no longer going to be used, cut off the system from
the pressure supply and remove it from the production machine on
which it is installed.
8.2
Placing into storage
The following points should be considered:
Clean and grease the surface of the Zero Point System.
Keep the system in a dry environment at +10°C(32°F)
÷
55°C.
8.3
Disposal
If the ZPS is to be scrapped, the oil in it must be emptied and disposed
of in accordance with the applicable legal regulations in the respective
country.
The remaining parts of the pump unit should be sorted by material and
then also disposed of in accordance with the legal regulations.