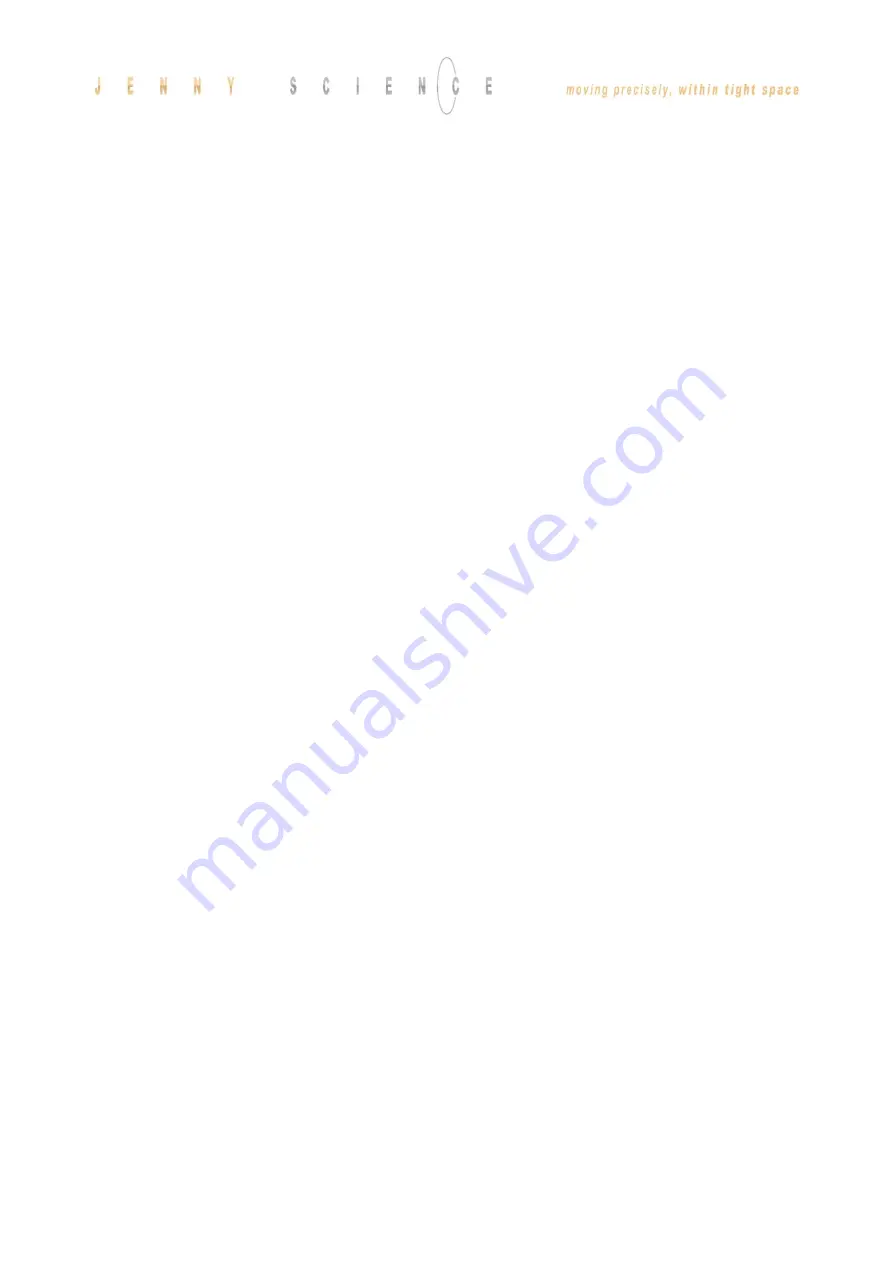
95
14
Error Handling
Errors are displayed on the XENAX
®
servo controller
‘s
7-segment display by flashing a two digit number.
With the command
„>TE“
(Tell Error) they can be
retrieved.
There are 3 different categories to differentiate:
Information
No 0-39
They do not change state of the servo controller. These are
simple status indicators.
Warnings
No 40-49
They can trigger a stop of an active drive (e.g. driving in soft
limit). However, the drive can then be continued without the
need to switch off the output stage.
Errors
No 50-99
Always cause the output stage to switch off. The drive can
only be continued after troubleshooting and error
acknowledgement (Power Quit).
The first information/warning/error is always displayed first. A possible follow-
up error won’t be displayed. Each
warning can overwrite information and each error can overwrite a warning or information. The error history can
be retrieved with ASCII command TEB.
14.1
Error Codes
F-Number
Description
Note
Information
01 to 12
Waiting for input xx (Low od. High)
Keeps driving, if status has been reached or restart with HO, REF,
SM, or PQ, PWC.
20
Command not allowed
Command is not allowed, if an external PLC is controlling the axis.
The command priority of the overriding PLC can be deactivated if
the user set the CANopen Mode of operation to 0 (CANopen Object
0x6060)
21
Force license missing
Calibration value are existing in motor,
but there is no force license active
22
Program start interrupted
Program start is
interrupted through input function “I
NTERRUPT
PROGRAM
”
23
Starting position of motion profile is not
valid
Motion profile (ASCII command “PRF”) can only be started if linear
motor slide is positioned at or behind the starting position of the
motion profile.
24
Index Paramater not valid
One or more parameters of the most previous selected index are
not valid. Please check Acceleration (ASCII-command
„AIX“), Speed
(ASCII-
command „SIX“) and t
ype (ASCII-command
„TYIX“)
of index.
25
Bus module supervision disabled
Bus module is only intended for development purposes. Change
bus module by Jenny Science.
26
Third party motor not configurated or
DIP-switch setting wrong
For Jenny Science Motors (LINAX/ELAX/ROTAX):
For all Jenny Science motors the DIP-switch has to be set on
„LINAX/ELAX/ROTAX“
.
For third party motors:
Please make correct setting for the motor in WebMotion® under
setup
→
motor.
27
Swing Out Reduction Parameter
inconsistency
A new calculation of the target trajectory for swing out reduction
feature can only be initialized after a motor standstill
-> Motor has to be at standstill for at least 1000ms so that a new
set of parameters can be used.