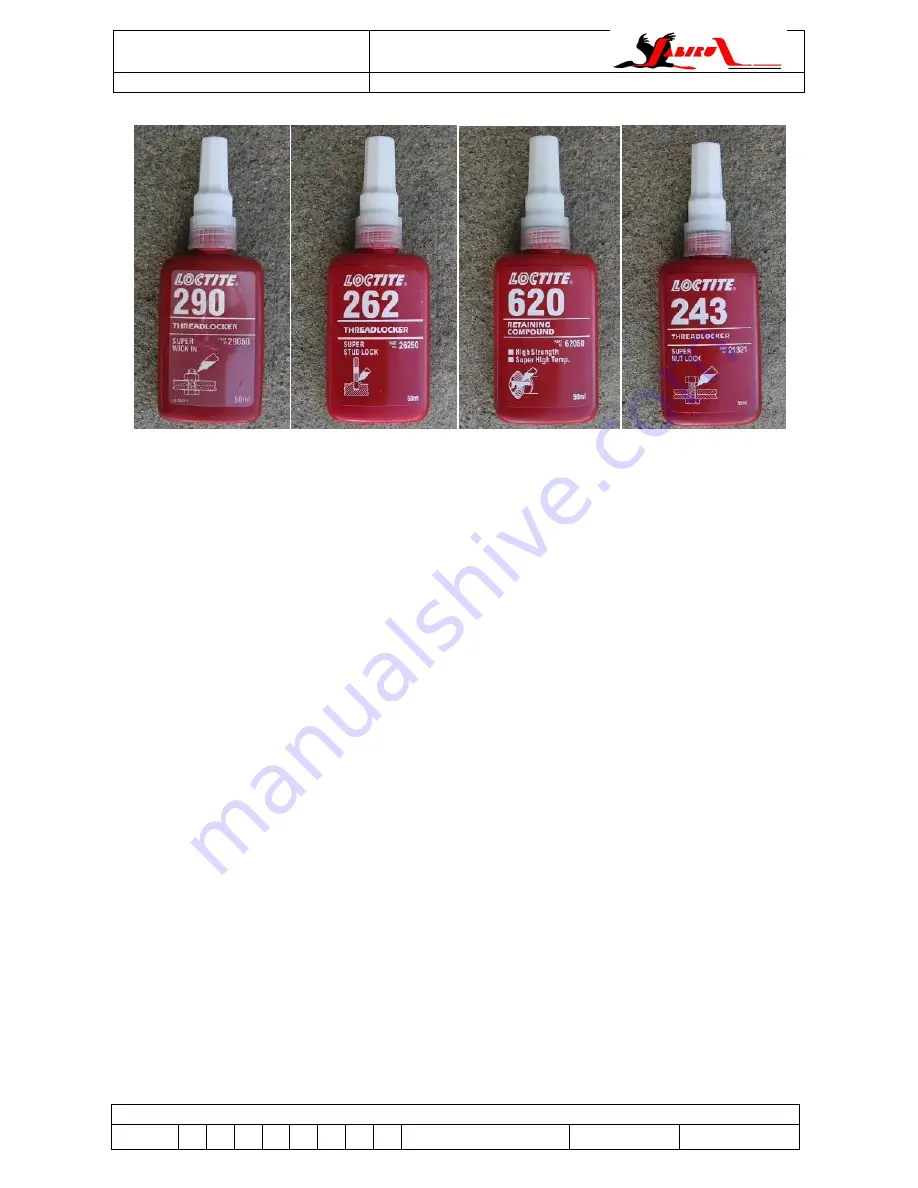
Engine Maintenance Manual
Jabiru Aircraft
Pty Ltd
JEM0002-5
Jabiru 2200 & 3300 Aircraft Engines
This document is controlled while it remains on the Jabiru server. Once this no longer applies the document becomes uncontrolled.
ISSUE
1
2
3
4
5
Dated : 2nd June 2015
Issued By: AS
Page: 35 of 103
L:\files\Manuals_For_Products\Engine_Manuals\Engine Maintenance Manual 22 & 33\JEM0002-5.docx
6.10
Loctite 620 & Other Retaining Compounds
Figure 15
– Sealants, Compounds & Lubricants #3
Loctite 620 is designed for the bonding of cylindrical fitting parts. Typical applications include
locating pins in radiator assemblies, sleeves into pump housings and bearings in auto
transmissions. Particularly suitable for applications where temperature resistance up to 200°C
is required. Used as a ultra-strong threadlock. Loctite 620 is specified in several places in
Jabiru Engine assembly where a reliable bond is essential. When using it, follow the rules
below:
WARNING
Failure to use Loctite 620 correctly can result in engine failure
-
Check use-by dates.
Loctite 620 (like most other compounds used on the engine for
sealing etc) has a use-by date. Generally this is not printed on the bottle but can be found
by contacting the distributor and telling them the batch number.
-
Work fast.
Loctite 620 can cure very quickly. All screws must be torqued to final settings
as quickly as practical. Anything more than a minute is not recommended, particularly if
cure accelerator spray (Loctite 7471) is used.
-
Only use as much as required/specified.
Excess compound can make it nearly
impossible to disassemble the parts later.
-
Surface preparation is critical.
Threads must be cleaned and prepared properly.
-
To Remove.
Can normally be achieved by heating the screw to over 150°C using a pencil-
point gas burner. Minimise direct heat applied to the head of the screw as this can weaken
the drive socket
– direct heat towards the thread as must as possible.
Loctite 290 is designed for the locking and sealing of threaded fasteners. Because of its low
viscosity and capillary action, the product wicks between engaged threads and eliminates the
need to disassemble prior to application. The product cures when confined in the absence of
air between close fitting metal surfaces and prevents loosening and leakage from shock and
vibration. The product can also fill porosity in welds, castings and powdered metal parts.
Loctite 262 is designed for the permanent locking and sealing of threaded fasteners. Typical
applications include the locking and sealing of large bolts and studs (up to M25 ). A medium
strength threadlock.
Loctite 243 is designed for the locking and sealing of threaded fasteners which require normal
disassembly with standard hand tools. Particularly suitable for applications on less active
substrates such as stainless steel and plated surfaces, where disassembly with hand tools is
required for servicing. A medium-strong threadlock. Typically used for cap screws into castings
or Aluminium.