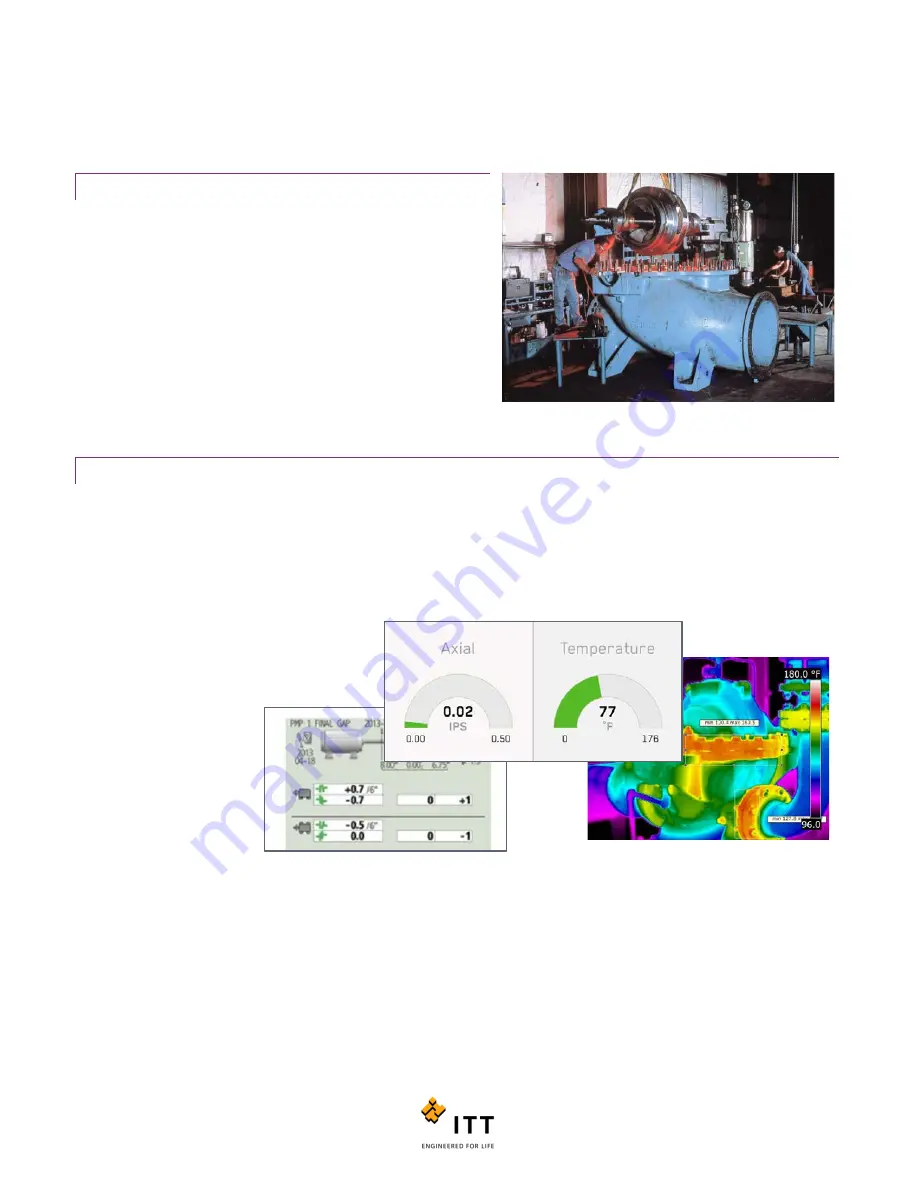
i-ALERT2 Application Guide
11 of 64
If process data is available from the control system it should be overlaid with the vibration/temperature trends of the i-
ALERT2
to help determine root cause. Often the root cause of a vibration problem is a process upset.
STEP 3.RESOLVE: CORRECTION AND IMPROVEMENT
After determining the root cause of the problem, it can be
corrected. Cost effective corrective actions will depend on the
machine in question and the findings of the failure analysis. In
order to maximize the reliability of the machine in question, it is
also advisable to improve the vibration levels on the machine to
“precision state” levels after it has been repaired. This will extend
the life of the machine.
STEP 4.DOCUMENT
After determining the root cause of the problem, correcting the problem and improving the machine, it is important to
verify
that the correction/improvement has occurred and document the findings. One mechanism for this verification is
comparing the vibration levels after restarting the machine with those taken before shutdown and the original baseline
data. Other common verification methods include:
o
Measuring reduced energy consumption
o
Capturing Infrared Thermography Images
o
Oil analysis
o
Confirming precision alignment
Figure 7: Document results to verify corrective action was effective
Figure 6: Precision repair at an ITT PRO Service center
Summary of Contents for i-ALERT2
Page 1: ...Application Guide...
Page 2: ...i ALERT2 Application Guide 2 of 64...
Page 32: ...i ALERT2 Application Guide 32 of 64 Figure 27 Devices in range and out of range...
Page 58: ...i ALERT2 Application Guide 58 of 64 Figure 57 Route Report Trend Details Screen...
Page 63: ...i ALERT2 Application Guide 63 of 64...
Page 64: ...i ALERT2 Application Guide 64 of 64 G iALERT2AppGuide en US 2016 10...