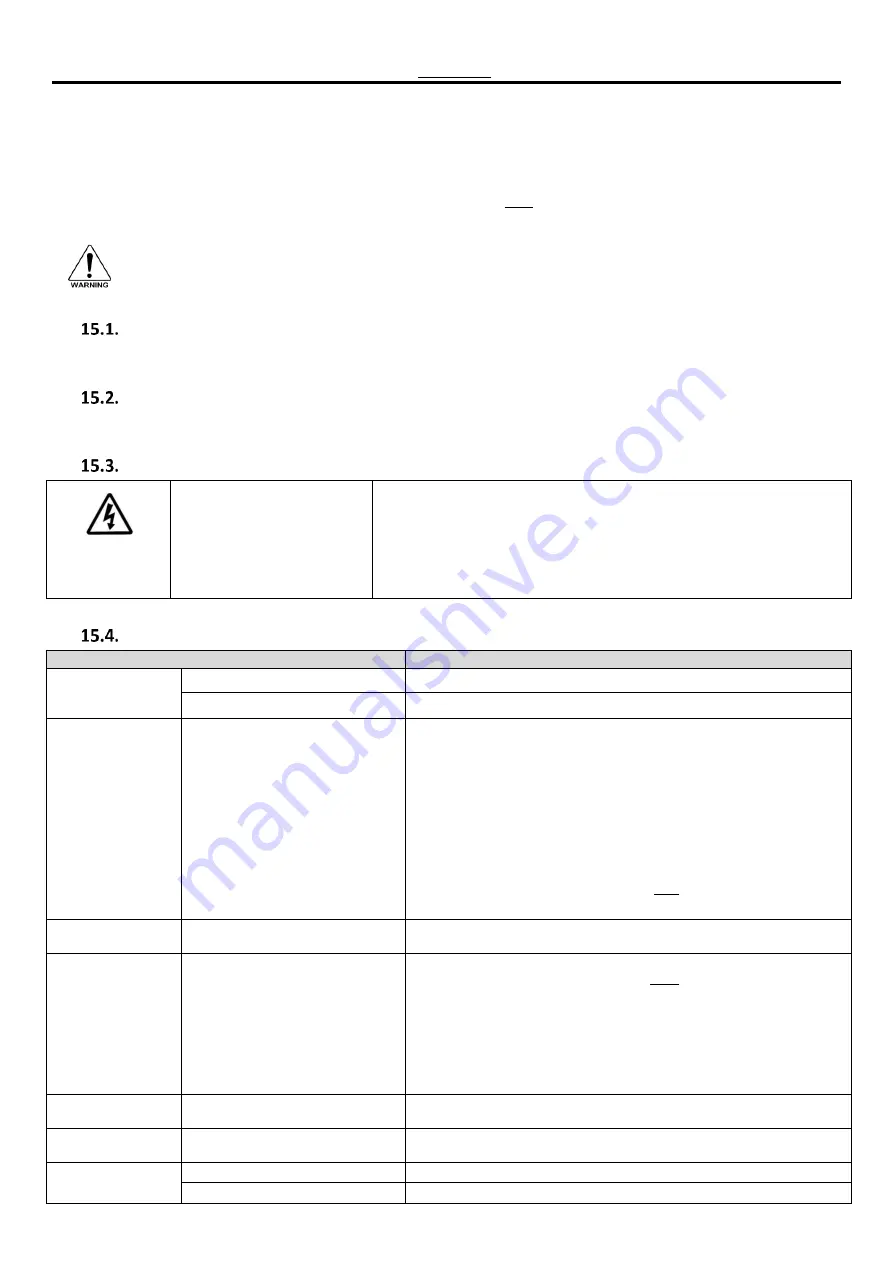
Optidrive P2 Elevator User Guide V2.30
51
Gearless (Permanent Magnet) Motors-Without Encoder (P4-01=3).
www.InvertekDrives.com
15.
Gearless (Permanent Magnet) Motors-Without Encoder (P4-01=3).
Open loop operation of a gearless (PM) motor is intended as a method of motor operation without an encoder, this allows for a means of
confirming that the motor direction and encoder signal direction matches during first start-up of the elevator system, furthermore this
function can be used to bring the elevator car to a required position in the shaft should the encoder feedback be lost, it should be noted that
the motor control performance will not be as per Closed loop operation.
In all applications, to ensure good performance and safe control over the motor and connected load, it is essential to ensure that the drive
parameters are adjusted to suit the connected motor. Following this, an autotune must be carried out, this allows the drive to measure the
data required for correct control of the connected motor.
Whilst the autotune procedure does not rotate the motor shaft, the motor shaft may still turn if the motor holding brake is
not applied. It is not normally necessary to uncouple the load from the motor; however the user should ensure that no risk
arises from the possible movement of the motor shaft.
Step 1- Wiring Connections.
Make wiring connections as per detailed in section 12.1 “Step 1- Wiring Connections.” But without making encoder connections.
Step 2- Pre-Power Checks.
Perform Pre-Power checks as per detailed in section 12.2 “Step 2- Pre-Power Checks.”
Step 3- Apply Power.
Apply Electrical
Power to the drive
Apply rated voltage to the
drive.
Check that the drive displays
or
.
If
or
is not shown refer to the troubleshooting section at the
back of the user manual.
Step 4- Motor nameplate data entry.
Action
Additional Information
Select Gearless
(Permanent Magnet)
motor control mode
Set P1-14 to 201
Advanced Parameter Access.
Set P4-01 to 3
Both IPM and SPM type motors are supported.
Enter motor back-
EMF voltage value
From motor datasheet Enter the
Phase to Phase back-EMF value (at
motor rated speed).
If the back-EMF value is not
available from the motor datasheet
then enter calculated value as shown
opposite.
If the back-emf value is not available it can be approximated as per the
following calculation :
P1-07 = Motor Rated Power / Motor Efficiency / Motor Power factor /1.732 / Motor
rated Current.
(Typical values are 0.95 for Motor efficiency and 0.90 for Motor power factor).
Example: Motor rated Power = 7.2kW
Motor Efficiency = 0.95, Motor Power
factor (Cos
Ø
) = 0.9, Motor rated current = 16.9A.
Therefore: P1-07 = 7200/0.9/0.9/1.732/16.9 = 304V
Note: Incorrect value can result in abnormal motor operation (motor vibration).
Enter Motor
Rated Current
Enter value into P1-08
Obtained from Motor nameplate (Amps).
Enter Motor
Rated Frequency
Enter value into P1-09
Note: The drive uses P1-09 to calculate the number of motor pole pairs.
Motor Poles (Pair) = P1-09*60/ P1-10, the result must equal a whole number (zero
decimal places e.g. 12 and not 12.3) :
For non-whole number frequencies e.g. 6.82Hz, then choose next whole number for
P1-09 and recalculate accordingly :
Next whole number (7)/Pole pairs*60 = New rated speed value (P1-10).
Enter Motor
Rated Speed
Enter value into P1-10
Obtained from Motor nameplate (rpm)
Set Motor
Switching Frequency
Set P2-24 to 16kHz
16kHz provides optimum motor control.
Set PM Motor
boost values
Set P7-14 to 25%
Boost Current Level
Set P7-15 to 10%
Boost Frequency